試作は、製品開発において最も重要な段階の 1 つです。しかし、迅速かつコスト効率の高い試作に適した材料と方法を見つけるのは困難な場合があります。シリコン成形は優れたソリューションとして際立っていますが、なぜメーカーや設計者がシリコン成形を優先するのでしょうか。この記事では、シリコン成形が試作に最適な理由、その利点、次の大きなプロジェクトでシリコン成形を活用する方法について詳しく説明します。
シリコン成形は、柔軟性、耐久性、使いやすさから、試作によく使用されます。正確で機能的な試作品を迅速かつ低コストで作成できるため、本格的な生産前に設計をテストするのに最適です。 新しい製品のアイデアをテストする場合でも、部品の複数のバージョンが必要な場合でも、シリコン成形によりプロセスが簡素化されます。
さて、なぜこの方法が高く評価されているのか、そしてそれがプロトタイピングのニーズにどのような変化をもたらすのかを見てみましょう。
シリコン成形とは一体何でしょうか?
シリコン成形とは、金型を使用してシリコン素材を希望の形状に成形するプロセスを指します。素材自体は柔軟性に優れているため、さまざまなプロトタイプの用途に最適です。しかし、このプロセスは具体的にどのように機能するのでしょうか。
まず、マスターモデル(多くの場合、3D プリントまたは機械加工)を作成し、その周りにシリコン型を作ります。型が固まったら、シリコン材料を流し込んで最終プロトタイプを作成します。完成した作品は最終製品の特性を再現できるため、フィット感や機能から外観や感触まですべてをテストできます。
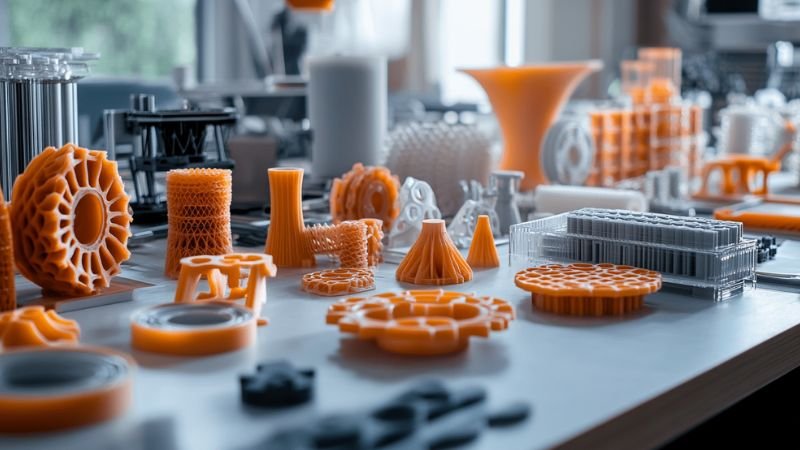
シリコン成形がプロトタイプ作成に最適な理由
プロトタイプ作成においては、時間と費用が決定的な要素となることがよくあります。シリコン成形が両方の分野で優れている理由は次のとおりです。
1. 少量生産でもコスト効率が良い
少量の試作品の場合、シリコン成形は従来の製造方法に比べて手頃なオプションです。 セットアップコストの削減、これは、お金をかけずに機能的なプロトタイプを素早く作成したい人にとって最適なツールです。
2. 迅速な対応時間
試作ではスピードが重要です。シリコン型を使用すると、射出成形などの他のプロセスに比べて生産時間を短縮できます。通常、 シリコン型は数日で完成します迅速な反復とテストからの迅速なフィードバックが可能になります。
3. 素材の多様性
シリコンには、食品グレード、医療グレード、工業グレードなどさまざまなグレードがあり、さまざまなプロトタイプのニーズに幅広く対応できます。 現実世界のアプリケーションをシミュレートするのに理想的な素材です 柔軟性と耐久性が重要になります。
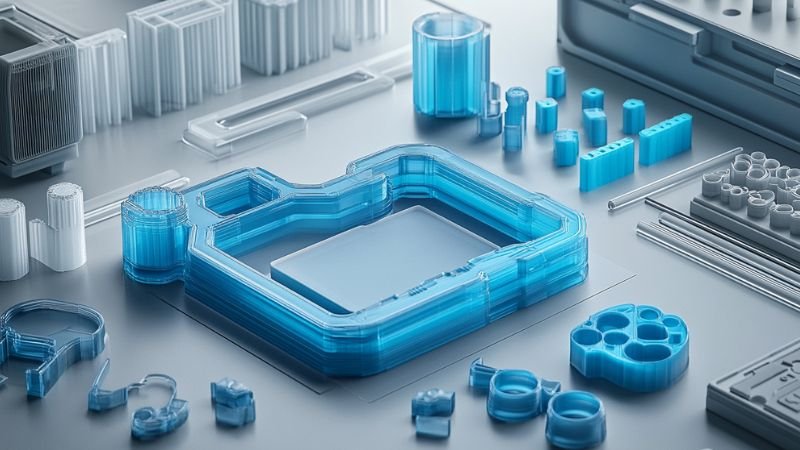
プロトタイプ作成におけるシリコン成形の利点
プロトタイプ作成にシリコン成形を使用する主な利点を分析してみましょう。
1. 高精度と細部までこだわった
シリコン成形の大きな利点の一つは、細かいディテールを再現できることです。シリコンは、どんなに小さな特徴でも再現することができます。 信じられないほどの正確さ複雑な部品や複雑な形状のテストに最適です。
2. 優れた耐久性と柔軟性
シリコン素材は耐久性と柔軟性に優れています。これらの特性は、次のようなアイテムの試作に特に役立ちます。 ガスケット、シール、またはフレキシブル部品 耐久性とストレス下でのパフォーマンスをテストする必要があります。
3. 複雑な形状に最適
従来の方法とは異なり、シリコン成形は複雑な形状やアンダーカットのある部品に最適です。プロトタイプに珍しい角度や複雑なデザインが必要な場合は、 シリコン成形により、他のプロセスでは実現が難しい形状を作成できます。
4. 短いリードタイム
シリコン型の作成が簡単なため、リードタイムが大幅に短縮されます。デザインのプロトタイプを 1 か月ではなく 1 週間で作成する必要がある場合、シリコン型を使用すればそれが実現できます。
シリコン成形の仕組みをステップごとに解説
シリコン成形プロセスが具体的にどのように機能するのか疑問に思うかもしれません。以下に詳しく説明します。
- マスターモデルを作成する: これは、3D プリントまたは CNC 加工を使用して行うことができます。
- 型を準備するマスターモデルを容器に入れ、その上に液状シリコンゴムを注ぎます。
- シリコンを硬化させる: シリコン混合物を固めて硬化させ、マスターモデルを完全に反映した型を形成します。
- プロトタイプを成形するシリコン型が準備できたら、必要な材料(樹脂、ワックス、シリコンなど)を型に注ぎ、プロトタイプを形成します。
このプロセスは迅速に実行できるため、迅速な反復とテストが可能になります。

試作用シリコン成形の種類
一般的なシリコン成形プロセスは比較的シンプルですが、望ましい結果に応じてバリエーションがあります。プロトタイプ作成で使用される最も一般的なタイプは次のとおりです。
1. 圧縮成形
圧縮成形では、シリコン材料を加熱した金型キャビティに入れて圧縮します。これは、堅牢性と耐久性が求められる部品に適しています。
2. 射出成形
やや大規模な生産の場合は、シリコンを使用した射出成形が使用されることがあります。シリコンは圧力をかけた状態で金型に注入されるため、高い精度が確保され、無駄が最小限に抑えられます。
3. トランスファー成形
この方法は、圧縮成形と射出成形を組み合わせたもので、制御された圧力下でシリコンを金型に注入します。
シリコンプロトタイピングの実際の応用
シリコンプロトタイピングは、自動車からヘルスケアまで、さまざまな業界で使用されています。シリコン型が特に役立つ実際のアプリケーションをいくつか見てみましょう。
- 医療機器: シリコンは毒性がなく柔軟性があるため、カスタムインプラントや義肢などの医療機器のプロトタイプをテストするのに最適です。
- 消費者製品: キッチンツール、ベビー用品、ウェアラブル テクノロジーなど、シリコン型を使用すれば、これらすべての高品質なプロトタイプを作成し、最終製品のパフォーマンスをシミュレートできます。
- 工業用部品航空宇宙や自動車などの業界では、大規模生産に移る前に、シリコンプロトタイプを使用してシール、ガスケット、または複雑なコンポーネントをテストできます。
シリコンプロトタイピングと従来の方法
シリコン成形は、3D プリントや従来の射出成形などの他の試作方法と比べてどうですか?
- 料金: シリコン成形は、通常、少量生産の場合、射出成形よりも安価です。
- スピード: 大きな部品では時間がかかる可能性がある 3D プリントとは異なり、シリコン型では処理時間が短くなります。
- 材料特性: 3D プリントでは、特に現実世界の機能をテストする場合、シリコンが提供する柔軟性や耐久性が不足する可能性があります。
つまり、シリコン成形は、速度、コスト、材料特性の間で最適なバランスを実現しており、多くの業界でプロトタイプ作成に好まれる選択肢となっています。
結論
シリコン成形は、精度、柔軟性、手頃な価格を独自に組み合わせた、プロトタイプ作成に最適な方法です。新しい製品設計をテストする場合でも、生産に向けてプロトタイプを微調整する場合でも、シリコン成形は、作業を迅速かつコスト効率よく完了するために必要な俊敏性を提供します。