Les produits en silicone sont largement utilisés dans de nombreux domaines en raison de leurs caractéristiques non toxiques, insipides, de résistance aux hautes températures, de performances stables, etc. Dans notre vie quotidienne, les produits en silicone peuvent être trouvés partout, de l'alimentation des bébés en silicone aux ustensiles de cuisine en silicone, de des pièces automobiles aux équipements médicaux, et des produits de beauté aux biens de consommation, comme les jouets et les cadeaux en silicone.
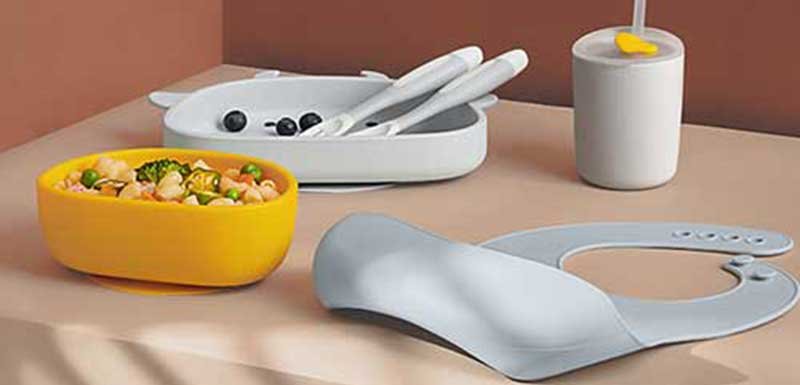
Les produits en caoutchouc de silicone sont les bienvenus non seulement en raison de leurs propriétés physiques de haute qualité, mais également parce que leur structure chimique est basée sur une alternance d'unités de silicium et d'oxygène. Ils peuvent être fabriqués avec différentes bases organiques et carbonées, ainsi que des additifs et des charges intégrés dans leur structure moléculaire pour créer des produits avec différentes formes, duretés ou élasticités, couleurs, transparences, résistances à la déchirure, résistance aux contraintes environnementales ou mécaniques, etc.
Comment fabriquer des produits en silicone ?
En tant que fabricant professionnel de produits en silicone avec de nombreuses années d'expérience dans l'industrie, les processus de fabrication du silicone Ruiyang comprennent :
- Moulage par compression
- Moulage par injection de caoutchouc de silicone liquide
- Moulage par injection de caoutchouc à haute consistance
- Moulage par extrusion
- Moulage par calandrage
- Moulage par transfert
Le choix du processus à utiliser varie d'un produit à l'autre en fonction de la complexité de la structure du produit en silicone, de sa taille, de sa quantité, de son coût, des besoins particuliers en matière de performances, etc. Par conséquent, il est essentiel de comprendre les matériaux et les processus de fabrication pour optimiser le produit en silicone. qualité, productivité et cohérence. Examinons de plus près ces méthodes.
Moulage par compression
Le moulage par compression est une méthode très courante pour traiter le silicone. Cela se fait principalement par l’ajustement du moule, et la forme du moule détermine la forme du produit en silicone. Le silicone est généralement moulé par des moules à haute température. Tout d’abord, les matières premières solides en silicone sont mélangées à un agent de vulcanisation. Ensuite, le matériau est pressurisé à travers le vulcanisateur pour remplir toute la cavité et vulcanisé à haute température, et le chauffage et la pression sont maintenus jusqu'à ce que le silicone soit durci. Au cours de ce processus, le caoutchouc de silicone reste quelque peu flexible et la dureté du silicone moulé se situe généralement entre 30°C et 70°C. Ce procédé de fabrication est relativement simple et applicable à la majorité des produits en silicone.
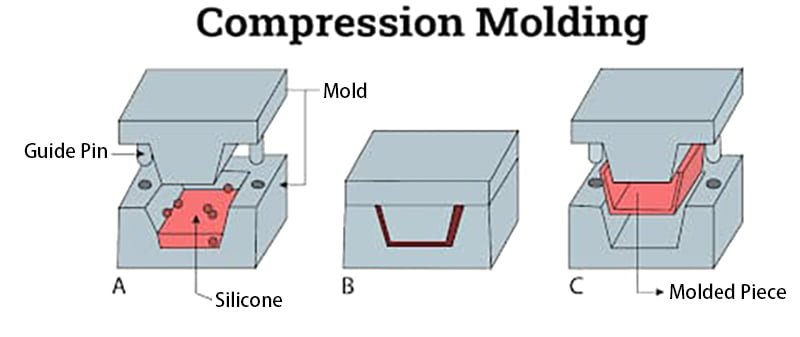
Les avantages du moulage par compression comprennent
- Coût d’outillage réduit
- Moins de gaspillage de matières premières
- Rentable, en particulier pour les grandes pièces et les commandes à volume élevé
- Convient aux petites pièces et aux formes plus complexes
- Large gamme d'applications, notamment les claviers d'ordinateur, les ustensiles de cuisine, les pièces électriques et certains équipements médicaux et dentaires.
Types de produits en silicone moulés par compression
Produits en silicone pour bébé, produits en silicone pour la cuisine, articles ménagers, joints, joints d'étanchéité, joints toriques, valves à bec de canard en silicone, pièces automobiles personnalisées en silicone, etc.
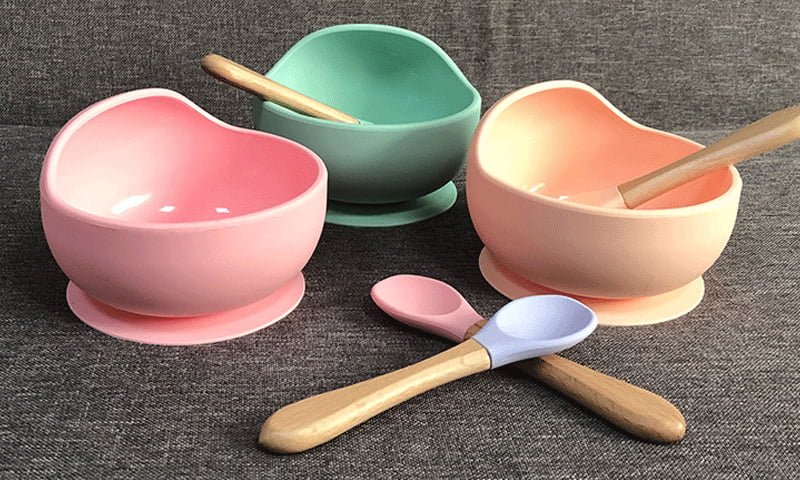
Moulage par injection
Le moulage par injection est plus complexe que le moulage par compression, le moulage par transfert ou le moulage par extrusion. Des temps de durcissement courts et une faible viscosité font du moulage par injection un excellent choix pour une grande variété de produits en silicone. La conception du moule, la taille des portes et l'emplacement sont des facteurs clés dans l'optimisation du processus de moulage par injection.
L’utilisation du procédé de moulage par injection présente les avantages suivants :
- S'adapter à une production en grand volume
- Plusieurs matériaux peuvent être utilisés en même temps
- Peut être automatisé
- Faible prix de production par composant
- Cycle de moulage court
- Aucune préparation préfabriquée requise
- Avec une conception de moule correcte, aucun découpage n'est requis
- Très adapté aux produits nécessitant une tolérance dimensionnelle ou une uniformité
Bien entendu, en plus des avantages, il convient également de prêter attention à certains points lors du processus d'utilisation du moulage par injection pour fabriquer des produits en silicone.
- Solins, déformations, bulles, bosses
- Un volume d'injection insuffisant empêchera la partie du moule de se remplir
- Dans les moules multi-empreintes, équilibrez les portes pour optimiser le flux de matière
- Une ventilation avec un remplissage rapide et des temps de mise au point courts peut être nécessaire pour éliminer l'air emprisonné
- Le rafraîchissement des mélanges de matériaux avant le moulage améliore le rendement des pièces
- Gardez la cavité propre et identifiez
- Durcissement du produit
- Idéal pour les produits à parois minces
Types de produits moulés en silicone par injection
Petites pièces de précision, pièces automobiles, fournitures de natation, appareils de cuisine
Moulage par injection de caoutchouc de silicone liquide (LSR)
Le caoutchouc de silicone liquide est un silicone durci à deux composants de haute pureté, renforcé de silice spécialement traitée. Il a des exigences relativement élevées en matière de solidité, de résistance et de haute qualité. Le LSR est moins visqueux que le HCR, ce qui en fait un matériau pompable idéal pour le moulage par injection de liquides.
La principale différence entre le LSR et le HCR réside dans la nature « fluide » ou « liquide » du matériau LSR. De plus, alors que le HCR peut utiliser des procédés de durcissement au peroxyde ou au platine, le LSR n'utilise que des additifs au platine. En raison de la nature thermodurcie du matériau, le moulage par injection LSR nécessite une manipulation spéciale telle qu'un mélange distributif intensif tout en maintenant le matériau à basse température avant qu'il ne soit poussé dans une cavité chauffée et vulcanisé.
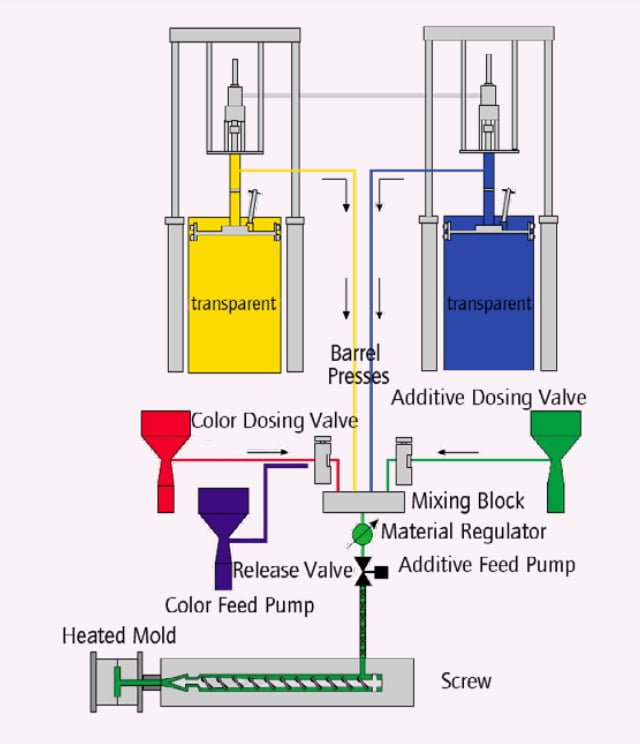
Comment fonctionne le procédé de moulage par injection LSR et quels sont ses avantages ?
L'injection LSR, comme son homologue HCR, est utilisée pour créer un produit final moulé dans une cavité. Le procédé LSR utilise un liquide non chauffé ou un matériau visqueux qui est pompé à travers une buse d'injection dans la cavité du moule. La matière première est simplement transportée sous pression dans la cavité chauffée et fermée, remplissant la cavité en un instant. De par sa simplicité, le moulage par injection LSR est une méthode de fabrication très rapide, utilisant un doseur pour tirer directement du fût, avec des délais d'exécution rapides, idéal pour produire des pièces de très gros volumes.
Principaux avantages de l’injection LSR
- Cycles de moulage courts et précis
- Production de masse
- Traitement efficace et économique
- Large gamme d'utilisations, peut fabriquer une variété de produits généraux
- Durcissement rapide et excellent démoulage
Moulage par injection de caoutchouc à haute consistance (HCR)
Le caoutchouc à haute consistance (HCR) est également connu sous le nom de caoutchouc durci à la chaleur ou de caoutchouc de silicone HTV (vulcanisé à haute température). Ce matériau est constitué de silicone réactif contenant des macromolécules de très haut poids.
Diverses matières premières peuvent fournir des fonctions spécifiques au HCR, telles que la silice fumée ou la silice précipitée avec une surface spécifique élevée pour améliorer les propriétés mécaniques, un stabilisant thermique, un plastifiant ou un agent anti-recombinaison.
Les élastomères HCR surpassent les élastomères organiques traditionnels, offrant une résistance mécanique supérieure dans la plage de températures de -50°C à +300°C. Ils ont également de bonnes propriétés de vieillissement, sont chimiquement inertes, sont stables lorsqu’ils sont exposés à la lumière ou à l’oxygène et sont facilement colorés et même transparents, ce qui les rend idéaux pour les applications d’emballage alimentaire et d’aide médicale.
L'incorporation de divers additifs dans le HCR ouvre la voie à des solutions personnalisées illimitées pour les applications existantes et nouvelles dans diverses industries. Aérospatiale, automobile, soins de santé, pétrole et gaz, construction, électronique, véhicules électriques, etc.
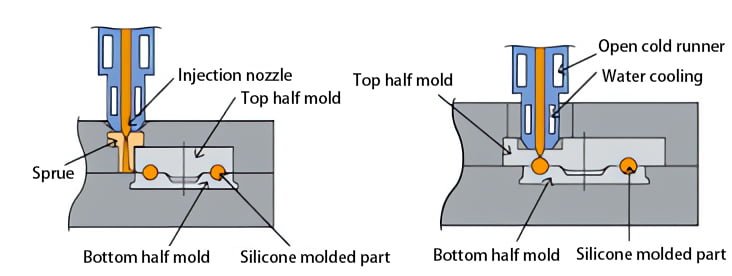
Comment fonctionne le processus de moulage par injection HCR et quels avantages apporte-t-il ?
Le HCR dosé est injecté directement du cylindre dans le moule chauffé fermé via le mécanisme à vis et la buse, à travers la porte. Le matériau remplit et remplit la cavité du moule, formant la pièce.
Les principaux avantages du moulage par injection HCR
- Cycles de moulage courts et précis
- coût unitaire inférieur
- Moins de gaspillage de matière
- Possibilité de moulage avec d'autres matériaux comme le plastique ou le métal
- En termes de produits finis, la production est stable
- Précision et remplissage supérieurs de pièces complexes par rapport au moulage par compression ou par transfert.
- Il s’agit sans doute de la méthode de formage la plus courante et la plus puissante, dans laquelle les produits peuvent varier considérablement en taille, en complexité et en application.
La différence entre le moulage par compression et le moulage par injection
Le moulage par compression et le moulage par injection sont similaires dans le sens où ils remplissent tous deux des cavités préformées, mais ils diffèrent par le fait que les moules à compression sont directement pré-remplis de charge, alors que dans le moulage par injection, la charge est préalablement injectée entièrement dans une cavité fermée.
Fabricants de différents types de pièces utilisent souvent à la fois le moulage par compression et par injection, mais pour différents types de pièces. En général, le moulage par injection est préféré pour la fabrication de pièces plus complexes (et souvent plus petites), tandis que la compression fonctionne très bien pour les conceptions simples ou basiques et les grandes pièces qui ne peuvent pas être produites par extrusion.
D'autres points de comparaison incluent : le moulage par injection a des temps de cycle plus courts et est donc généralement plus rapide et plus rentable pour les produits en grand volume, tandis que le moulage par compression est principalement utilisé pour les pièces en série de faible à moyenne production.
Moulage par extrusion
Les produits en silicone extrudés sont généralement formés par une extrudeuse. L'extrusion de caoutchouc de silicone est généralement utilisée pour la fabrication de tuyaux, de câbles, de profilés complexes et de pièces à section transversale, de composants souvent assez longs, souvent multicouches, ainsi que de tiges, de joints de four, de câbles, d'isolation de fils, de joints, d'étanchéité. .
Les tubes en silicone sont largement utilisés dans les équipements médicaux et mécaniques. Il peut également être utilisé comme tampon pour les matériaux d’emballage.
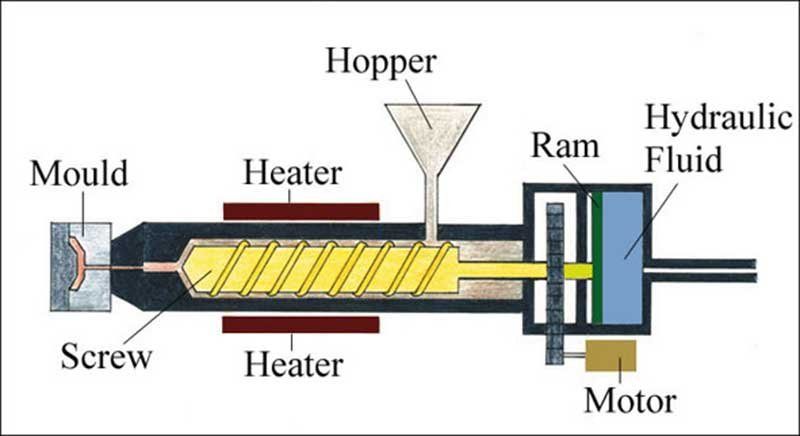
Le procédé utilise un composé HCR avec un catalyseur, préfabriqué en bandes ou en blocs. La préforme est ensuite introduite dans une extrudeuse à vis qui force le composé à travers une filière en acier trempé avec un motif de coupes. Le silicone façonné passe ensuite à travers une chambre chauffée sur une bande transporteuse et est durci dans un four à tirage continu.
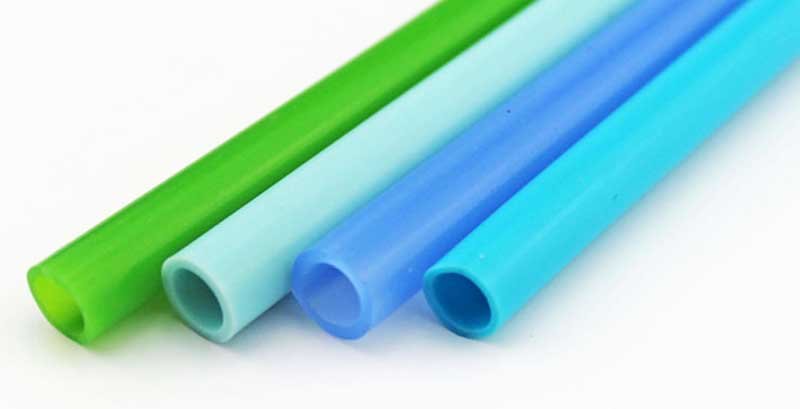
Le principal défi pour les fabricants utilisant cette technologie est de savoir comment sélectionner la qualité appropriée de caoutchouc de silicone et le système de catalyseur adapté pour fonctionner de manière optimale dans un processus mécanique spécifique, à température et vitesse contrôlées et pour que le produit final soit conforme aux spécifications, aux normes de tolérance et le respect des normes réglementaires.
Calandrage du caoutchouc de silicone
Le calandrage est un processus mécanique qui consiste à comprimer et à lisser le matériau de manière continue en déplaçant la feuille à travers des paires de rouleaux chauffés. Ces ensembles de doubles ou multiples couches de rouleaux en acier dur sont appelés calendriers. Ils sont ajustés sous pression pour produire une épaisseur, une finition de surface et une texture prédéterminées et uniformes du caoutchouc de silicone qui peuvent être brillantes, mates, lisses, adhésives ou gaufrées, etc.
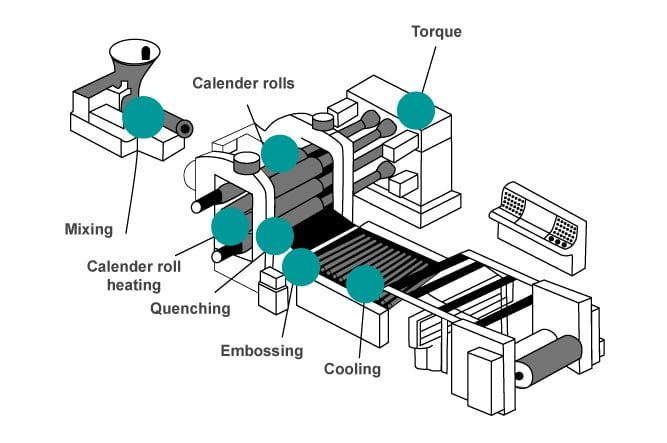
La matière première, généralement du HCR, qui détermine les propriétés mécaniques du produit fini, est préalablement ramollie ou extrudée à chaud, puis forcée à travers des rouleaux cylindriques disposés en rangée. Le processus de calandrage comprime la préforme de silicone non durcie en une feuille de silicone continue. Les silicones peuvent ensuite être pressées sur divers substrats tels que des revêtements antiadhésifs ou liées à divers tissus, verre, plastiques, etc.
Les principaux avantages du traitement de calandrage comprennent
- Traitement continu et en grand volume de produits de haute qualité
- Plaques autoportantes (non supportées) livrées dans une doublure de protection ou produits associés à d'autres matériaux, notamment des tissus organiques ou synthétiques (polyamide, viscose, polyester, etc.), du verre, du plastique, etc.
- Il existe des applications presque infinies, allant des revêtements pour la construction aux produits ménagers, en passant par les vêtements, les décorations, les produits en contact avec les aliments, les bandes transporteuses industrielles, les produits autoclavables pour les applications médicales, et bien plus encore.
Moulage par transfert de caoutchouc de silicone
Le moulage par transfert est similaire au moulage par compression à plusieurs égards. Il utilise du HCR, qui est pressé depuis une chambre auxiliaire (appelée réservoir de transfert) dans un système de moule fermé sous pression qui intègre un récipient chauffé au-dessus du moule, entraîné à l'aide d'un piston. Le caoutchouc de silicone est rempli d'un système unique de porte et de canal qui peut se déplacer. matériaux relativement durs dans le moule avant de les chauffer. Le processus de moulage par transfert de caoutchouc de silicone est idéal pour fabriquer des pièces moulées en silicone de haute précision et pour « empiler » avec d’autres matériaux afin de permettre le moulage de géométries complexes. La combinaison des processus HCR et de moulage par transfert peut produire des pièces de haute qualité, offrant une flexibilité de conception et des cycles de production plus courts.
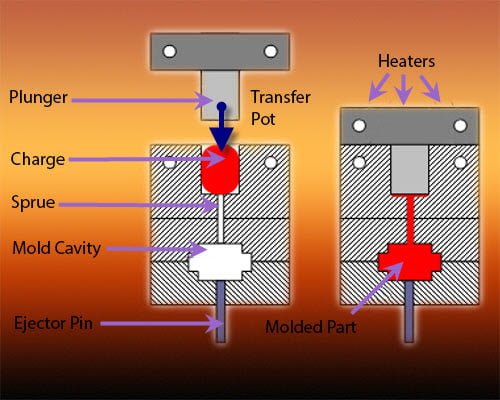
Le moulage par transfert diffère du moulage par compression dans la mesure où le moule est complètement fermé plutôt que divisé en deux parties. Pour cette raison, il diffère également du moulage par injection dans la mesure où des pressions plus élevées sont nécessaires pour remplir le moule. Cela permet également au moulage par transfert d'accepter des fibres ou une matrice ajoutées dans sa couche externe pour produire des pièces renforcées sur mesure.
Les principaux avantages du processus de moulage par transfert
- Coûts d’outillage réduits
- Pièces uniformes, précises et plus cohérentes par rapport au moulage par compression grâce au moule monobloc et à la tolérance dimensionnelle élevée
- Capacité efficace et agile pour accepter différentes fibres de renfort prépositionnées dans le moule, notamment le verre, le carbone et l'aramide, ainsi que des fibres végétales naturelles.