シリコン製品は、無毒、無味、耐高温性、安定した性能などの特徴から、多くの分野で広く使用されています。私たちの日常生活では、シリコン製のベビーフードからシリコン製のキッチン用品、自動車部品から医療機器、美容製品からシリコン製のおもちゃやギフトなどの消費財まで、あらゆる場所でシリコン製品を見つけることができます。
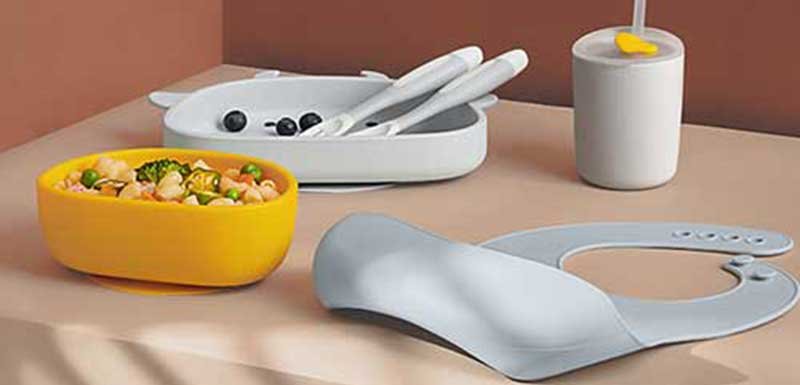
シリコンゴム製品は、その高品質の物理的特性だけでなく、シリコンと酸素の交互の単位に基づく化学構造によっても歓迎されています。さまざまな有機および炭素ベース、および分子構造に統合された添加剤と充填剤を使用して製造することができ、さまざまな形状、硬度または弾性、色、透明性、引裂強度、環境または機械的ストレスに対する耐性などを備えた製品を作成できます。
シリコン製品の製造方法は?
業界で長年の経験を持つシリコーン製品の専門メーカーとして、Ruiyang シリコーンの製造プロセスには以下が含まれます。
- 圧縮成形
- 液状シリコーンゴム射出成形
- 高濃度ゴム射出成形
- 押し出し成形
- カレンダー成形
- トランスファー成形
使用するプロセスの選択は、シリコン製品の構造の複雑さ、サイズ、数量、コスト、特別な性能要件などに応じて、製品ごとに異なります。したがって、シリコン製品の品質、生産性、一貫性を最適化するには、材料と製造プロセスを理解することが重要です。これらの方法を詳しく見てみましょう。
圧縮成形
圧縮成形は、シリコーンを加工する非常に一般的な方法です。主に金型のフィットによって行われ、金型の形状によってシリコーン製品の形状が決まります。シリコーンは通常、高温金型で成形されます。まず、固体シリコーン原料を加硫剤と混合します。次に、材料を加硫機で加圧してキャビティ全体に充填し、高温で加硫させます。加熱と圧力は、シリコーンが硬化するまで維持されます。このプロセス中、シリコーンゴムはある程度柔軟性を保ち、成形されたシリコーンの硬度は通常30°C〜70°Cです。この製造プロセスは比較的簡単で、ほとんどのシリコーン製品に適用できます。
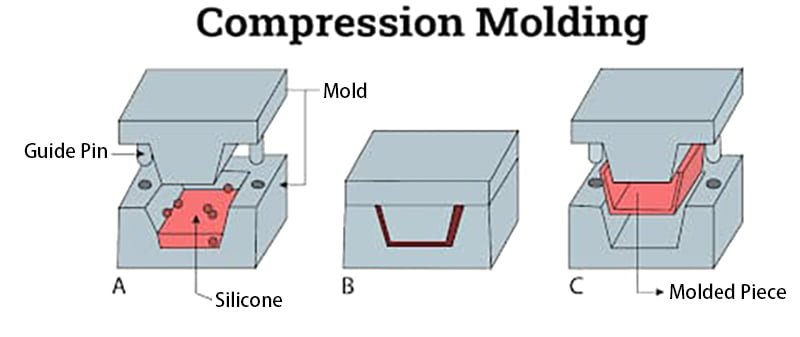
圧縮成形の利点は次のとおりです。
- ツールコストの削減
- 原材料の無駄を減らす
- 特に大型部品や大量注文の場合、コスト効率に優れています
- 小型部品や複雑な形状に適しています
- コンピュータのキーボード、キッチン用品、電気部品、一部の医療機器や歯科機器など、幅広い用途に使用できます。
圧縮成形シリコーン製品の種類
ベビー用シリコン製品、キッチン用シリコン製品、家庭用品、ガスケット、シーリングガスケット、Oリング、シリコンダックビルバルブ、シリコンカスタム自動車部品など。
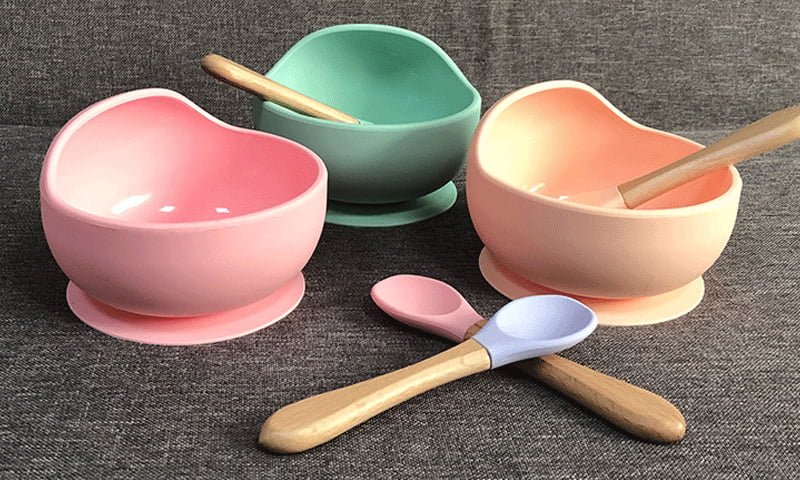
射出成形
射出成形は、圧縮成形、トランスファー成形、または押し出し成形よりも複雑です。硬化時間が短く、粘度が低いため、射出成形はさまざまなシリコン製品に最適です。金型の設計、ゲートのサイズ、および位置は、射出成形プロセスを最適化するための重要な要素です。
射出成形プロセスを使用すると、次のような利点があります。
- 大量生産に適応
- 複数の材料を同時に使用できる
- 自動化可能
- 部品あたりの生産価格が低い
- 短い成形サイクル
- プレハブの準備は不要
- 正しい金型設計であればトリミングは不要
- 寸法公差や均一性が求められる製品に最適です
もちろん、利点に加えて、射出成形を使用してシリコーン製品を製造するプロセスでは注意する必要がある点もいくつかあります。
- はみ出し、反り、気泡、へこみ
- 射出量が不十分だと金型部品が充填されない
- マルチキャビティ金型では、ゲートのバランスをとって材料の流れを最適化します。
- 閉じ込められた空気を除去するために、高速充填と短いフォーカス時間による換気が必要になる場合があります。
- 成形前に材料混合物をリフレッシュすると、部品の歩留まりが向上します。
- 空洞を清潔に保ち、
- 製品の硬化
- 薄肉製品に最適
射出成形シリコーン製品の種類
小型精密部品、自動車部品、水泳用品、キッチン家電
液状シリコーンゴム(LSR)射出成形
液状シリコンゴムは、特殊処理されたシリカで強化された高純度の 2 成分硬化シリコンです。強度、耐性、高品質に対する要件は比較的高くなっています。LSR は HCR よりも粘性が低いため、液体射出成形に最適なポンプ可能な材料です。
LSR と HCR の主な違いは、LSR 材料の「流動性」または「液体」の性質です。また、HCR では過酸化物またはプラチナ硬化プロセスを使用できますが、LSR ではプラチナ添加剤のみを使用します。材料の熱硬化性のため、LSR 射出成形では、材料を加熱されたキャビティに押し込んで加硫する前に、材料を低温に保ちながら強力な分散混合を行うなどの特別な処理が必要です。
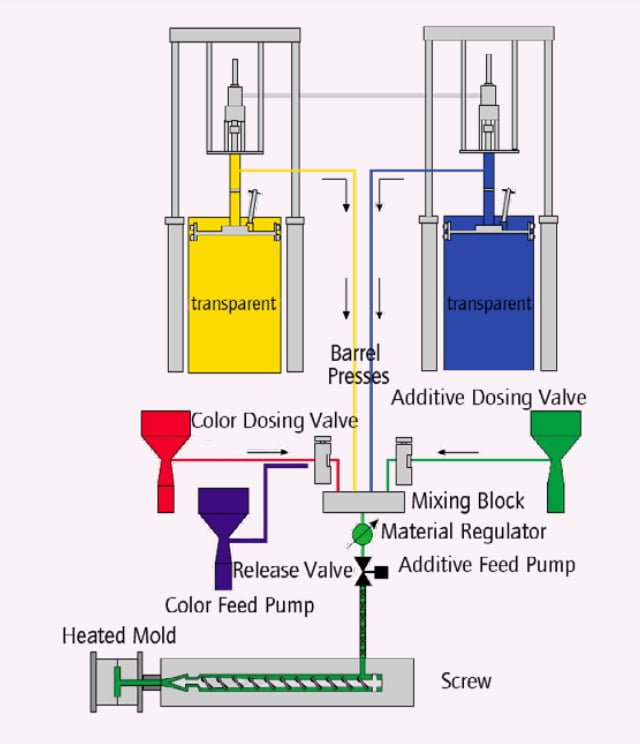
LSR 射出成形プロセスはどのように機能し、その利点は何ですか?
LSR 射出成形は、HCR 射出成形と同様に、キャビティ内に成形された最終製品を作成するために使用されます。LSR プロセスでは、非加熱の液体または粘性材料が射出ノズルから金型キャビティに注入されます。原材料は圧力をかけられた状態で密閉された加熱キャビティに送られ、瞬時にキャビティが満たされます。LSR 射出成形は、そのシンプルさから、非常に高速な製造方法であり、計量装置を使用してバレルから直接引き出すため、ターンアラウンド時間が短く、非常に大量の部品を製造するのに最適です。
LSR注入の主な利点
- 短くて正確な成形サイクル
- 大量生産
- 効率的かつ経済的な処理
- 幅広い用途、様々な一般製品を作ることができます
- 硬化が速く、型離れが良い
高濃度ゴム(HCR)射出成形
高粘度ゴム (HCR) は、熱硬化ゴムまたは HTV (高温加硫) シリコーンゴムとも呼ばれます。この材料は、非常に高分子量高分子を含む反応性シリコーンで作られています。
さまざまな原材料が HCR に特定の機能を提供できます。たとえば、機械的特性を向上させる高比表面積のヒュームドシリカや沈降シリカ、熱安定剤、可塑剤、再結合防止剤などです。
HCR エラストマーは従来の有機エラストマーよりも優れており、-50°C ~ +300°C の温度範囲で優れた機械的強度を発揮します。また、優れた耐老化性、化学的不活性、光や酸素にさらされても安定、着色しやすく透明にすることもできるため、食品包装や医療補助用途に最適です。
さまざまな添加剤を HCR に組み込むことで、航空宇宙、自動車、ヘルスケア、石油・ガス、建設、電子機器、電気自動車など、さまざまな業界の既存および新規のアプリケーションに無限のカスタム ソリューションを提供できるようになります。
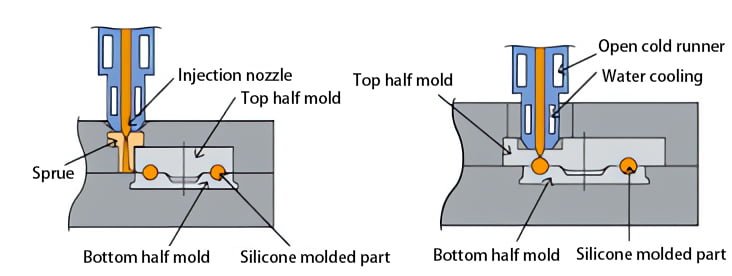
HCR 射出成形プロセスはどのように機能し、どのような利点が得られるのでしょうか?
計量された HCR は、スクリュー機構とノズル、ゲートを介してシリンダーから閉じられた加熱された金型に直接注入されます。材料が金型のキャビティに充填され、部品が形成されます。
HCR射出成形の主な利点
- 短くて正確な成形サイクル
- 単位コストの低減
- 材料の無駄を減らす
- プラスチックや金属などの他の材料との成形が可能
- 完成品に関しては、生産は安定している
- 圧縮成形やトランスファー成形に比べて、複雑な部品の精度と充填に優れています。
- これは、製品のサイズ、複雑さ、用途が大きく異なる場合に、最も一般的で強力な成形方法であると言えます。
圧縮成形と射出成形の違い
圧縮成形と射出成形は、どちらも事前に形成されたキャビティを充填するという点で似ていますが、圧縮金型では充填剤が直接事前に充填されるのに対し、射出成形では充填剤が閉じたキャビティ内に事前に完全に注入されるという点で異なります。
メーカー 異なるタイプの部品を製造する場合、圧縮成形と射出成形の両方を使用することがよくありますが、使用する部品のタイプは異なります。一般的に、射出成形はより複雑な(多くの場合はより小型の)部品を製造する場合に好まれますが、圧縮成形は、単純または基本的な設計や、押し出し成形では製造できない大型部品に非常に適しています。
その他の比較ポイントとしては、射出成形はサイクルタイムが短いため、大量生産品の場合は一般的に高速でコスト効率が高いのに対し、圧縮成形は主に少量から中量の生産シリーズの部品に使用されます。
押し出し成形
押し出しシリコーン製品は通常、押し出し機によって形成されます。シリコーンゴムの押し出しは、通常、ホース、ロープ、複雑なプロファイル、断面部品(多くの場合、非常に長く、多層コンポーネント)、ロッド、オーブンシール、ケーブル、電線絶縁体、ガスケット、シールの製造に使用されます。
シリコンチューブは医療機器や機械設備に広く使用されており、包装材の緩衝材としても使用できます。
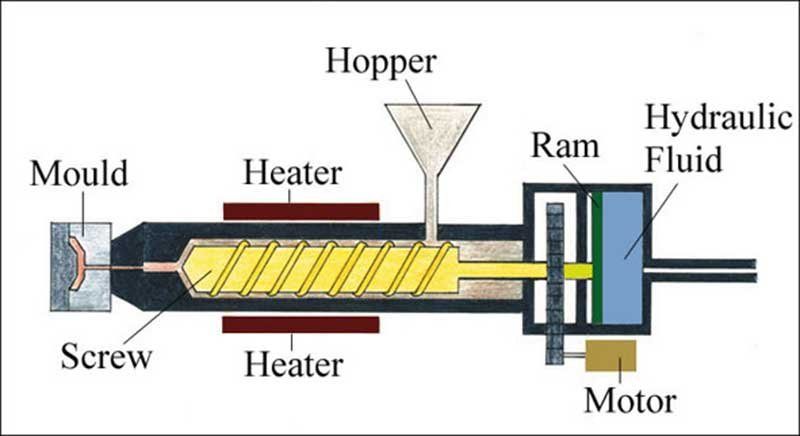
このプロセスでは、あらかじめストリップまたはブロックに加工された触媒を含む HCR 化合物を使用します。次に、プレフォームをスクリュー押し出し機に送り込み、カットパターンのある硬化鋼ダイに化合物を押し込みます。成形されたシリコンは、コンベア ベルト上の加熱チャンバーを通過し、連続プル オーブンで硬化されます。
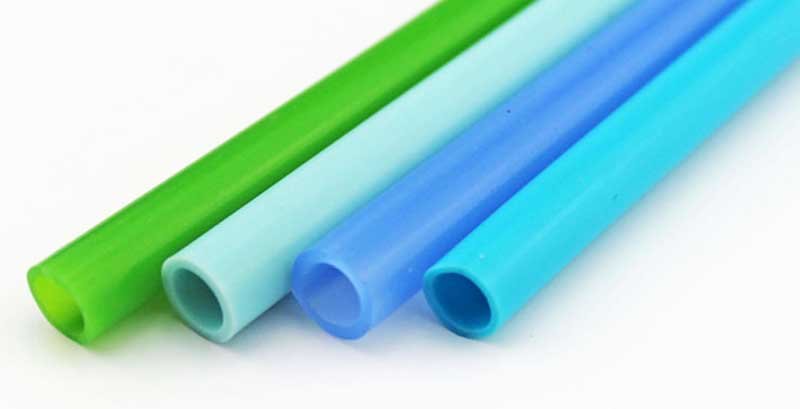
この技術を使用するメーカーにとっての主な課題は、特定の機械的、温度、速度制御プロセスで最適に機能し、最終製品を仕様、許容基準、規制基準に準拠させるために、適切なグレードのシリコーンゴムと適合触媒システムを選択することです。
シリコーンゴムカレンダー加工
カレンダー加工は、シートを一対の加熱ローラーに通して連続的に材料を圧縮し、滑らかにする機械加工です。これらの二重または多層の硬質鋼製ロールのセットはカレンダーと呼ばれます。カレンダーは圧力調整され、所定の均一な厚さ、表面仕上げ、光沢、マット、滑らか、接着、エンボス加工などのシリコンゴムの質感を生み出します。
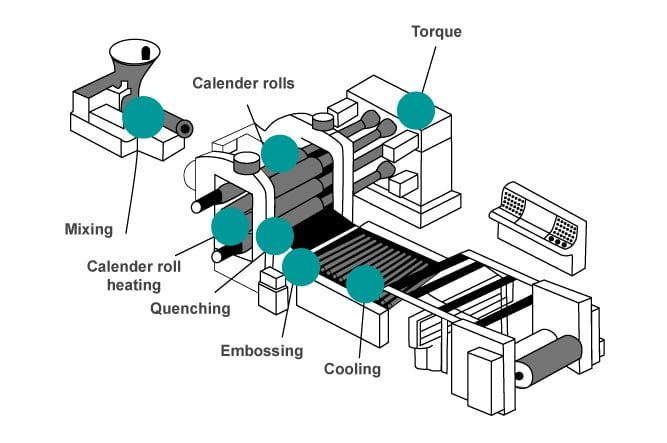
最終製品の機械的特性を決定する原材料 (通常は HCR) は、あらかじめ加熱軟化または押し出し加工され、配列された円筒形ロールに押し込まれます。カレンダー加工プロセスでは、未硬化のシリコン プリフォームを圧縮して連続したシリコン シートにします。その後、シリコンはリリース ライナーなどのさまざまな基材に押し付けたり、さまざまな布地、ガラス、プラスチックなどに接着したりできます。
カレンダー加工の主な利点は次のとおりです。
- 高品質製品の大量連続処理
- 保護ライニングで提供される自立型シート(サポートなし)、または有機または人工繊維(ポリアミド、ビスコース、ポリエステルなど)、ガラス、プラスチックなどの他の材料と組み合わせた製品。
- 用途は、建設用ライナー、家庭用品、アパレル、装飾品、食品接触製品、工業用コンベヤーベルト、医療用途のオートクレーブ可能製品など、ほぼ無限にあります。
シリコーンゴムトランスファー成形
トランスファー成形は、いくつかの点で圧縮成形に似ています。トランスファー成形では、補助チャンバー(トランスファータンクと呼ばれる)から密閉された加圧金型システムに押し込まれる HCR を使用します。この金型システムには、金型の上に加熱された容器が組み込まれており、ピストンで駆動されます。シリコーンゴムには、加熱前に比較的硬い材料を金型に移動できる独自のゲートおよびランナーシステムが充填されています。シリコーンゴムのトランスファー成形プロセスは、高精度のシリコーン成形部品の製造や、他の材料と「積み重ねて」複雑な形状の成形を可能にするのに最適です。HCR とトランスファー成形プロセスを組み合わせると、高品質の部品を製造でき、設計の柔軟性と生産サイクルの短縮が実現します。
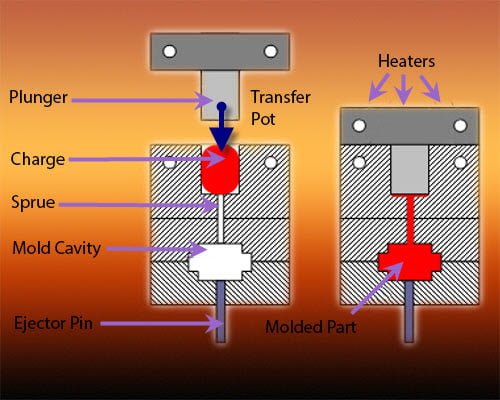
トランスファー成形は、金型が 2 つの部分に分割されるのではなく、完全に閉じられるという点で圧縮成形とは異なります。このため、金型を充填するためにより高い圧力が必要となるという点でも射出成形とは異なります。これにより、トランスファー成形では、外層に繊維やマトリックスを追加して、カスタム強化部品を製造することもできます。
トランスファー成形加工の主な利点
- ツールコストの削減
- 一体成形と高い寸法公差により、圧縮成形に比べて均一で正確で一貫性のある部品が得られます。
- ガラス、カーボン、アラミド、天然植物繊維など、金型内に事前に配置されたさまざまな強化繊維を受け入れるための効率的で機敏な能力。