シリコンの着色は、非反応性のため難しい課題となる可能性があり、一貫した鮮やかな色合いを実現するのは困難です。この困難は、色のにじみ、退色、または不均一な分布などの問題につながる可能性があり、生産コストが増加するだけでなく、製品の品質が低下し、ブランドの評判が損なわれるリスクもあります。
正しい方法を理解していれば、シリコンの着色は可能であり、効果的です。互換性のある着色剤を使用し、適切に混合し、正しい技術を採用することで、材料の特性を損なうことなく、希望する色合いを実現できます。
このガイドでは、シリコンを効率的かつ効果的に着色するために必要なすべてのことを説明します。
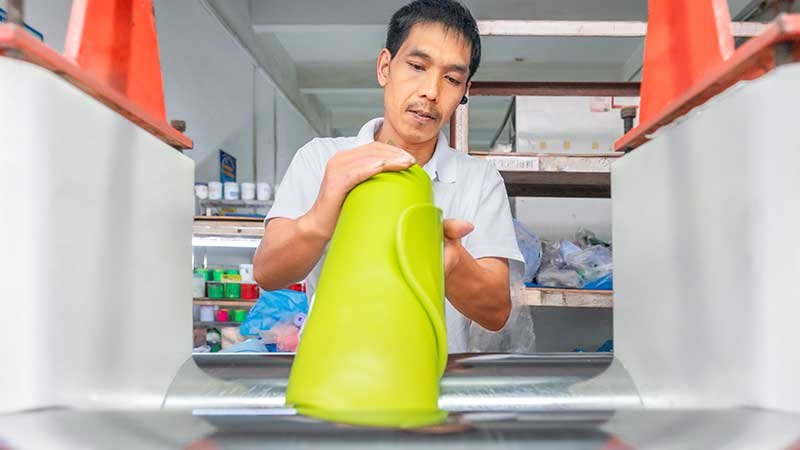
シリコンを着色する最良の方法は何ですか?
シリコンの着色にはいくつかの選択肢がありますが、すべての方法が同じように機能するわけではありません。最適な方法は、使用するシリコンの種類や希望する結果など、特定のニーズによって異なります。
顔料マスターバッチ
最も一般的な方法の 1 つは、顔料マスターバッチを使用することです。これは、成形プロセスの前に着色剤をシリコーンと事前に混合することを意味します。製品全体で一貫した色を実現するには理想的です。この方法は、その精度と安全性から、医療用および食品グレードのシリコーン業界で広く使用されています。
液状シリコーンゴム(LSR)着色
のために 液状シリコーンゴム(LSR) の場合は、LSR 専用に設計された液体着色剤を使用できます。この方法では、色の濃さを正確に制御できるため、独自の色が必要なカスタム オーダーに特に便利です。着色剤は、硬化プロセスの前に液体シリコーンに直接混合されます。
表面コーティング
もう一つの方法は、成型後にシリコンの表面に色を塗る表面コーティングです。この技術は表面の美観が重要な製品に適していますが、他の方法ほど耐久性がない場合があります。ただし、コーティング技術の進歩により耐久性が向上し、一部の用途では実行可能なオプションとなっています。
粉末顔料
粉末顔料 は、特に手作業で色を混ぜたい人向けのもう 1 つのオプションです。これらは通常、シリコーン オイルまたは溶剤と混ぜてペースト状にしてからシリコーンに加えます。この方法では色のブレンドに柔軟性がありますが、不一致を避けるために正確な混合が必要です。
シリコンに最適な着色剤はどれですか?
適切な着色剤を選択することは、シリコン着色を成功させる上で非常に重要です。間違った選択をすると、色の付着が悪くなったり、色あせたり、さらにはシリコン構造が損なわれる可能性があります。
有機顔料と無機顔料
有機顔料と無機顔料のどちらかを選択する必要があります。有機顔料はより明るく鮮やかな色を提供しますが、紫外線や高温下では安定性が低下する可能性があります。対照的に、無機顔料はより安定していますが、色はそれほど鮮やかではありません。製品の用途に応じて、どちらかを優先する場合があります。
シリコン対応着色剤
シリコンと互換性のある着色剤を使用することは不可欠です。これらはシリコンと結合するように特別に配合されており、色の均一な分布と長持ちする鮮やかさを保証します。他の素材用に設計された標準的な染料や顔料はうまく混ざらない可能性があり、時間の経過とともに分離したりにじんだりする可能性があります。
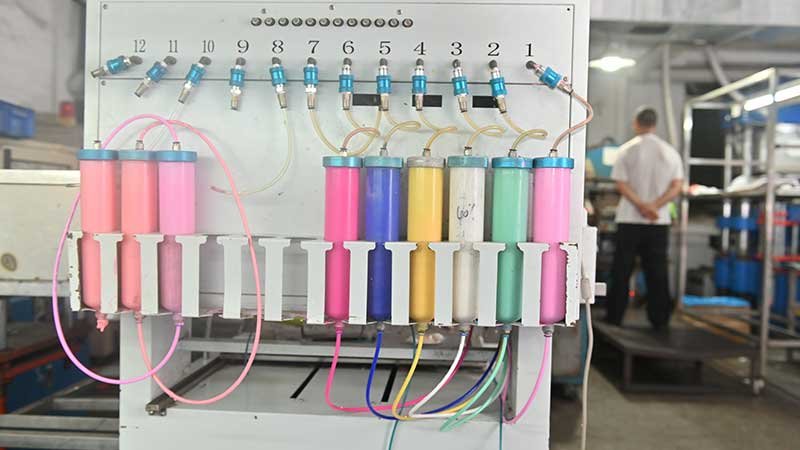
着色剤とシリコンを混ぜる方法は?
混合プロセスは、希望する色の一貫性を実現するために重要です。不適切な混合は、色の分布が不均一になったり、縞や斑点が生じる可能性があります。
手動ミキシング
少量の場合は、手作業で混ぜる方法もあります。着色剤をシリコンベースとよく混ぜてください。これは、スパチュラまたはミキサーを使用して行うことができます。重要なのは、最終製品の外観に影響を与える可能性のある気泡が発生しないように、ゆっくりと混ぜることです。
機械ミキシング
大量生産の場合は、機械による混合が推奨されます。これにより、より均一な混合が保証され、より大量のシリコンを処理できます。着色剤をシリコンに混合するように設計された専用の機械があり、時間の節約とエラーの削減に役立ちます。
硬化プロセス
混合後、シリコンを適切に硬化させることが重要です。一部の色素は熱によって変化する可能性があるため、硬化プロセスは最終的な色に影響を与える可能性があります。色の完全性を維持するために、硬化時間と温度に関する製造元のガイドラインに必ず従ってください。
シリコンの着色における一般的な課題は何ですか?
シリコンの着色は簡単ですが、知っておくべき課題がいくつかあります。
色あせ
よくある問題は 色あせ 時間が経つにつれて、この問題は発生します。これは特に、紫外線や高温にさらされる製品でよく発生します。紫外線に安定な顔料を使用し、シリコンを適切に硬化させることで、この問題を軽減できます。
色の不一致
色の一貫性がない 不適切な混合や互換性のない着色剤の使用により発生する可能性があります。これを避けるには、推奨される混合比率に従い、シリコンと互換性のある着色剤のみを使用するようにしてください。
表面の欠陥
着色方法として表面コーティングを選択した場合、剥がれやひび割れなどの表面欠陥が発生する可能性があります。これは、不適切な塗布や低品質のコーティングの使用が原因である可能性があります。コーティングを塗布する前に、シリコン表面が清潔で下塗りされていることを確認し、より密着性を高めてください。
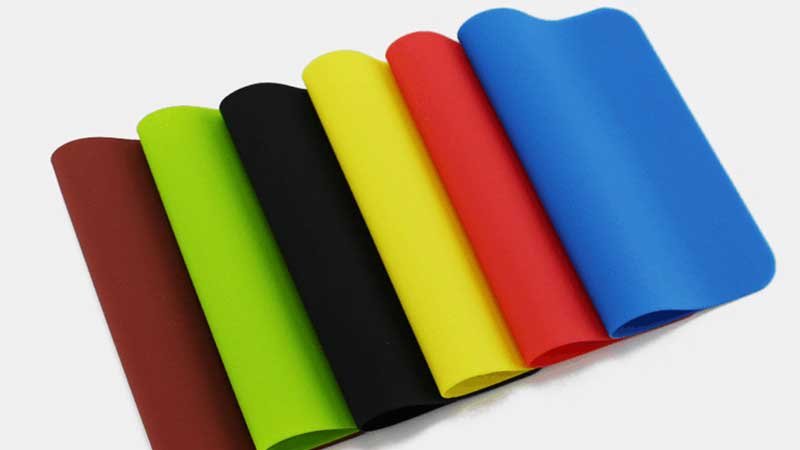
シリコン製品の色をカスタマイズできますか?
はい、シリコン製品の色をカスタマイズすることは可能ですが、慎重な計画と実行が必要です。
カラーマッチング
特定の色を合わせる必要がある場合は、着色剤サプライヤーと協力してカスタム ブレンドを作成できます。色合わせは、さまざまな顔料を混合して希望する色相を正確に実現する精密なプロセスです。これは、ブランディング目的や他のコンポーネントを合わせる必要がある場合に特に重要です。
多色製品
多色製品の場合、複数の着色剤を使用したり、異なる着色方法を組み合わせたりする必要があるかもしれません。これはより複雑になる可能性がありますが、クリエイティブなデザインとユニークな製品提供が可能になります。
テストと品質管理
大量生産の前に、着色シリコンをテストして、基準を満たしていることを確認することが重要です。これには、色の堅牢性、耐久性、一貫性のテストが含まれます。厳格な品質管理プロセスを導入することで、問題を早期に特定して解決することができます。
結論
シリコンの着色は難しいように思えるかもしれませんが、適切な方法、着色剤、技術を使用すれば、鮮やかで耐久性があり、一貫性のある結果を得ることができます。顔料マスターバッチ、液体着色剤、表面コーティングのどれを選択する場合でも、重要なのは、特定のニーズを理解し、混合と硬化のベスト プラクティスに従うことです。これにより、製品の魅力が高まるだけでなく、顧客の期待と業界標準にも確実に応えることができます。