シリコーン押出成形は、現代産業において最も信頼性が高く、広く利用されているプロセスの一つです。命を救う医療用チューブから、車のドアのガタつきを防ぐ防水シールまで、このプロセスは私たちの日常生活をよりスムーズにするために、舞台裏で静かに働いています。では、柔らかくて生地のような素材が、どのようにして完璧な形状の高性能製品へと変化するのでしょうか?シリコーン押出成形の魅力的な世界に飛び込み、一つ一つ解説していきましょう。
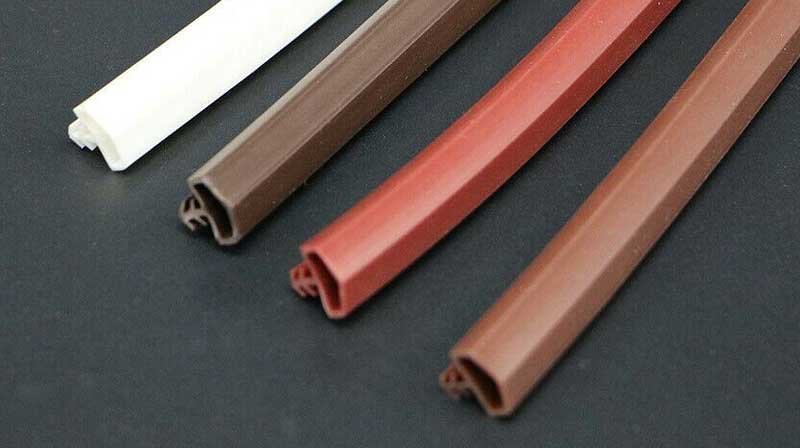
シリコーン押出成形とは?
シリコーン押出プロセスは、シリコーンの製造技術です。まず、材料を加熱し、金型に押し込んで所望の形状を作ります。押出後、材料は硬化処理され、耐久性と耐熱性が向上します。最後に、製品は冷却・切断され、次の使用に向けて準備されます。この効率的なプロセスは、様々な産業向けに、精密で高品質なシリコーン製品の製造に広く利用されています。
シリコーン押出成形のプロセス
シリコーン押出成形プロセスは、幅広いシリコーン製品の製造に用いられる確立された方法です。このプロセスは、原料シリコーンを様々な産業に適した高品質の押出成形品へと変換する複数の段階から構成されています。以下では、プロセスの各ステップについて詳しく説明します。
材料の準備
シリコーン押出プロセスは、材料の準備から始まります。高強度ゴム(HCR)は、その強度と汎用性から一般的に使用されています。さらに、最終製品の要件に応じて添加剤も選択されます。添加剤は以下の通りです。
- 硬化剤これらには、押し出しプロセス中の硬化に使用される過酸化物または白金ベースの触媒が含まれます。
- フィラーシリコーンの特性を調整するために、シリカなどの充填剤やその他の化合物が添加されます。これにより、引張強度の向上、収縮の低減、硬度の調整などが可能になります。
- 顔料: 特定の製品要件を満たすために顔料が組み込まれています。
- その他の添加剤可塑剤は柔軟性を高め、安定剤は老化や環境要因に対する耐性を向上させます。
混合
材料の準備ができたら、混合の準備が整います。混合とは、シリコーンと添加剤を混合し、均一なコンパウンドを作り、押出成形の準備を整えるプロセスです。これは通常、2本ロールミルや密閉式ミキサーなどの専用機器を用いて行われます。
- 2ロールミル2ロールミルは、材料をより均一に混合するために使用されます。ロールは材料を通過させ、連続的に混合とせん断を行います。
- 内部ミキサー: 2本ロールミルまたはバンバリーミキサーを用いてシリコーンベースと添加剤を混合します。材料は適切な粘度になるまで混練されます。
- 添加剤の分散適切な分散が不可欠です。添加剤はシリコーン全体に均一に分散されるように徹底的に混合され、強度、弾力性、熱安定性といった望ましい特性が得られます。
- 粘度調整: このプロセスでは粘度を慎重に調整し、シリコンが厚すぎたり薄すぎたりすることなく、押し出し機を通してスムーズに流れるようにします。
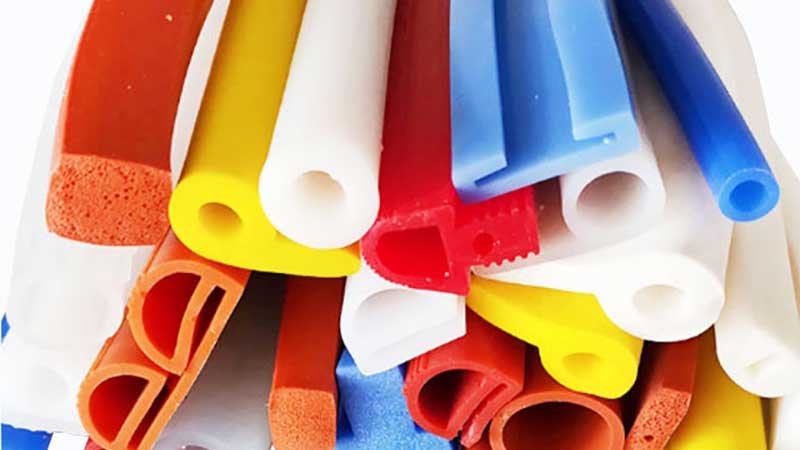
押し出し
押出成形は、準備されたシリコーン材料を押出機に投入することから始まります。材料は加熱・加圧され、ダイを通して押し出され、所望の形状に成形されます。
押出プロセス:
押出機は加熱されたバレルと回転するスクリューで構成されています。スクリューは材料を徐々に加熱しながら押し出します。押出機の温度は、シリコーン材料の適切な粘稠度と流動性を維持するために厳密に制御されます。
次に、材料を金型に押し込み、製品を成形します。気泡、厚みの不均一、表面の凹凸などの欠陥を避けるため、材料は金型内を滑らかかつ均一に流れなければなりません。
硬化
シリコンは押し出された後、加硫処理を受けます。この硬化処理によって、ゴムは柔らかく柔軟な状態から、固体で耐久性のある材料に変化します。
硬化プロセス:
押し出されたシリコーンは加熱された硬化炉を通過し、通常160℃~200℃の高温にさらされます。その後、硬化剤がシリコーンポリマーと反応し、鎖間に架橋結合を形成します。これにより、材料は強度が増し、耐熱性と耐摩耗性が向上します。硬化時間は、押し出された材料の厚さによって異なります。
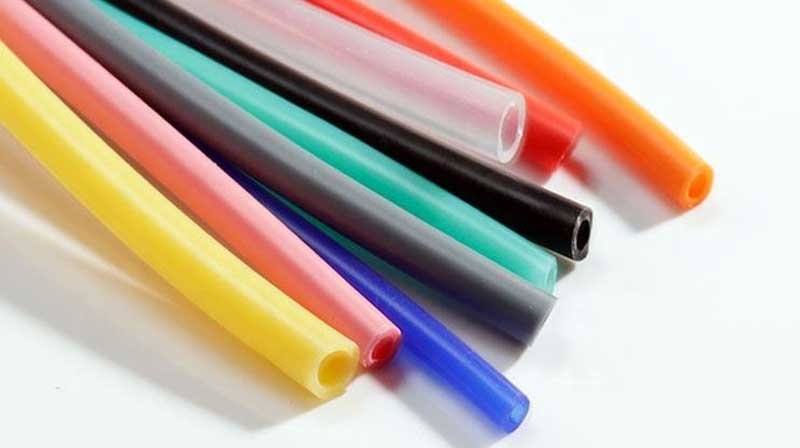
後処理
製品が希望の仕様を満たしていることを確認するには、いくつかの後処理手順を実行する必要があります。
- 冷却: 硬化後、材料の構造を安定させるために冷却する必要があります。これは通常、空冷または湯煎を用いて行われます。急速冷却は製品の固化を促進し、変形を防ぐのに役立ちます。
- 切断: 連続押し出し材料は、多くの場合、顧客の要件に応じて特定の長さまたはセクションに切断されます。
- スプールシリコンチューブなどの製品の場合、取り扱いや輸送を容易にするために材料がスプールに巻かれます。
一部のシリコン製品では、接着、印刷、組み立てなどの追加プロセスが必要になる場合があります。
- ボンディング: シリコン部品を他の材料と結合して多機能製品を作成することもできます。
- 印刷製品の表面にはロゴ、部品番号、その他のマークが印刷されている場合があります。
- 組み立て: 一部のシリコン製品は、シリコンガスケットやシールなどの大きなユニットに組み立てる必要がある場合があります。
最終製品が必要な仕様をすべて満たしていることを確認するには、品質管理が重要です。
- 押し出されたシリコンの各バッチは、引張強度、伸び、硬度などのさまざまなテストを受けます。
- 気泡や表面の凹凸などの欠陥を検出するために目視検査が行われます。
- 製品が必要なサイズと許容範囲を満たしていることを確認するために、寸法はキャリパーまたはレーザー システムで測定されます。
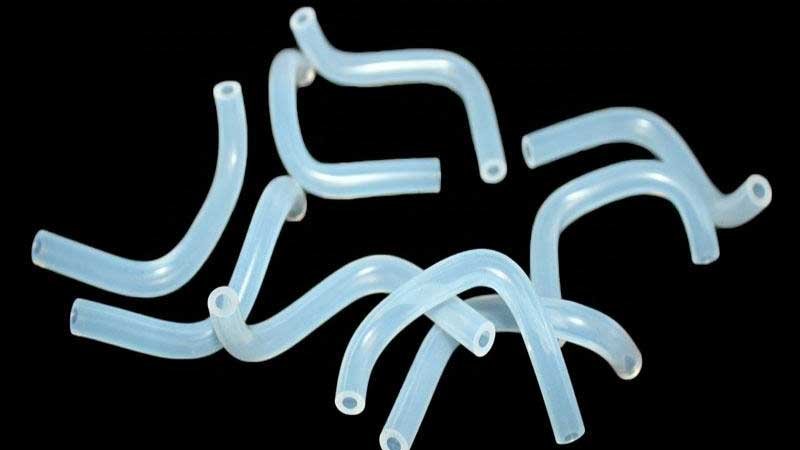
シリコーン押出成形の利点
高精度と一貫性
押し出し成形されたシリコーン製品は、一貫した品質と正確な寸法で知られています。このプロセスにより、各バッチで均一な厚さ、形状、材料分布が維持されます。複雑な断面形状も容易に実現できます。
設計とアプリケーションの多様性
シンプルなチューブから複雑なシーリングプロファイルまで、幅広い形状、サイズ、デザインを製造可能です。シリコーン押出成形品は、医療、自動車、電子機器、産業用途で広く使用されています。カラーバリエーションや素材の変更など、カスタマイズオプションも豊富にご用意しております。
大量処理でも効率的かつコスト効率に優れています
押出機のセットアップが完了すると、プロセスは連続的に稼働するため、大量生産に最適です。さらに、押出工程でシリコーンが効率的に使用されるため、材料の無駄が最小限に抑えられます。さらに、自動化により人件費が削減され、製造速度が向上します。
シリコーン押出成形の限界
シリコン押出成形には多くの利点がありますが、すべてのプロジェクトに最適というわけではありません。この方法を選択する前に考慮すべき点をご紹介します。
初期設定には時間がかかり、費用もかかる
カスタムダイの設計とテストには、特に特殊な形状の場合、時間がかかります。特に小ロット注文の場合、金型製作にはコストがかかることがあります。多くの場合、押し出しパラメータを微調整し、所望の出力を得るには、複数回の調整が必要になります。
連続プロファイルにのみ適しています
押し出しは、チューブ、コード、ストリップなどの直線的で連続した形状の製造に最適です。押し出しだけでは複雑な3Dパーツを作成することはできません。より複雑なデザインを製造するには、通常、押し出し後に追加の成形や組み立てが必要になります。
多くの場合、後処理が必要
押し出し成形されたシリコン部品は、最初の成形後に切断、接着、あるいは更なる硬化処理が必要となる場合があります。また、射出成形に比べて表面仕上げの選択肢も限られています。生産全体を通して一貫した公差を維持することは困難であり、厳格な品質管理が求められます。
押し出しは多くの用途で効率的ですが、これらの制限を理解することで、プロセスが製品の目標と一致することを保証できます。
シリコーン押出成形の用途
シリコーン押出成形は、様々な業界で広く利用されています。連続性、柔軟性、耐久性に優れた形状を製造できるため、多くの用途で好まれています。以下の表は、シリコーン押出成形が使用されている業界と、それぞれの用途に適した特性を示しています。
業界 | アプリケーション | 主な特徴 |
医学 | チューブ、カテーテル、シール、ガスケット、蠕動ポンプチューブ | 生体適合性、滅菌可能、柔軟性、無毒性 |
自動車 | シール、ガスケット、ホース、振動ダンパー | 耐熱性、耐候性、耐久性 |
エレクトロニクス | 絶縁材、電線コーティング、EMIシールド | 電気絶縁性、温度安定性 |
航空宇宙 | シーリングストリップ、断熱材、振動減衰材 | 軽量、耐高温、耐オゾン性 |
工事 | 窓シール、ウェザーストリップ、伸縮継ぎ目 | 紫外線耐性、防水性、長持ち |
食料と飲料 | 食品グレードのチューブ、シール、ガスケット | FDA承認済み、無毒、極度の温度にも耐性 |
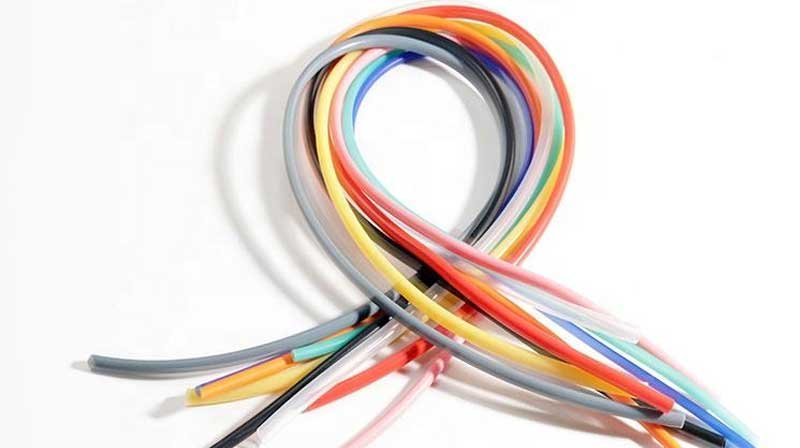
シリコーン押出成形の市場分析
シリコーン押出成形市場は近年、ヘルスケア、自動車、エレクトロニクス、建設などの業界における需要の増加に牽引され、着実に成長を遂げています。耐久性、柔軟性、そして過酷な条件への耐性を備えた高性能材料を求める産業界の増加に伴い、世界市場規模はさらに拡大すると予測されています。材料配合と製造技術の進歩に伴い、市場は製品のカスタマイズと効率性における革新を目の当たりにすると予想されます。
競争の面では、業界は強力な研究開発力、高度な生産技術、そして確立されたサプライチェーンによって大きな市場シェアを占める主要企業によって支配されています。大手企業は、競争力を維持するために、製品の品質、イノベーション、そして戦略的パートナーシップに重点を置いています。一方、新興企業は、専門的なソリューション、費用対効果の高い生産、そして持続可能な代替手段を提供することで、ニッチ市場にビジネスチャンスを見出しています。需要の継続的な増加に伴い、競争は激化し、さらなる技術開発と新たな応用分野への進出が促進されるでしょう。
結論
シリコーン押出成形は、最も派手なプロセスではないかもしれませんが、間違いなく最も効果的なプロセスの一つです。精度、効率、そして汎用性を兼ね備えています。耐熱自動車用ガスケット、医療用フレキシブルチューブ、食品に安全なキッチン用品など、押出成形されたシリコーンはあらゆる場所で使用され、その価値を静かに証明しています。技術の進歩に伴い、このプロセスはさらに洗練され、より革新的な用途への扉が開かれるでしょう。つまり、シリコーン押出成形は単なる製造技術ではなく、私たちの日常生活を向上させる耐久性と高性能を兼ね備えた製品への入り口なのです。