تعتبر عملية نقل السيليكون (STM) طريقة موثوقة وفعالة لإنتاج أجزاء السيليكون عالية الدقة.
تستكشف هذه المقالة عملية STM، بما في ذلك مبادئ عملها وخطواتها الرئيسية وتطبيقاتها. كما نناقش مزاياها وعيوبها، وكيفية مقارنتها بتقنيات القولبة الأخرى. علاوة على ذلك، نجيب على الأسئلة الشائعة لمساعدتك على فهم طريقة التصنيع هذه بشكل أفضل.
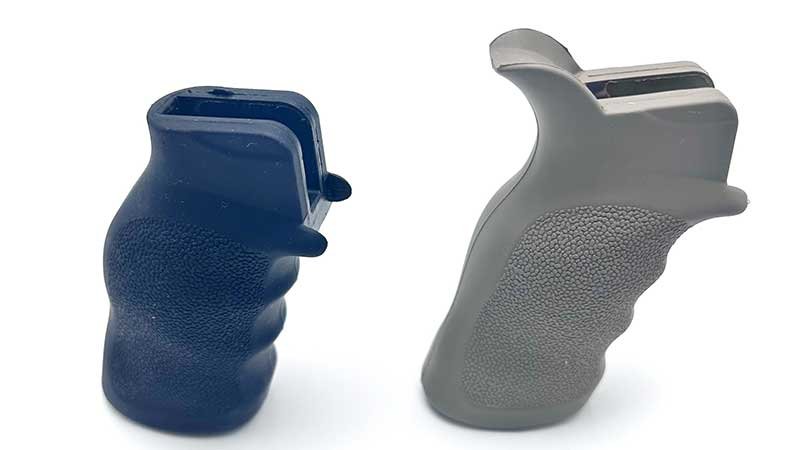
ما هو قالب نقل السيليكون؟
تعد عملية نقل السيليكون (STM) عملية تصنيع تستخدم لإنشاء أجزاء سيليكون عالية الدقة، مثل مقابض الأجهزة الطبية أو التغليفات للمكونات الإلكترونية. تُعدّ هذه الطريقة مناسبةً بشكل خاص للمنتجات التي تتطلب أشكالًا معقدة وتفاوتات دقيقة. تحقن عملية STM السيليكون غير المُعالَج في قالب مُسخّن تحت ضغط، ثم يُعالَج ليُشكّل المنتج النهائي. تُفضّل هذه الطريقة لمرونتها ومتانتها، مما يجعلها مثاليةً بشكل خاص للتطبيقات التي تتطلب توافقًا حيويًا، كما هو الحال في المجال الطبي.
كيف تعمل عملية نقل القالب السيليكوني؟
يُعدّ قولبة السيليكون بالنقل عملية تصنيع عالية الكفاءة والدقة. بفضل الجمع بين الحرارة والضغط، تضمن هذه الطريقة تدفقًا ممتازًا للمواد واستنساخًا دقيقًا للقالب. بدءًا من تحضير القالب وحتى المعالجة النهائية، تلعب كل خطوة دورًا حاسمًا في تحقيق أداء فائق للمنتج. فيما يلي المراحل الرئيسية لقولبة السيليكون بالنقل.
تحضير القالب: أساس الجودة
تحضير القالب هو الخطوة الأولى.
يُصنع القالب عادةً من الفولاذ عالي القوة أو الألومنيوم، ويُحدد شكل المنتج وجودته. غالبًا ما تُختار قوالب الفولاذ لمتانتها، بينما تُقلل قوالب الألومنيوم من دورات التصنيع. يجب تصنيع القالب بدقة عالية لضمان الحصول على منتج مثالي.
قبل بدء الإنتاج، يُنظَّف القالب ويُطلى بمادة عازلة، مثل بخاخات السيليكون أو طلاءات PTFE. يمنع هذا الطلاء الالتصاق، مما يُسهِّل إزالة المنتج، ويُطيل عمر القالب.
تحضير المواد: تجهيز السيليكون
يستخدم قولبة نقل السيليكون خليطًا من السيليكون الأساسي وعامل معالجة. يجب خلط هذه المكونات بنسب دقيقة لضمان تجانس الخصائص الكيميائية في المنتج النهائي. تتراوح نسب الخلط الشائعة بين 10:1 و20:1 (سيليكون أساسي وعامل معالجة)، وذلك حسب التركيبة والخصائص المطلوبة.
تتوفر مادة السيليكون بأشكال متنوعة، كالمسحوق والحبيبات والصفائح. ويُستخدم المطاط عالي الاتساق (HCR) بشكل شائع في قوالب النقل نظرًا لخصائصه الميكانيكية الأفضل مقارنةً بمطاط السيليكون السائل (LSR).
بعد الخلط، يتم وضع السيليكون المقاس مسبقًا في خزان آلة نقل القوالب (وعاء النقل)، والذي تم تصميمه عادةً بوظيفة التسخين المسبق لتحسين السيولة قبل النقل.
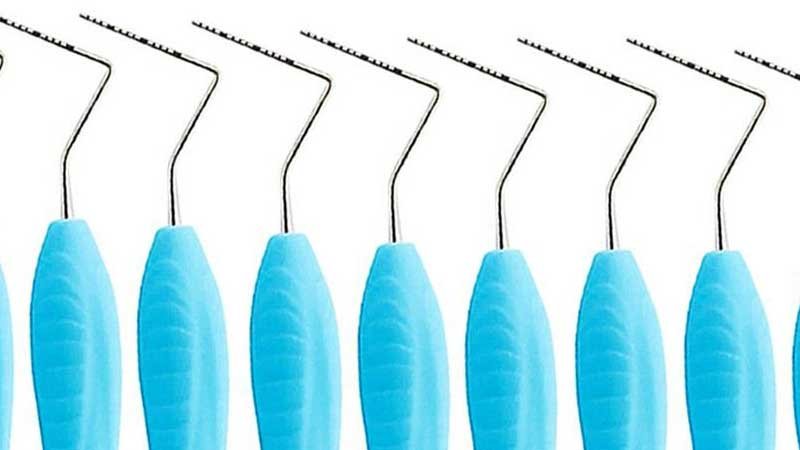
مرحلة النقل: تشكيل السيليكون
بعد تجهيز القالب وحشو السيليكون، يُغلق القالب. ثم يضغط مكبس الآلة على السيليكون المسخن في وعاء النقل. تتراوح ضغوط النقل النموذجية بين 500 و2000 رطل/بوصة مربعة، وذلك حسب لزوجة السيليكون وتعقيد تصميم القالب.
تُخفِّض الحرارة لزوجة السيليكون، مما يجعله يتدفق كالسائل. تحت الضغط، تتحرك المادة عبر نظام البوابة والمسار، وتملأ جميع تجاويف القالب. ولتحسين التدفق ومنع احتباس الهواء، غالبًا ما تُصمَّم قنوات تهوية في القالب للسماح بخروج الغازات المحبوسة.
يضمن هذا الجمع بين الحرارة والضغط تكرار حتى أدق تفاصيل القالب بدقة.
علاج:إعطاء الجزء قوته
بمجرد ملء القالب، فإن الخطوة التالية هي المعالجة، والمعروفة أيضًا باسم الفلكنة.
تُنشّط الحرارة الناتجة عن عملية النقل عامل المعالجة، مما يُحفّز تفاعلًا تشابكيًا بين جزيئات السيليكون. تتراوح درجات حرارة المعالجة عادةً بين 150 و200 درجة مئوية (302 و392 درجة فهرنهايت)، وتتراوح مدة المعالجة بين 30 ثانية وعدة دقائق، حسب سُمك القطعة.
تُحوّل هذه العملية الكيميائية السيليكونَ اللين إلى شكلٍ متينٍ ودائم، مما يُعطي القطعة المصبوبة قوةً ومرونةً ومتانةً. بالنسبة للقطع التي تتطلب قوةً ميكانيكيةً أعلى، قد يلزم تعقيمها لاحقًا في فرنٍ على درجة حرارة 200 درجة مئوية لعدة ساعات.
إزالة القالب والقذف: إطلاق المنتج النهائي
بعد المعالجة، يفتح القالب.
لإزالة قطعة السيليكون النهائية، تُوضع دبابيس القذف داخل القالب. يجب التحكم بدقة في موضع هذه الدبابيس وضغطها لمنع تشوه القطعة.
تدفع هذه المسامير القطعة المصبوبة برفق للخارج دون التسبب في أي ضرر. في بعض الحالات، يُستخدم نظام إزالة القالب بمساعدة الفراغ لتقليل الضغط على القطعة أثناء إزالتها.
إن التعامل الدقيق أثناء هذه الخطوة ضروري للحفاظ على سلامة الجزء.
مرحلة ما بعد المعالجة: اللمسة الأخيرة
قد تحتوي أجزاء السيليكون المصبوبة حديثًا على مواد زائدة على طول خط فصل القالب، تُعرف باسم "الفلاش". يجب قص هذه المادة أثناء المعالجة اللاحقة. يتراوح سمك اللمعان عادةً بين 0.05 مم و0.2 مم، حسب دقة القالب وقوة التثبيت أثناء التشكيل.
بالإضافة إلى ذلك، قد يلزم إجراء معالجات سطحية إضافية أو فحوصات جودة. تشمل طرق المعالجة اللاحقة الشائعة المعالجة بالبلازما لتعزيز التصاق السطح لتطبيقات الترابط، والإزالة بالتبريد العميق، حيث تُجمّد الأجزاء وتُقلب لإزالة المواد الزائدة.
وتضمن هذه الخطوات النهائية أن أجزاء السيليكون تلبي جميع المعايير الأبعادية والجمالية اللازمة.
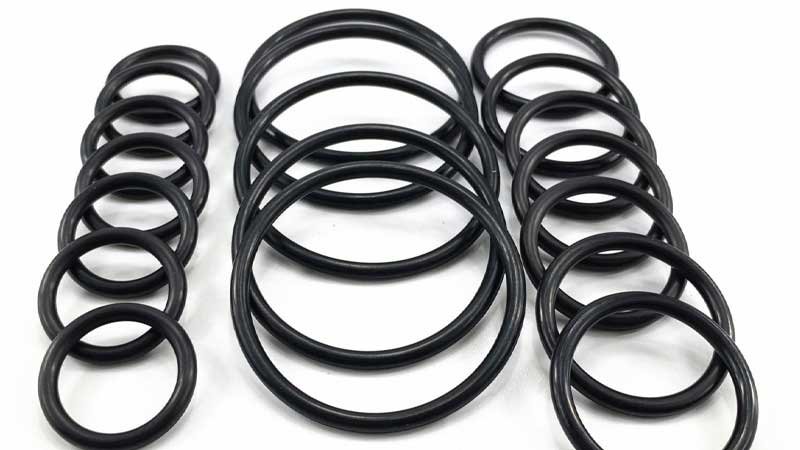
المزايا والقيود: موازنة الإيجابيات والسلبيات
يوفر قولبة نقل السيليكون مرونةً ونتائج عالية الجودة، مما يجعله مثاليًا للعديد من الصناعات. ومع ذلك، وكما هو الحال في أي عملية تصنيع، له مزايا وعيوب يجب مراعاتها.
مزايا قوالب نقل السيليكون
- المرونة والمتانةيُعدّ قولبة السيليكون بالنقل مثالية لإنتاج قطع ذات أشكال معقدة. تتيح عملية القولبة هذه إنتاج تصاميم معقدة وخصائص دقيقة يصعب تحقيقها بالطرق الأخرى.
- سهولة إدراج التكاملمن السهل دمج الحشوات أو المكونات المعدنية مباشرةً في أجزاء السيليكون أثناء عملية التشكيل. هذا يُقلل الحاجة إلى خطوات تجميع إضافية، مما يوفر الوقت وتكاليف العمالة.
- تصميم بسيط وتكاليف قابلة للتحكمالتصميم العام لقوالب نقل السيليكون بسيط نسبيًا، وعملية التصنيع فعالة من حيث التكلفة، خاصةً للإنتاج بكميات متوسطة إلى صغيرة. كما أنها توفر توازنًا جيدًا بين التكلفة والأداء لتطبيقات محددة.
حدود صب نقل السيليكون
- وقت معالجة أطولتتراوح مدة معالجة قوالب نقل السيليكون بين دقيقة وخمس عشرة دقيقة، وهي أطول من حقن القالب. هذا قد يُبطئ الإنتاج، خاصةً في الكميات الكبيرة.
- نفايات الموادقد تُسبب مراحل تحضير المواد ونقلها بعض الهدر، مما قد يؤثر على الكفاءة ويزيد من تكاليف المواد.
- حبس الهواءقد يُحبس الهواء أثناء عملية النقل، مما قد يؤدي إلى عيوب مثل الفقاعات في المنتج النهائي، مما يؤثر على جودته. لذا، يلزم توفير تهوية جيدة ومراقبة دقيقة للعملية لتجنب هذه المشكلة.
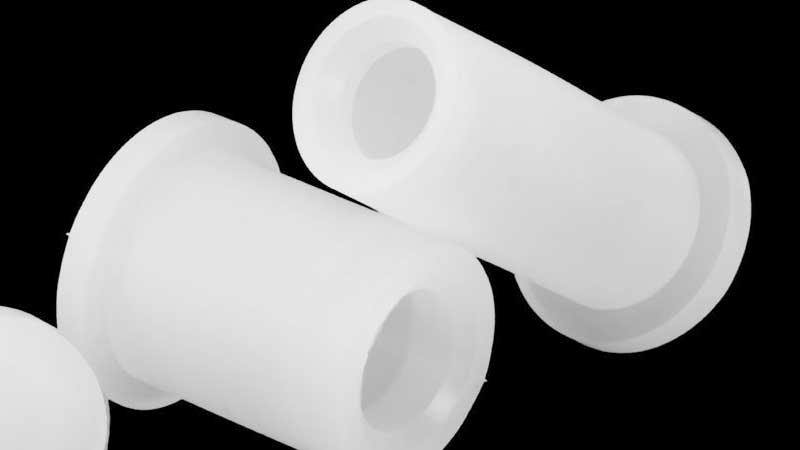
تطبيقات صب نقل السيليكون
يُستخدم قالب نقل السيليكون على نطاق واسع في مختلف الصناعات بفضل مرونته وقدرته على دمج الحشوات المعدنية. فيما يلي بعض التطبيقات الرئيسية:
صناعة | التطبيقات |
طبي | مقابض الأدوات الجراحية ومكونات الزرع، بسبب التوافق الحيوي ومقاومة درجات الحرارة. |
إلكترونيات | المكونات الإلكترونية لحماية الدوائر من العوامل البيئية. |
السيارات | الأختام الهيدروليكية وأختام الوجه، مناسبة للحواف الحادة والأشكال المعقدة. |
تتمتع شركة STM بقدرة على إنشاء أجزاء مفصلة وعالية الأداء مما يجعلها مثالية لهذه الصناعات، حيث توفر مكونات متينة وموثوقة.
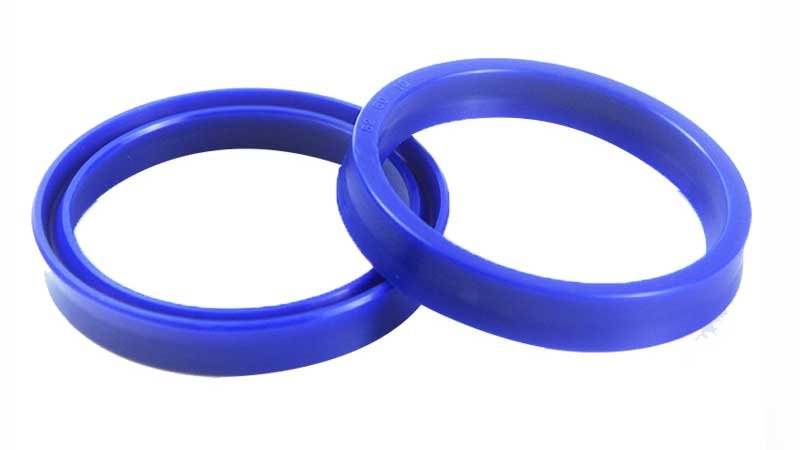
أسئلة مكررة
فيما يلي بعض الأسئلة الشائعة لمساعدة القراء على فهم عملية صب نقل السيليكون (STM) بشكل أفضل:
ما هي تكلفة STM؟
تعتمد تكلفة قوالب STM على حجم الدفعة وتعقيد القطعة. وهي عادةً أعلى من قوالب الضغط نظرًا لتكلفة المعدات والمواد.
كم من الوقت يستغرق STM؟
تستغرق كل دورة عادة حوالي 30-45 ثانية، مع أوقات معالجة تتراوح من 1 إلى 15 دقيقة، اعتمادًا على حجم الجزء.
هل STM مناسب للأجهزة الطبية؟
نعم، يتم استخدام STM على نطاق واسع في الصناعة الطبية بسبب توافقها الحيوي ومقاومتها للحرارة، مما يجعلها مثالية لإنتاج المقابض الجراحية والغرسات والمكونات الطبية الأخرى.
كيف يختلف STM عن القولبة بالحقن؟
تستخدم تقنية STM ضغطًا أقل (1500-2000 رطل/بوصة مربعة)، مما يجعلها أكثر ملاءمةً للإنتاج بكميات كبيرة من المتوسطة إلى الصغيرة والأشكال المعقدة. في المقابل، تستخدم تقنية القولبة بالحقن ضغطًا أعلى، وهي أكثر كفاءةً للإنتاج بكميات كبيرة.
خاتمة
صب السيليكون بالنقل تقنية متعددة الاستخدامات توفر الدقة والمتانة والمرونة. على الرغم من بعض القيود، مثل فترات المعالجة الطويلة واحتمالية هدر المواد، إلا أن قدرتها على إنشاء أشكال معقدة ودمج الحشوات تجعلها حلاً قيّماً للعديد من الصناعات. إن فهم عملية صب السيليكون بالنقل وفوائدها يساعد المصنّعين على اختيار أفضل طريقة صب تناسب احتياجاتهم.