Silikon enjeksiyon kalıplama, özellikle tıbbi cihazlar, otomotiv, tüketici elektroniği ve havacılık gibi sektörlerde yaygın olarak kullanılan bir silikon üretim yöntemidir.
Bu makalede silikon enjeksiyon kalıplama kavramı, süreci, avantajları, dezavantajları ve uygulamaları ele alınacaktır.
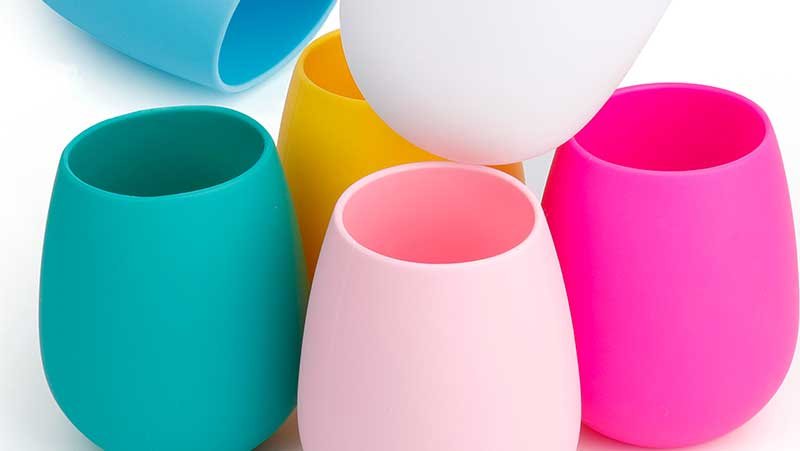
Silikon Enjeksiyon Kalıplama Nedir?
Silikon enjeksiyon kalıplama, bir silikon üretim sürecidir. Sıvı silikon kauçuğu yüksek basınç altında ısıtılmış bir kalıba enjekte eder ve ardından silikon kalıp içinde kürlenerek karmaşık tasarımlara ve hassas toleranslara sahip esnek, dayanıklı bileşenler oluşturur.
Bu yöntem tıbbi cihazlar, otomotiv, tüketici elektroniği ve havacılık gibi sektörlerdeki uygulamalar için idealdir.
Silikon Enjeksiyon Kalıplama İşlemi
Silikon enjeksiyon kalıplama, hassas bir silikon üretim sürecidir ve özellikle yüksek performanslı malzemeler gerektiren uygulamalar için uygundur. Üreticiler, sürecin her aşamasını hassas bir şekilde kontrol ederek, mükemmel tutarlılık, hassasiyet ve güvenilirliğe sahip yüksek kaliteli silikon bileşenler üretebilirler. Ana adımlar aşağıdaki gibidir.
Malzeme Hazırlığı
Sıvı silikon kauçuk enjeksiyon kalıplama sürecinde malzeme hazırlığı önemlidir.
İlk olarak, bileşen A ve bileşen B, karıştırmadan önce erken kürlenmeyi önlemek için ayrı ayrı saklanır. Bileşen A, silikon polimerden oluşur ve elastikiyet ve esneklik sağlar. Bileşen B tipik olarak platin bazlı bir katalizör olsa da, silikonun çapraz bağlanmasını ve kürlenmesini destekler.
Daha sonra, A ve B bileşenlerinin oranı ölçüm ekipmanı tarafından hassas bir şekilde kontrol edilir, genellikle 1:1 oranında.
Daha sonra ölçülen bileşenler statik bir karıştırıcı kullanılarak iyice karıştırılır. Karıştırma işlemi sırasında, erken kürlenmeyi veya malzemenin özelliklerinde herhangi bir değişikliği önlemek için sıcaklık kontrolü esastır.
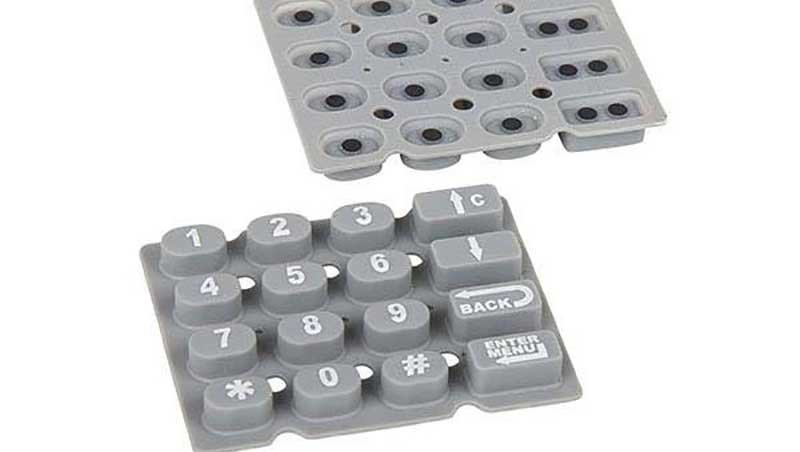
Enjeksiyon
LSR düzgün bir şekilde hazırlandıktan sonra enjeksiyon kalıplama makinesine sokulur. Makine bir namlu, bir piston veya vida, bir karıştırıcı ve bir nozuldan oluşur. Hazırlanan silikon karışımı namluya beslenir ve enjeksiyon için uygun viskoz bir sıvı hali elde etmek için genellikle 250°F ile 300°F (121°C ile 149°C) arasında önceden belirlenmiş bir sıcaklığa ısıtılır. Isıtılmış silikon daha sonra yüksek basınç altında ısıtılmış bir kalıp boşluğuna enjekte edilir. Kalıbın tasarımı, nihai ürünün geometrisini tanımlar ve ince ayrıntılara sahip karmaşık şekillerin oluşturulmasına olanak tanır.
Temel parametreler, nihai ürünün kalitesi üzerinde önemli bir etkiye sahiptir. Bu parametreleri optimize etmek, belirli ürün gereksinimleri ve ekipman performansının bir kombinasyonunu gerektirir. Aşağıda bir dizi temel üretim parametresi verilmiştir:
Parametre | Tipik Aralık | Faktörler |
Kalıp Sıcaklığı | 150-200°C | Kürlenme hızı, malzeme özellikleri |
Enjeksiyon Basıncı | 50-150 MPa | Kalıp dolumu, ürün yoğunluğu |
Enjeksiyon Hızı | 10-50 mm/s | Baloncuk oluşumu, üretim verimliliği |
- Kalıp sıcaklığı: Genellikle 150°C ile 200°C arasında değişir ve kürlenme hızının ve genel malzeme özelliklerinin belirlenmesinde önemli bir rol oynar.
- Enjeksiyon basıncı: Genellikle 50-150 MPa arasında olup kalıp dolumunu ve bitmiş ürünün yoğunluğunu etkiler.
- Enjeksiyon hızı: Genellikle 10 ila 50 mm/s arasında değişir ve kabarcık oluşumunu ve genel üretim verimliliğini etkiler.
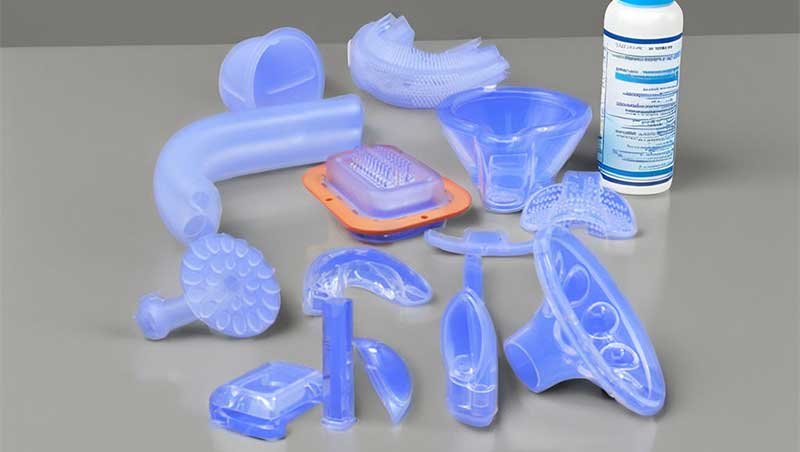
Kürleme (Vulkanizasyon)
Enjeksiyondan sonra kalıp, kürleme işlemini başlatmak için belirli bir sıcaklıkta tutulur; bu, aynı zamanda kürleme olarak da bilinir. vulkanizasyon. Bu, silikon polimer zincirlerini çapraz bağlayan ve sıvı malzemeyi katı, elastik bir yapıya dönüştüren bir kimyasal reaksiyonu içerir. Tam vulkanizasyonu sağlamak için kürleme sıcaklığı ve süresi dikkatlice kontrol edilir. Tipik olarak, kürleme sıcaklıkları 250°F ila 300°F (121°C ila 149°C) arasında değişir ve işlem süresi parçanın kalınlığına ve karmaşıklığına bağlı olarak birkaç dakikadan 30 dakikanın üzerine kadar değişebilir.
Rötuş
Kürleme tamamlandıktan sonra kalıp soğutulur ve katılaşmış silikon parçası dışarı atılır. Son işlem adımları şunları içerebilir:
- Kırpma ve Tüy Alma: Operatörler, istenilen şekli ve yüzey kalitesini elde etmek için ayırma çizgilerinden ve kapılardan çapak olarak bilinen fazla malzemeyi temizler.
- Ek Kürleme (Kürleme Sonrası): Kalıplanan parçalar, mekanik özelliklerini geliştirmek ve çapraz bağlanmanın tam olarak sağlanması için yüksek sıcaklıklarda ısıtılır.
- Yüzey İşlemleri: Yapışma, görünüm veya işlevselliği iyileştirmek için plazma işlemi, kaplama veya bağlama gibi çeşitli işlemler uygulanır.
- Kalite Kontrolü: Denetçiler, parçaların boyutlar, mekanik özellikler ve görsel kalite açısından belirtilen standartları karşıladığını doğrulamak için kapsamlı denetimler gerçekleştirir.
Bu son işlem adımları, ürünün amaçlanan uygulama için gerekli özellikleri ve performans kriterlerini karşılamasını sağlamak açısından önemlidir.
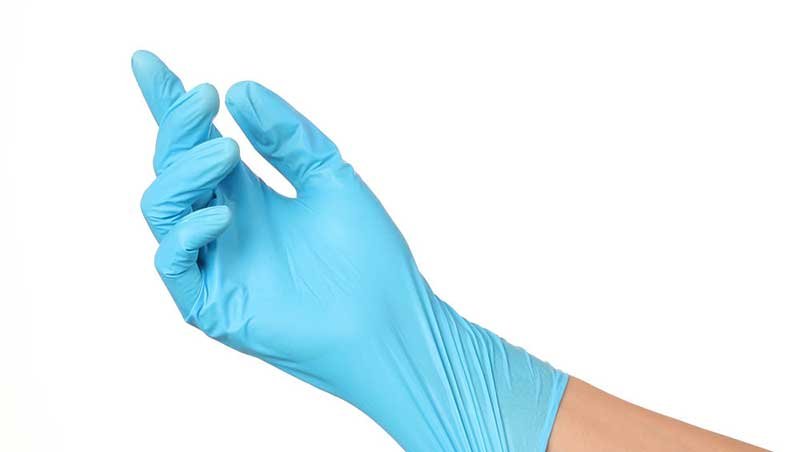
Silikon Enjeksiyon Kalıplamanın Avantajları
Silikon enjeksiyon kalıplama, yüksek kaliteli, hassas mühendislikle üretilmiş silikon ürünler üretmek için tercih edilen bir seçenek haline gelen birçok önemli avantaj sunmaktadır.
- Hassasiyet ve tekrarlanabilirlik: Bu işlem kullanılarak sıkı toleranslara sahip karmaşık şekiller üretilebilir. Bu, yüksek performans ve tutarlılığın gerekli olduğu tıbbi cihazlar, otomotiv ve elektronik gibi endüstriler için özellikle avantajlıdır.
- Minimum atık: Silikon enjeksiyon kalıplamada malzemenin hassas kullanımı minimum atık sağlar. Sonuç olarak, aşırı kesme ihtiyacı azalır ve bu da maliyetleri düşürmeye yardımcı olur.
- Kısa çevrim süreleri: Silikon enjeksiyon kalıplama, sıcaklık, basınç ve enjeksiyon hızı gibi faktörlerin kontrolü yoluyla kısa çevrim sürelerine olanak tanır. Bu, daha hızlı üretime, daha yüksek çıktıya ve daha kısa teslim sürelerine yol açar.
Genel olarak silikon enjeksiyon kalıplama, karmaşık özelliklere ve yüksek performans taleplerine sahip yüksek kaliteli silikon ürünlerin üretimi için uygun maliyetli, verimli ve çok yönlü bir çözüm sunmaktadır.
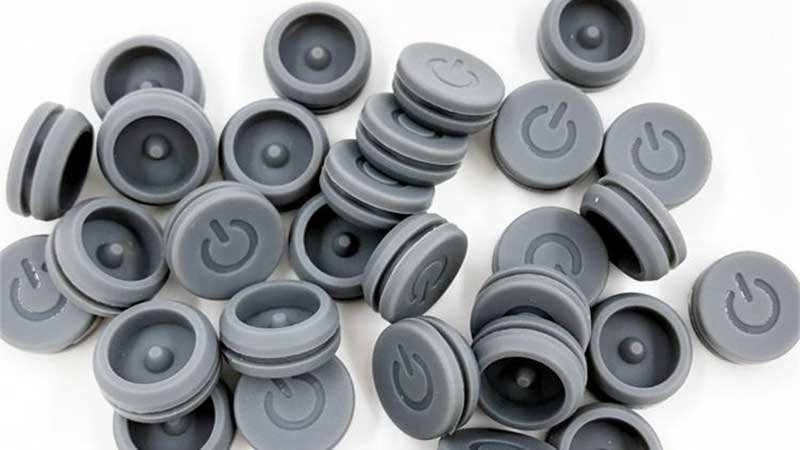
Silikon Enjeksiyon Kalıplamanın Dezavantajları
Silikon enjeksiyon kalıplama ayrıca dikkatlice ele alınması gereken belirli zorluklar sunar. Başlıca dezavantajları şunlardır:
- Yüksek İlk Takım Maliyetleri: Enjeksiyon kalıplama için kalıp pahalıdır, özellikle karmaşık tasarımlar için. Bu ön maliyetler, sınırlı bütçeli veya küçük üretim hacimli projeler için caydırıcı olabilir.
- Maddi Sınırlamalar: Enjeksiyon kalıplama işlemi öncelikle sıvı silikon kauçuk (LSR) kullanır. Tüm uygulamalar için gereken belirli malzeme özelliklerini sunmayabilir. Bu sınırlama, performans gereksinimlerine göre dikkatli malzeme seçimini gerektirir.
Silikon enjeksiyon kalıplama güçlü bir üretim tekniği olmakla birlikte, bu potansiyel dezavantajları anlamak ve ele almak, ürün geliştirmedeki uygulamasını optimize etmek için önemlidir.
Silikon Enjeksiyon Kalıplamanın Uygulamaları
Silikon enjeksiyon kalıplama, çeşitli endüstrilerde kullanılan çok yönlü bir üretim sürecidir. Aşağıdaki tablo, silikon enjeksiyon kalıplamanın en yaygın uygulamalarından bazılarını özetlemektedir:
Endüstri | Uygulamalar |
Tıbbi | Kateterler, cerrahi contalar, protezler, tıbbi eldivenler ve tüpler. |
Otomotiv | Contalar, contalar, hortumlar, motor yatakları ve elektrik yalıtım bileşenleri. |
Elektronik | Tuş takımları, konnektörler, contalar, contalar, yalıtkanlar ve anahtar pedleri. |
Havacılık | Contalar, contalar, yalıtım panelleri, yakıt hortumları ve O-ringler. |
Tüketim Malları | Mutfak eşyaları, bebek bakım ürünleri, kişisel bakım ürünleri ve giyilebilir ürünler. |
Bu uygulamalar, biyouyumluluk, esneklik, ısı direnci ve dayanıklılık gibi silikon malzemelerin benzersiz özelliklerinden dolayı silikon enjeksiyon kalıplamanın uyarlanabilirliğini vurgulamaktadır.
Çözüm
Silikon enjeksiyon kalıplama, çeşitli endüstrilerde benzersiz hassasiyet ve çok yönlülük sunan temel bir üretim süreci olarak öne çıkar. Karmaşık, yüksek kaliteli bileşenler üretme yeteneği, onu tıbbi cihazlar, otomotiv, tüketici elektroniği ve havacılık gibi sektörlerde vazgeçilmez kılar. Hem avantajlarını hem de sınırlamalarını anlayarak, üreticiler bu tekniğin tüm potansiyelinden yararlanabilir, inovasyonu teşvik edebilir ve üstün silikon ürünlerinin üretimini sağlayabilir.
Kaynaklar: