シリコーン射出成形は、特に医療機器、自動車、家電製品、航空宇宙などの業界で広く使用されているシリコーン製造方法です。
この記事では、シリコーン射出成形の概念、プロセス、利点、欠点、および用途について説明します。
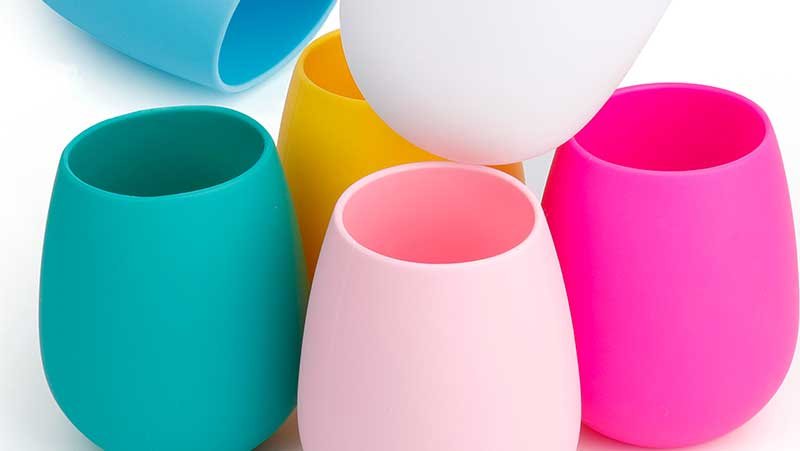
シリコーン射出成形とは何ですか?
シリコーン射出成形は、シリコーンの製造プロセスです。液状シリコーンゴムを加熱された金型に高圧下で注入し、金型内でシリコーンを硬化させることで、複雑なデザインと精密な公差を備えた、柔軟で耐久性のある部品を形成します。
この方法は、医療機器、自動車、民生用電子機器、航空宇宙などの業界でのアプリケーションに最適です。
シリコーン射出成形プロセス
シリコーン射出成形は精密なシリコーン製造プロセスであり、特に高性能材料を必要とする用途に適しています。プロセスの各段階を正確に制御することで、メーカーは優れた均一性、精度、信頼性を備えた高品質のシリコーン部品を製造できます。主な手順は次のとおりです。
材料の準備
液状シリコーンゴムの射出成形プロセスでは、材料の準備が重要です。
まず、A成分とB成分は混合前に早期硬化を防ぐため、別々に保管されます。A成分はシリコーンポリマーで構成され、弾力性と柔軟性を提供します。一方、B成分は典型的には白金系触媒であり、シリコーンの架橋と硬化を促進します。
次に、コンポーネント A と B の比率が計量装置によって正確に制御され、通常は 1:1 の比率になります。
次に、計量された成分をスタティックミキサーで徹底的に混合します。混合プロセス中は、早期硬化や材料特性の変化を防ぐため、温度管理が不可欠です。
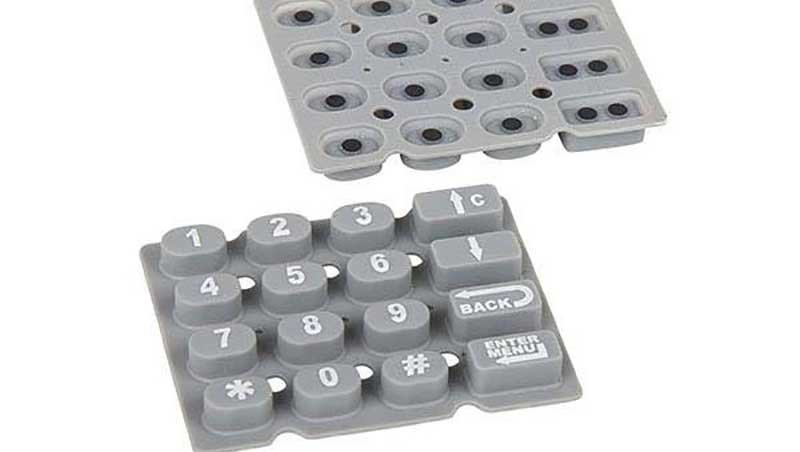
注射
LSRが適切に準備されると、射出成形機に投入されます。この成形機は、バレル、プランジャーまたはスクリュー、ミキサー、ノズルで構成されています。準備されたシリコーン混合物はバレルに投入され、所定の温度(通常は121℃~149℃)に加熱され、射出成形に適した粘性液体状態になります。加熱されたシリコーンは、高圧下で加熱された金型キャビティに注入されます。金型の設計によって最終製品の形状が決まり、微細なディテールを持つ複雑な形状の成形が可能になります。
主要なパラメータは最終製品の品質に大きな影響を与えます。これらのパラメータを最適化するには、特定の製品要件と設備の性能を組み合わせる必要があります。以下に主要な生産パラメータをいくつか示します。
パラメータ | 標準範囲 | 要因 |
金型温度 | 150~200℃ | 硬化速度、材料特性 |
射出圧力 | 50~150MPa | 金型充填、製品密度 |
射出速度 | 10~50 mm/秒 | バブル形成、生産効率 |
- 金型温度: 一般的には 150°C ~ 200°C の範囲で、硬化速度と全体的な材料特性を決定する上で重要な役割を果たします。
- 射出圧力: 一般的には 50 ~ 150 MPa の範囲で、金型の充填と完成品の密度に影響します。
- 射出速度: 通常は 10 ~ 50 mm/s の範囲で、気泡の形成と全体的な生産効率に影響します。
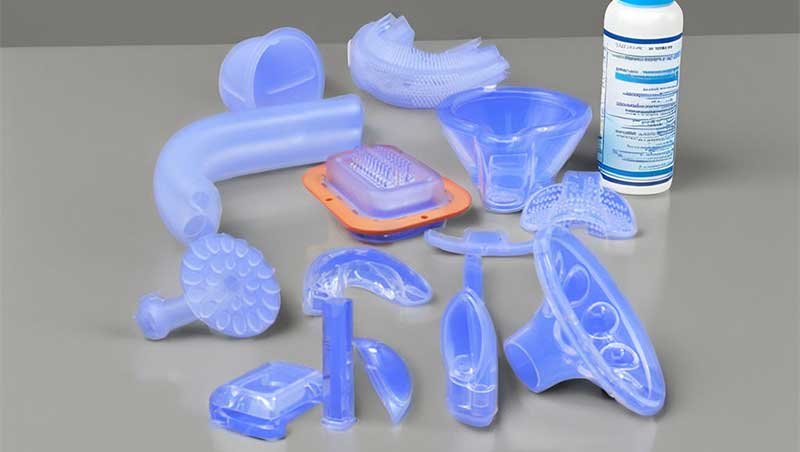
硬化(加硫)
射出成形後、金型は特定の温度に維持され、硬化プロセス(硬化とも呼ばれる)が開始されます。 加硫これは、シリコーンポリマー鎖を架橋させる化学反応を伴い、液体材料を固体の弾性構造へと変化させます。完全な加硫を確実に行うため、硬化温度と硬化時間は厳密に管理されます。通常、硬化温度は250°F~300°F(121°C~149°C)の範囲で、処理時間は部品の厚さや複雑さに応じて数分から30分以上まで変化します。
後処理
硬化が完了すると、金型は冷却され、固化したシリコン部品が取り出されます。後処理には以下の手順が含まれます。
- トリミングとバリ取り: オペレーターは、バリと呼ばれる余分な材料をパーティングラインとゲートから除去して、目的の形状と表面仕上げを実現します。
- 追加硬化(後硬化): 成形された部品は高温で加熱され、機械的特性が向上し、完全な架橋が保証されます。
- 表面処理: 接着性、外観、機能性を向上させるために、プラズマ処理、コーティング、接着などのさまざまなプロセスが適用されます。
- 品質検査: 検査員は徹底的な検査を実施し、部品が寸法、機械的特性、外観品質に関する指定された基準を満たしていることを確認します。
これらの後処理手順は製品にとって不可欠であり、意図された用途に必要な仕様とパフォーマンス基準を満たすことを保証します。
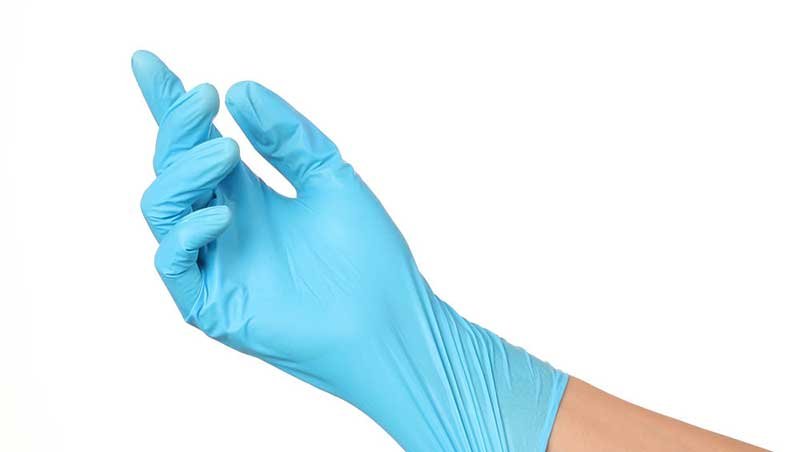
シリコーン射出成形の利点
シリコン射出成形にはいくつかの重要な利点があり、高品質で精密に設計されたシリコン製品の製造に最適な選択肢となっています。
- 精度と再現性このプロセスを用いることで、厳しい公差を持つ複雑な形状を製造できます。これは、高い性能と一貫性が求められる医療機器、自動車、電子機器などの業界にとって特に有利です。
- 無駄を最小限に抑えるシリコーン射出成形では、材料を正確に使用することで無駄を最小限に抑え、余分なトリミングの必要性を減らし、コスト削減に貢献します。
- 短いサイクルタイムシリコーン射出成形は、温度、圧力、射出速度などの要素を制御することでサイクルタイムを短縮し、生産速度の向上、生産性の向上、リードタイムの短縮を実現します。
全体として、シリコーン射出成形は、複雑な機能と高性能が求められる高品質のシリコーン製品を製造するための、コスト効率が高く、効率的で、多用途なソリューションを提供します。
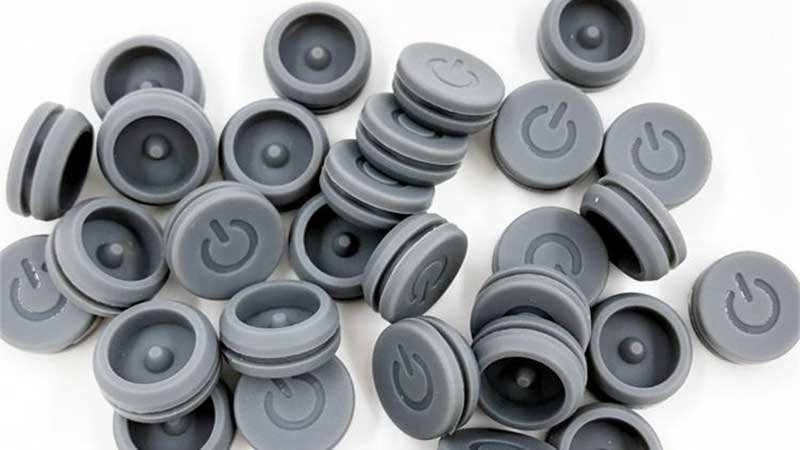
シリコーン射出成形の欠点
シリコーン射出成形には、慎重に検討すべき課題も存在します。主な欠点は次のとおりです。
- 初期ツールコストが高い射出成形用の金型は、特に複雑なデザインの場合、高価です。こうした初期費用は、予算が限られているプロジェクトや生産量が少ないプロジェクトでは、大きな障害となる可能性があります。
- 材料の制限射出成形プロセスでは主に液状シリコーンゴム(LSR)が使用されます。LSRは、あらゆる用途に必要な特定の材料特性を備えていない場合があります。この制限により、性能要件に基づいた慎重な材料選定が必要となります。
シリコン射出成形は強力な製造技術ですが、製品開発におけるその応用を最適化するには、これらの潜在的な欠点を理解して対処することが重要です。
シリコーン射出成形の用途
シリコーン射出成形は、様々な業界で利用されている汎用性の高い製造プロセスです。以下の表は、シリコーン射出成形の最も一般的な用途をまとめたものです。
業界 | アプリケーション |
医学 | カテーテル、外科用シール、人工器官、医療用手袋、チューブ。 |
自動車 | ガスケット、シール、ホース、エンジンマウント、電気絶縁部品など。 |
エレクトロニクス | キーパッド、コネクタ、シール、ガスケット、絶縁体、スイッチ パッドなど。 |
航空宇宙 | シール、ガスケット、断熱パネル、燃料ホース、O リング。 |
消費財 | キッチン用品、ベビーケア用品、パーソナルケア製品、ウェアラブル。 |
これらの用途では、生体適合性、柔軟性、耐熱性、耐久性などのシリコーン材料の独自の特性により、シリコーン射出成形の適応性が強調されます。
結論
シリコーン射出成形は、比類のない精度と汎用性を備えた、極めて重要な製造プロセスです。複雑で高品質な部品を製造できるため、医療機器、自動車、家電、航空宇宙などの分野では欠かせない存在となっています。その利点と限界を理解することで、メーカーはこの技術の潜在能力を最大限に活用し、イノベーションを推進し、優れたシリコーン製品の製造を確実に行うことができます。
リソース: