Some silicone products look finished after molding — but still smell like chemicals, or fail final testing.
That’s often due to skipping or misunderstanding a key step: post curing, or what we call in Chinese “硅胶二次硫化”.
When done right, post curing enhances performance, ensures safety, and meets demanding global compliance.
Post curing is a secondary heat treatment that removes residual volatiles, improves mechanical properties, and ensures silicone parts meet food-grade, medical, or industrial standards.
So yes, post curing isn’t just a technical step—it’s a profit-protection strategy. Especially if you’re rebranding these products in high-compliance markets like the U.S. and Europe.
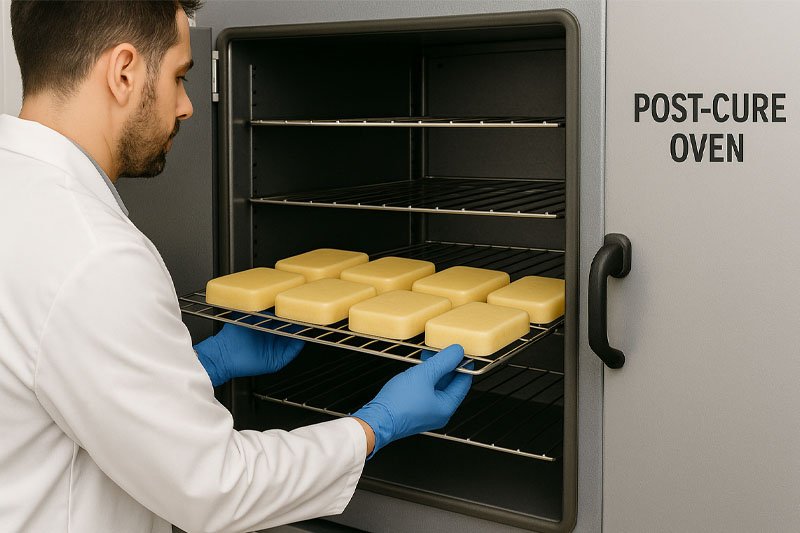
What Is Silicone Post Cure?
Post curing refers to a controlled high-temperature baking process.
It typically occurs after the initial vulcanization (curing) of silicone rubber, especially LSR (liquid silicone rubber) or HTV (high-temperature vulcanized rubber) products.
The goal is to:
- Remove residual crosslinking agents, plasticizers, or volatiles
- Enhance thermal stability and mechanical strength
- Ensure the part complies with FDA, LFGB, REACH, RoHS, etc.
- Eliminate that “rubbery” or chemical odor
At Ruiyang Silicone, we set our post cure ovens at around 200°C for 4-6 hours, but the exact specs depend on the product thickness and formulation.
When Is Post Cure Needed?
Not all silicone products need a second vulcanization. But many do—especially in these cases:
- Food-contact items (baby spoons, baking molds, etc.)
- Medical-grade components (tubes, valves)
- Odor-sensitive products (toys, electronics gaskets)
- High-performance parts requiring excellent aging and compression set resistance
For example, if we’re producing silicone baby pacifiers for a European distributor, skipping post cure is a shortcut to failed migration tests.
Even worse? Your end-customer might accuse you of “toxic materials” or non-compliance. That’s a nightmare for importers.
What Happens If You Skip It?
Short answer: A lot can go wrong.
Here’s what we’ve seen from rushed or unprofessional suppliers:
- Strong chemical smells on finished products
- Sticky surfaces or surface blooming
- Poor high-temperature resistance
- Failure to pass FDA 21 CFR 177.2600 or LFGB food safety tests
- Discoloration or yellowing over time
- Poor bonding or adhesion if used with other materials
Post curing isn’t a marketing gimmick. It’s science-backed, compliance-driven processing.
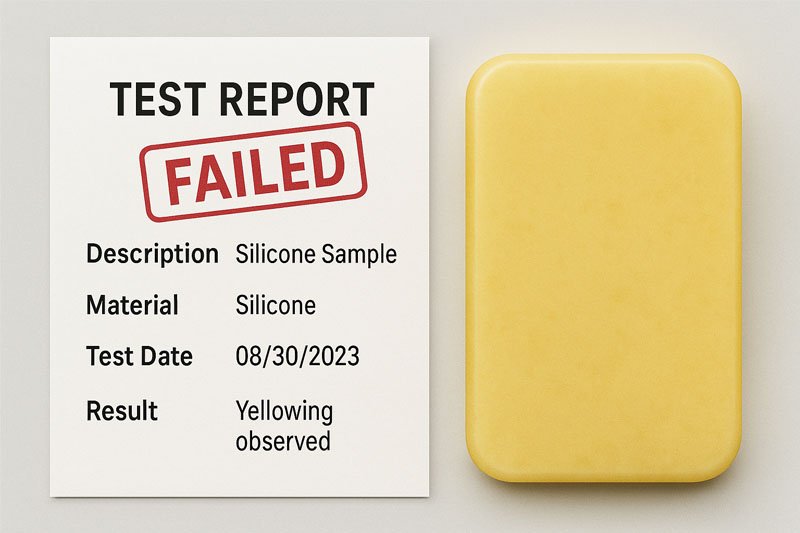
How We Handle Post Cure at Ruiyang Silicone
Our facility has dedicated post cure ovens, with controlled temperature zones.
We treat this step with the same care as molding or design.
Here’s how we do it:
- Sorting and preparation – We check every batch before post curing. No contamination allowed.
- Oven settings – Typically 200–220°C, duration adjusted based on product type and volume.
- Clean airflow systems – Keeps ovens free from dust or oil residues.
- Batch recording – Each curing cycle is tracked with time, temperature, and product ID.
- Final inspection – We re-test key parameters: smell, flexibility, color, and compliance.
This ensures that when John White (or any importer) receives the goods, he doesn’t need to worry about chemical odors or customs issues.
Certifications That Require Post Cure
Many customers ask, “Do I really need this extra step?”
If your end customers require any of these certifications, the answer is yes:
- FDA 21 CFR 177.2600 – For food-contact silicone in the U.S.
- LFGB – For German/EU food compliance
- REACH – For substances of high concern
- RoHS – For electronics silicone components
- ISO 10993 – For medical devices
Our post cure process is specifically designed to help customers pass these tests without hassle.
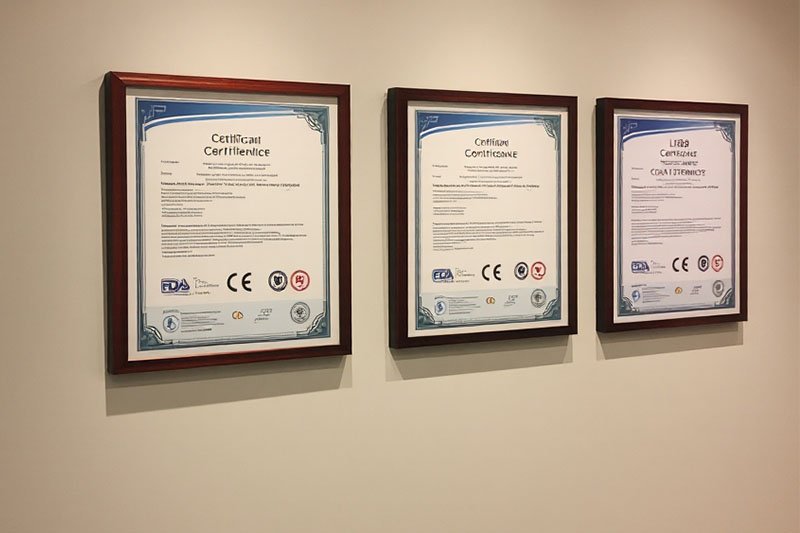
Does Post Cure Affect Cost and Lead Time?
Of course. It adds time—typically 1 extra day to your lead time.
It also adds a small cost, mainly due to energy and labor.
But here’s the ROI:
- Better market access (especially in EU/US)
- Fewer product returns
- Happier distributors who trust your quality
- No bad reviews from “chemical smell” issues on Amazon or retail shelves
In the long run, it’s cheaper than customer complaints, rejections, or customs seizures.
If your business model relies on rebranding and premium pricing, this step is your secret weapon.
Common Myths About Silicone Post Cure
Let me bust a few myths:
Myth 1: “If the silicone looks good, it’s cured.”
Nope. Volatiles aren’t always visible.
Myth 2: “Only medical products need post cure.”
Wrong. Even kitchenware can fail food-grade tests without it.
Myth 3: “Post cure is just a fancy way to charge more.”
Tell that to the customs officer rejecting your container because of odor or unverified safety compliance.
Our job as your silicone partner is to get past the myths and protect your brand.
How to Confirm If Your Supplier Does Post Cure?
Here’s a checklist I give our partners:
- Ask if they have dedicated post cure ovens
- Request batch records or photos of the curing setup
- Check if they’ve passed FDA, LFGB, REACH tests
- Request a pre-shipment smell test report or sample
- If in doubt, send a product for third-party testing
At Ruiyang Silicone, we welcome this level of scrutiny. In fact, we encourage it.
Transparency builds trust—and I know trust is currency in B2B.
Conclusion
Post curing isn’t an “extra”—it’s essential.
Whether you’re selling baby spoons, gaskets, or medical devices, don’t skip this step.
We’ve invested in the tech and process so you don’t have to worry.
Let’s build products that pass every test—and make you proud to put your label on them.