Silicone is known for its flexibility and resilience, making it a popular choice in various industries from medical devices to household products. A key attribute of silicone is its tensile strength, which is essential for its performance.
Tensile strength of silicone measures the maximum stress it can endure before breaking. This property is critical for assessing silicone’s durability and strength under tension. Typically, silicone’s tensile strength ranges between 200 and 1500 psi, depending on its type and formulation. This robustness makes it suitable for numerous applications where both flexibility and durability are important.
Understanding silicone’s tensile strength can guide you in selecting the right type for your needs.
How is Silicone Tensile Strength Measured?
Tensile strength is gauged using a tensile test, where a silicone sample is stretched until it breaks. The force applied during this process is recorded, providing a clear measure of the silicone’s strength under stress.
Factors Influencing Tensile Strength
- Formulation: Different formulations can significantly impact tensile strength. High-performance silicones often contain additives that boost their strength.
- Curing Process: Proper curing is vital as it ensures silicone reaches its maximum strength potential.
- Temperature and Environment: Silicone’s tensile strength can vary with temperature and environmental conditions. High temperatures may reduce tensile strength, while low temperatures can make it more brittle.
Research shows that adding specific agents to silicone can enhance its tensile strength, making it more suitable for demanding applications.
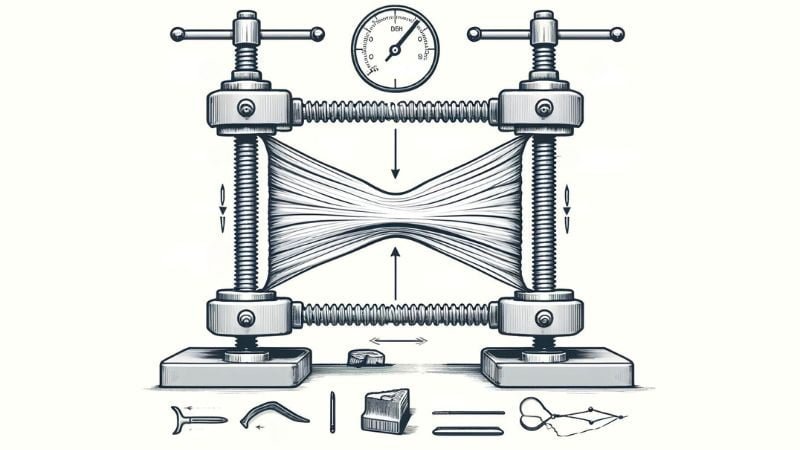
Why is Tensile Strength Important in Silicone?
Tensile strength indicates how well a material can withstand stress without breaking. For silicone, high tensile strength means it can endure stretching, pulling, and tension, which is crucial for many applications.
Applications Requiring High Tensile Strength
- Medical Devices: High tensile strength is essential for medical-grade silicone used in implants, catheters, and other devices that experience tension.
- Seals and Gaskets: In industrial settings, silicone seals and gaskets must remain intact under pressure and tension to prevent leaks.
- Consumer Products: Items like silicone bakeware, phone cases, and wearables need high tensile strength for durability and longevity.
How Does Silicone Compare to Other Materials?
When comparing silicone to rubber and plastic, it often surpasses them in tensile strength and other properties.
Comparison with Rubber
- Heat Resistance: Silicone maintains its strength at higher temperatures compared to rubber.
- Flexibility: Silicone stays flexible across a broader temperature range.
- Longevity: Silicone typically outlasts rubber due to its superior resistance to environmental factors.
Comparison with Plastic
- Elasticity: Silicone is more elastic than most plastics, allowing it to stretch without breaking.
- Durability: Silicone can withstand harsh conditions that might degrade plastic over time.
What are the Limitations of Silicone Tensile Strength?
Despite its strengths, silicone has some limitations.
Potential Issues
- Temperature Sensitivity: Extremely high temperatures can weaken silicone’s tensile strength.
- Chemical Exposure: Some chemicals can degrade silicone, affecting its strength.
- Mechanical Fatigue: Repeated stretching and bending over time can lead to material fatigue.
Enhancing Silicone Tensile Strength
Manufacturers can boost silicone’s tensile strength through various methods, such as adding reinforcing agents and optimizing the curing process.
Reinforcing Agents
- Silica: Adding silica can significantly increase tensile strength.
- Carbon Black: Enhances strength and durability in some formulations.
Advanced Formulations
- High-Performance Silicones: These are specially designed to offer superior tensile strength and other enhanced properties.
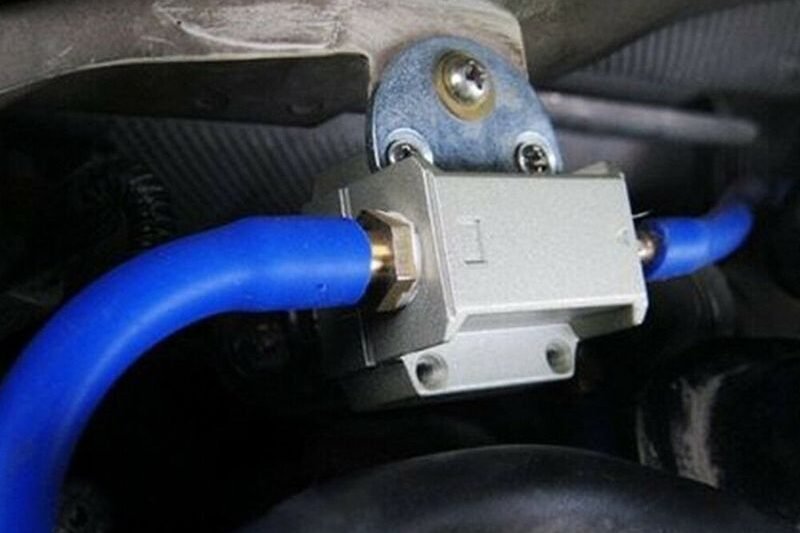
Real-World Applications of High-Tensile Strength Silicone
High-tensile strength silicone is valuable in many demanding fields.
Aerospace Industry
In aerospace, silicone seals and gaskets must withstand extreme conditions. High tensile strength ensures these components perform reliably under high pressure and temperature variations.
Medical Field
Silicone used in medical implants and devices must resist breaking under tension, ensuring safety and effectiveness.
Electronics
In electronics, silicone is used in flexible circuits and connectors. High tensile strength allows these components to maintain integrity under repeated stress.
Conclusion
Silicone’s tensile strength is a critical factor in determining its suitability for various applications. By understanding and utilizing this property, you can ensure the longevity and reliability of silicone products in medical, industrial, or consumer settings. High-tensile strength silicone is preferred for its unmatched combination of flexibility, durability, and reliability.