Have you ever wondered how some products can withstand extreme temperatures, resist chemicals, and maintain their flexibility over time? The answer lies in the remarkable properties of silicone tubing. This versatile material has become an essential component in a wide range of industries, from healthcare to food processing, thanks to its exceptional characteristics. In this article, we will dive into the world of silicone tubing, exploring its unique properties, applications, and the advantages it offers. So, grab a cup of coffee, sit back, and let’s embark on this enlightening journey!
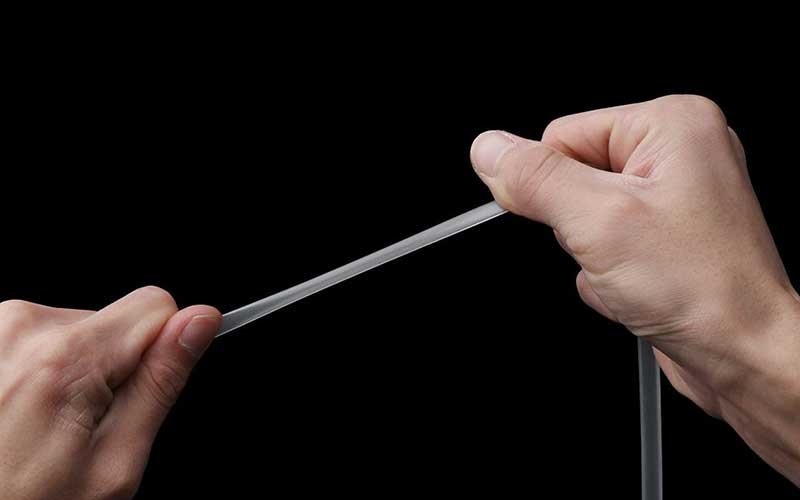
The Marvelous World of Silicone Tubing
Silicone tubing is a flexible, hollow tube made from silicone, a synthetic polymer composed of silicon, oxygen, carbon, and hydrogen. It exhibits a myriad of fascinating properties that make it stand out from other materials. Let’s explore some of its most remarkable features:
1. Temperature Resistance: A Hot or Cold Companion
Imagine a medical device that needs to function flawlessly in extreme temperatures or an industrial process that requires fluid transfer at high temperatures. Silicone tubing comes to the rescue! With its excellent temperature resistance, it can withstand both freezing cold and scorching heat. Silicone tubing can comfortably operate in a temperature range of -60°C to 200°C (-76°F to 392°F), making it an ideal choice for various demanding applications.
2. Flexibility: Bend it, Twist it, Shape it
Flexibility is key when it comes to tubing, especially in applications that require maneuverability and easy installation. Silicone tubing boasts exceptional flexibility, allowing it to bend, twist, and shape to fit different configurations and tight spaces. Whether it’s navigating around complex machinery or passing through intricate systems, silicone tubing adapts effortlessly, making it an invaluable component in diverse industries.
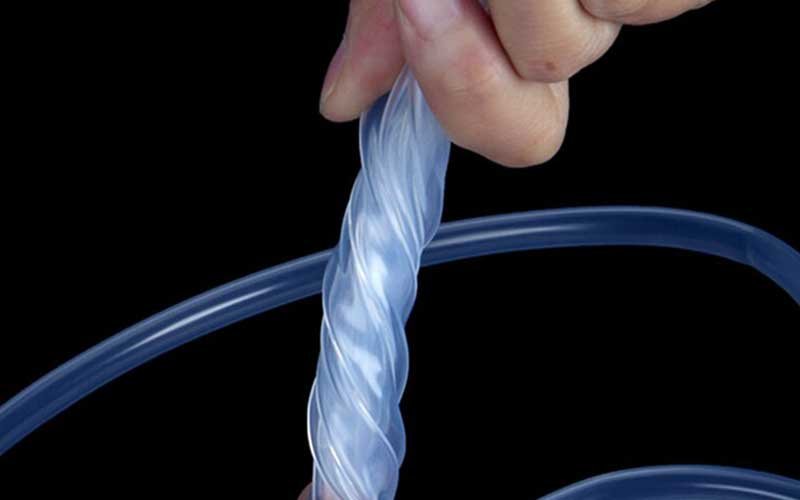
3. Chemical Resistance: Unfazed by Harsh Substances
In some industries, tubing comes into contact with aggressive chemicals, solvents, or acids. The ability to resist chemical attack is paramount for ensuring long-lasting performance and maintaining product integrity. Silicone tubing exhibits exceptional chemical resistance, safeguarding against corrosion, degradation, and the leaching of substances that could compromise the materials being transported. It serves as a reliable guardian, protecting against a wide range of chemicals encountered in various industrial processes.
4. Biocompatibility: Keeping Health and Wellness in Mind
When it comes to medical devices, pharmaceutical applications, or food processing, safety and biocompatibility are of utmost importance. Silicone tubing shines in this aspect, as it is biologically inert and non-toxic. It is widely used in the healthcare industry for applications such as fluid transfer, drug delivery, and surgical implants. Furthermore, its hypoallergenic nature makes it an ideal choice for sensitive individuals, ensuring that it meets the highest standards of safety and efficacy.
5. Electrical Insulation: Powering Innovation
Silicone tubing possesses excellent electrical insulation properties, making it a go-to material for applications requiring electrical protection and insulation. From high-voltage cables to electronic devices, silicone tubing provides a barrier against electrical current, preventing leakage and ensuring optimal performance. Its insulating properties, combined with its temperature resistance, make it an invaluable asset in the world of electronics and electrical engineering.
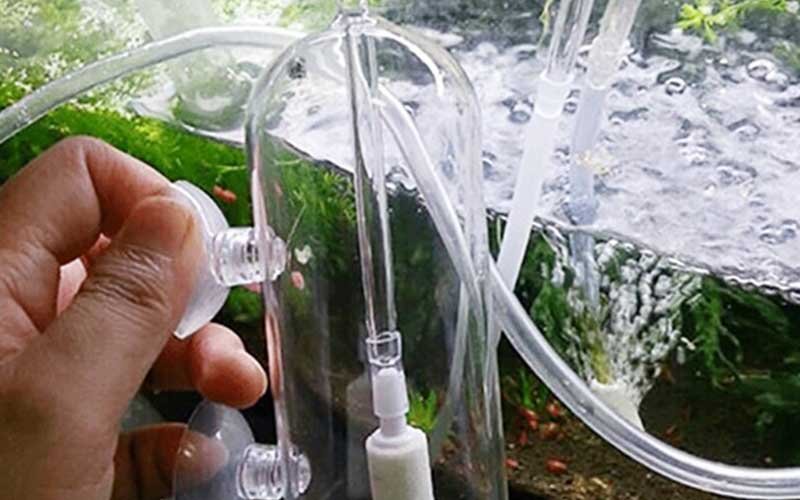
Diverse Applications of Silicone Tubing
The versatility of silicone tubing opens up a vast array of applications across various industries. Let’s explore a few examples where silicone tubing plays a crucial role:
1. Medical and Healthcare
Silicone tubing finds extensive use in the medical field due to its biocompatibility and flexibility. It is utilized in applications such as catheters, intravenous lines, peristaltic pumps, and respiratory equipment. Its ability to withstand sterilization processes, resistance to kinking, and compatibility with different medications and bodily fluids make it an indispensable material in the healthcare sector.
2. Food and Beverage
In the food and beverage industry, silicone tubing is highly sought after for its sanitary properties and resistance to extreme temperatures. It is commonly used for fluid transfer, dispensing beverages, and as a conduit for food ingredients. Silicone tubing ensures that the quality and taste of the product remain intact while meeting stringent hygiene standards imposed by food regulatory bodies.
3. Industrial and Manufacturing
Silicone tubing is a vital component in numerous industrial applications, including chemical processing, automotive manufacturing, and machinery. Its ability to withstand harsh chemicals, high temperatures, and mechanical stress makes it an excellent choice for fluid transfer, coolant systems, gaskets, and seals. Silicone tubing enhances the efficiency and durability of industrial processes, ensuring seamless operations.

The Advantages of Silicone Tubing
Now that we’ve explored the remarkable properties and diverse applications of silicone tubing, let’s delve into the advantages it offers:
1. Longevity and Durability
Silicone tubing exhibits exceptional durability, making it a long-lasting investment. Its resistance to degradation, weathering, and wear ensures that it can withstand the test of time, even in demanding environments. This durability translates into cost savings, reduced maintenance, and increased operational efficiency.
2. Ease of Cleaning and Maintenance
Maintaining hygiene and cleanliness is crucial in industries such as food processing, pharmaceuticals, and healthcare. Silicone tubing’s smooth and non-porous surface allows for easy cleaning and sterilization, preventing the growth of bacteria and ensuring product purity. Its low adherence to substances minimizes the risk of contamination, making it a favored choice in industries where hygiene is paramount.
3. Versatility and Customization
Silicone tubing offers versatility and customization options to suit specific application requirements. It can be manufactured in various sizes, shapes, and colors, allowing for seamless integration into existing systems. Additionally, silicone tubing can be reinforced with different materials, such as polyester or wire, to enhance its strength and flexibility, further expanding its range of applications.
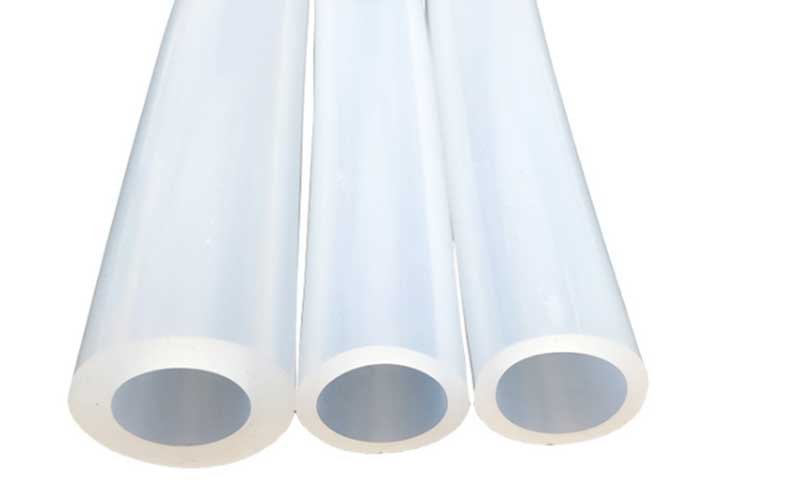
Frequently Asked Questions (FAQ)
Q: What is silicone tubing used for?
A: Silicone tubing has a wide range of applications across various industries. It is commonly used in medical devices, food and beverage processing, industrial processes, and electrical engineering. Its flexibility, temperature resistance, and chemical resilience make it suitable for fluid transfer, insulation, and protection in diverse settings.
Q: Is silicone tubing stretchy?
A: Yes, silicone tubing is known for its excellent stretchability and flexibility. It can be bent, twisted, and shaped to fit different configurations and tight spaces without losing its elasticity. This property makes it easy to install and adapt to various applications.
Q: What is the temperature range for silicone tubes?
A: Silicone tubes can withstand a broad temperature range. Typically, silicone tubing can operate effectively in temperatures ranging from -60°C to 200°C (-76°F to 392°F). This exceptional temperature resistance allows silicone tubing to function reliably in both extreme cold and hot environments.
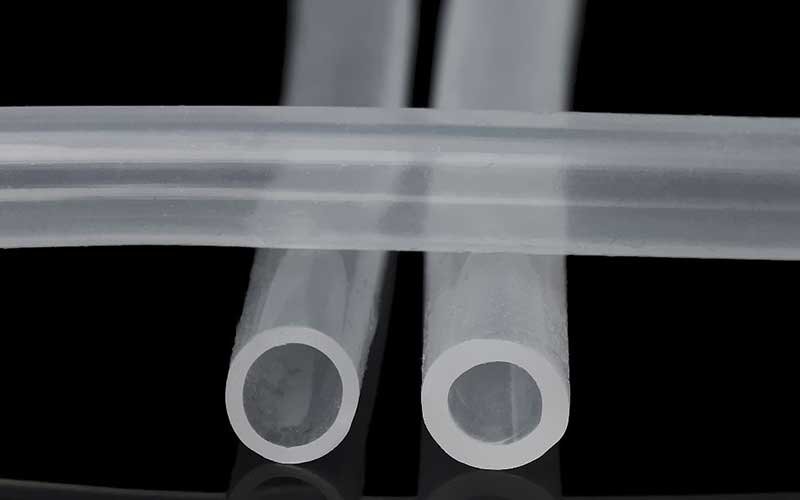
Q: What’s the diameter of a silicone tube?
A: The diameter of silicone tubing varies depending on the specific application and requirements. Silicone tubing is available in a wide range of diameters, from small sizes as thin as a few millimeters to larger diameters exceeding several inches. The diameter needed will depend on the intended use and the flow rate of the substance being transferred.
Q: How do you measure silicone tube size?
A: Silicone tubing size is typically measured using the inside diameter (ID) or the outside diameter (OD). The ID refers to the inner measurement of the tube, while the OD refers to the outer measurement. The choice of measurement method depends on the specific application and industry standards.
Q: How do you cut silicone tubing?
A: Cutting silicone tubing is a relatively straightforward process. To cut silicone tubing accurately, you can use a sharp utility knife, scissors, or specialized tubing cutters. Ensure that the tool you use is clean and sharp to achieve clean, precise cuts.
Q: Is silicone easy to cut?
A: Yes, silicone is relatively easy to cut, especially when using the appropriate tools. The flexibility and softness of silicone tubing make it easier to work with compared to some other materials. With a sharp tool and proper technique, silicone tubing can be cut cleanly and accurately.
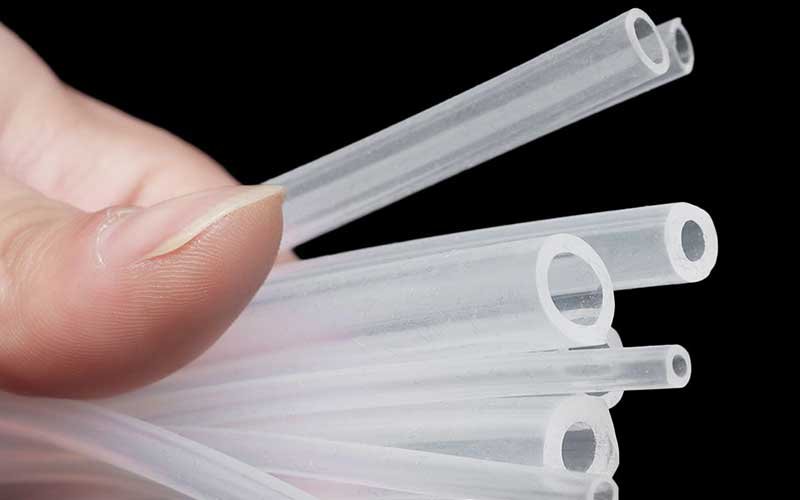
Q: What is an alternative to silicone tubing?
A: If silicone tubing is not suitable for your application or you are looking for alternatives, there are several options available. Some common alternatives to silicone tubing include fluoropolymer tubing, such as PTFE (polytetrafluoroethylene) tubing, which offers excellent chemical resistance and high-temperature capabilities. Other alternatives include thermoplastic elastomer (TPE) tubing, PVC (polyvinyl chloride) tubing, and rubber tubing. The choice of alternative tubing material depends on the specific requirements of your application.
Q: Why are tubes of silicone so expensive?
A: Silicone tubes can be more expensive compared to other materials due to the higher cost of raw materials and the manufacturing process involved. Silicone itself is a specialized material with unique properties, requiring specific manufacturing techniques and quality control measures. Additionally, the demand for silicone tubes in various industries contributes to the pricing. Despite the higher cost, silicone tubes often provide superior performance and longevity, making them a worthwhile investment in certain applications.
Q: What is the difference between silicone hose and tubing?
A: The terms “hose” and “tubing” are often used interchangeably, but they can refer to different forms of silicone products. Generally, silicone hoses are larger and thicker than silicone tubing. Hoses are typically designed for higher-pressure applications and conveyance of fluids or gases. Silicone tubing, on the other hand, tends to be more flexible and used for various applications such as fluid transfer, insulation, or protection in systems where lower pressures are involved.
Click to learn more about Silicone hoses.
Choose Quality, Choose RY Silicone
When it comes to silicone tubing, quality matters. As a leading silicone product manufacturer, we understands the importance of delivering exceptional products that meet the highest standards. With our expertise in silicone manufacturing and commitment to quality management, RY Silicone ensures that silicone tubing exceeds expectations in terms of performance, reliability, and safety.
Remember, if you have any specific questions about silicone tubing or need assistance with your unique requirements, don’t hesitate to reach out to RY Silicone for expert guidance and support.