When selecting materials for manufacturing, the debate between silicone and rubber surfaces frequently. Both materials boast unique properties, making the choice between them critical for product performance and longevity. But how do you decide which is better for your specific application? The answer lies in understanding each material’s strengths, limitations, and suitability for different environments.
This guide is all about helping you understand more about silicone and rubber. We’ll look at what makes them different, where they’re used, and how to choose the right one for your project. Whether you’re buying materials or making products, getting to know these materials will help you make better choices.
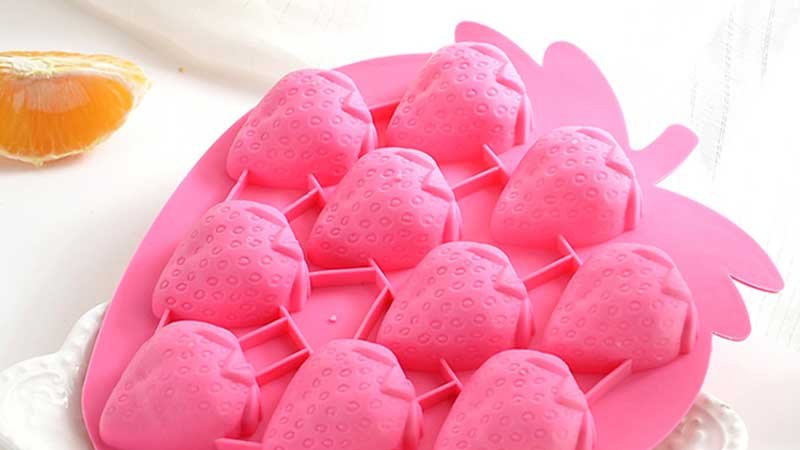
What is Silicone
Silicone is a synthetic material made from silicon, oxygen, carbon, and hydrogen. It’s not the same as silicon, the element used in electronics; silicone is a polymer with a wide range of uses.
Silicone Rubber Properties
What makes silicone stand out is its ability to keep its strength and shape in both very hot and very cold environments, which many other materials can’t do. It’s also very resistant to water and many chemicals, making it last longer in harsh conditions. Silicone is known for being durable, which means it can be used in lots of different ways, from kitchen tools to car parts.
What is Rubber
Rubber, on the other hand, can be natural or synthetic. Natural rubber comes from the sap of rubber trees, while synthetic rubber is made from petroleum products.
Rubber Properties
Rubber is famous for being stretchy and strong at the same time. It can go back to its original shape after being stretched or squished, which is why it’s used in things like tires and elastic bands. Natural rubber is very flexible and has a good grip, while synthetic rubber can be made to be even stronger or resistant to oils and chemicals. Because rubber can be collected from trees or made from oil, it’s usually cheaper than silicone, making it a good choice for a wide range of products.

Key Differences Between Silicone and Rubber
When choosing materials for different uses, it’s important to know how they handle extreme temperatures, react with chemicals, and if they’re safe for things like medical and food use.
- Temperature Resistance: Silicone is great at dealing with both very hot and very cold temperatures, making it a go-to for tough conditions. It can handle temperatures from really cold, at -55°C (-67°F), to really hot, up to 300°C (572°F). Rubber doesn’t do as well with extreme temperatures. Natural rubber gets brittle in the cold and starts breaking down in the heat, and while synthetic rubber is a bit better, it still can’t beat silicone.
- Chemical and Environmental Resistance: Silicone wins again in harsh conditions, resisting damage from many chemicals, sunlight, and ozone. This makes it last longer, especially outdoors. Rubber is a bit more sensitive, with natural rubber struggling with oils and synthetic rubber only being resistant to certain chemicals.
- Safety and Health Considerations: Silicone is the safer choice for people allergic to latex, making it great for medical devices and kitchen tools. It doesn’t react with food and is easy to clean. Rubber, especially natural rubber, can cause allergies, making it less ideal for products that touch skin or food.
Feature | Silicone | Rubber |
---|---|---|
Temperature Resistance | Excellent: -55°C to 300°C (-67°F to 572°F), with special types going higher. | Limited: -60°C to 80°C (-76°F to 176°F) for natural rubber, with synthetic versions varying. |
Chemical and Environmental Resistance | High resistance to oils, acids, solvents, UV light, and ozone. Ideal for harsh chemical environments. | Varies by type: Natural rubber is vulnerable to oils and solvents, while synthetic rubber can be formulated for specific resistances but generally lacks the broad resistance of silicone. |
Safety and Health Considerations | Latex-free, making it safe for people with allergies. Used in medical and food applications due to its inert nature and ability to be sterilized. | Natural rubber contains latex, which can cause allergies. Its use is more limited in direct human contact applications due to potential health risks. |
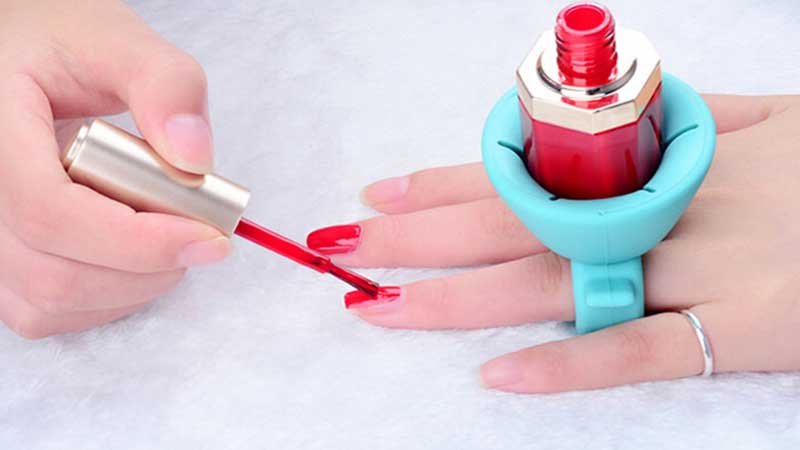
Applications and Industry Preferences
Both silicone and rubber have their special roles for different industries. Here’s how they fit into various applications:
Industrial and Automotive Applications
- Silicone is the star when it comes to things that need to handle very hot or very cold conditions. It’s used for seals, gaskets, and tubing in machines and vehicles because it doesn’t get damaged easily by temperature changes. This makes it perfect for engines and other parts that get really hot.
- Rubber is great for everyday needs. It’s used in seals, tires, and parts that need to absorb shocks, like anti-vibration mounts. It’s the go-to material for many parts of a car or machine that need to be strong and flexible.
Medical and Food Applications
- Silicone shines in the medical and food industries because it’s safe and doesn’t react with other substances. It’s used in medical devices and implants that go inside the body, and for kitchen tools and cookware because it can be easily cleaned and doesn’t hold onto bacteria.
- Rubber has its limits here because of safety concerns. Natural rubber, which contains latex, can cause allergic reactions, and there’s a risk of contamination. This means it’s not often used in products that come in contact with food or are used in medical settings.
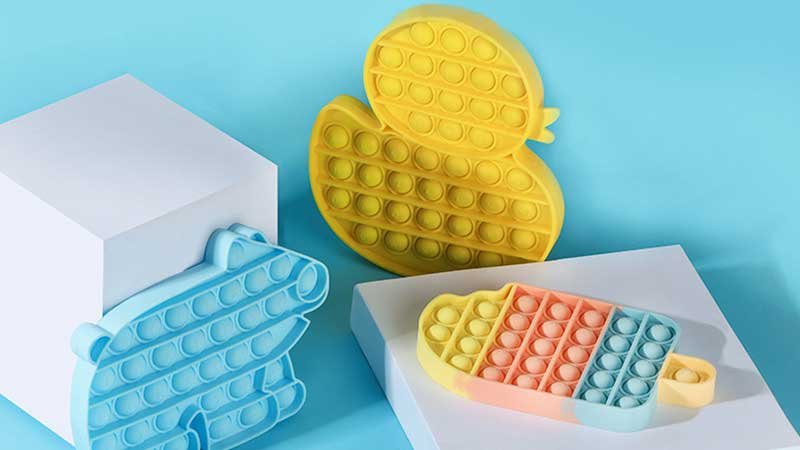
Advantages and Limitations
When deciding between silicone and rubber for a project, it’s important to consider both the upfront costs and the long-term benefits. Here’s how these materials stack up in terms of cost and performance, especially under tough conditions.
Cost Analysis
- Initial Cost vs. Long-Term Benefits: Silicone generally costs more upfront than rubber. However, its durability, temperature resistance, and chemical stability can lead to lower maintenance and replacement costs over time. This makes silicone a cost-effective choice for applications where long-term reliability is critical.
- Economic Impact of Material Selection: Choosing the right material affects not just the cost of production but also the lifespan and maintenance needs of the final product. For example, using silicone in high-performance parts may reduce the need for frequent replacements, ultimately saving money for both manufacturers and consumers.
Performance in Extreme Conditions
- Silicone vs. Rubber: Silicone excels in extreme temperatures and harsh environments, maintaining its integrity where rubber might fail. It can withstand high heat without melting or becoming brittle in cold, making it ideal for outdoor or automotive applications exposed to varying climates.
- Case Studies and Scenarios: Imagine a scenario where a company switches from rubber to silicone for its outdoor equipment seals. Initially, the switch seems costly, but over time, the silicone seals require fewer replacements due to weather-related wear and tear, proving the value of investing in a more resilient material.
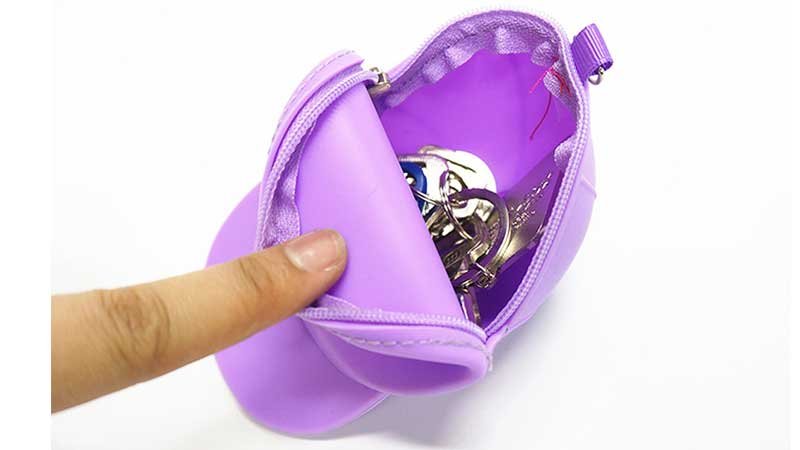
Choosing the Right Material
Selecting between silicone and rubber involves more than just comparing prices or performance under ideal conditions. Here’s what to keep in mind to ensure you pick the right material for your project:
Factors to Consider
- Application Requirements: Think about the environment where the product will be used. Will it face extreme temperatures, harsh chemicals, or heavy wear and tear? Silicone might be your best bet for tough conditions, while rubber could be enough for more moderate uses.
- Longevity and Durability vs. Cost-Effectiveness: Consider how long you need the product to last without needing repairs or replacements. Silicone often offers greater durability, which could save money in the long run, despite its higher initial cost.
- Environmental Impact and Sustainability: Today, it’s also important to think about the environmental footprint of the materials you choose. Silicone is durable and long-lasting, which might mean less waste over time, but rubber, especially natural rubber, can be a more sustainable choice since it’s a renewable resource.
Consultation and Customization
- Expert Advice: Material experts and manufacturers can provide valuable insights into the best material for your specific needs. They can help you weigh the pros and cons of silicone and rubber based on your project’s unique requirements.
- Customization Options: Both silicone and rubber products can be customized to meet specific needs. Whether you’re looking for a particular level of flexibility, strength, or resistance to conditions, manufacturers can often adjust the material formulation to fit your requirements.
Need help deciding between silicone and rubber for your project? We’re here to help! Contact us for expert advice and find out which material is best for you. Plus, check out our website for stories and resources on how both materials are used in real-world projects.
If you are looking for a professional silicone products manufacturer, please contact us.