Electronics manufacturing faces risks from static discharge and high heat, potentially damaging sensitive components and causing costly production delays. Can silicone mats help overcome these challenges?
Silicone mats are essential in electronics manufacturing because they offer effective anti-static and heat-resistant properties. They protect sensitive components from electrostatic discharge, dissipate heat efficiently, and ensure a safer, more efficient workspace, improving both product quality and manufacturing efficiency.
But there’s more to silicone mats than just heat resistance and anti-static protection. Let me take you deeper into understanding why they’ve become an indispensable part of modern electronics production.
How Do Silicone Mats Protect Against Electrostatic Discharge (ESD)?
Static electricity is a silent threat in electronics manufacturing, causing unseen damage that could lead to product failures. How exactly can silicone mats help eliminate this threat?
Silicone mats provide excellent ESD protection by dissipating static charges safely. They are specially formulated to conduct electricity at a controlled rate, preventing sudden electrostatic discharge that damages sensitive electronics components.
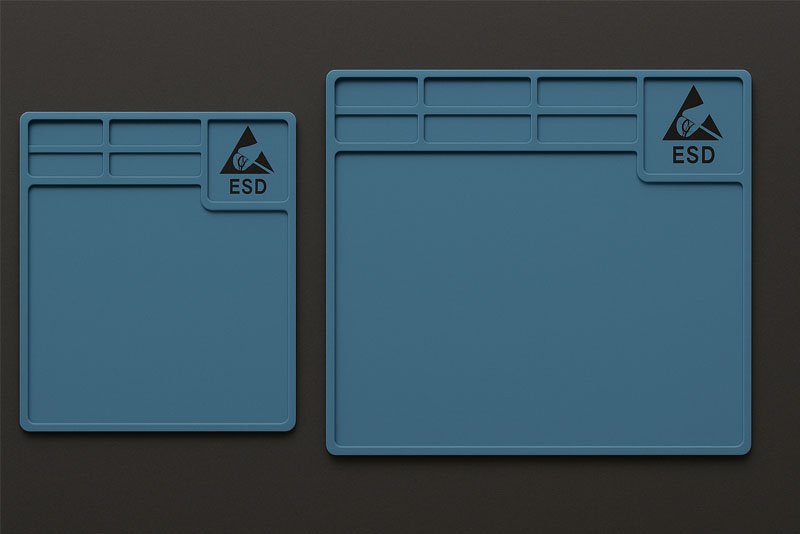
Understanding Electrostatic Discharge
Electrostatic discharge happens when two electrically charged objects come into contact or close proximity, causing electrons to jump from one surface to another. In electronics manufacturing, even minor ESD events can permanently damage semiconductor devices and printed circuit boards (PCBs). The table below explains common ESD risks and potential impacts on electronics:
ESD Source | Risk Level | Possible Damage |
---|---|---|
Human body discharge | High | IC damage, component failure |
Work surface friction | Moderate | PCB malfunction, data loss |
Tool or machine discharge | High | Complete device failure |
How Silicone Mats Prevent ESD Damage
Silicone mats designed for electronics manufacturing contain carbon or other conductive materials. These additives create paths for static electricity to safely dissipate into grounding points. Here are three ways silicone mats achieve this:
- Controlled Conductivity: They slowly release static charge, preventing sudden, damaging electrical surges.
- Grounding Integration: Mats come equipped with grounding cords to ensure safe discharge into an earth ground.
- Insulative Surface: Silicone mats also insulate against unintended electrical conduction, protecting delicate components.
In my experience, manufacturers who switch to high-quality silicone ESD mats consistently report fewer product returns and reduced damage claims from customers. This simple upgrade significantly improves product reliability and consumer trust.
Why Is Heat Resistance Important in Electronics Manufacturing?
Electronic components generate and endure significant heat during production and testing. Without proper heat management, manufacturers face quality and safety issues. Why is silicone the best material for managing heat?
Silicone mats offer exceptional heat resistance, typically handling temperatures from -60°C to over 230°C (-76°F to 446°F). They protect surfaces, components, and workers from heat-related damage and accidents, improving overall safety and efficiency in the production environment.
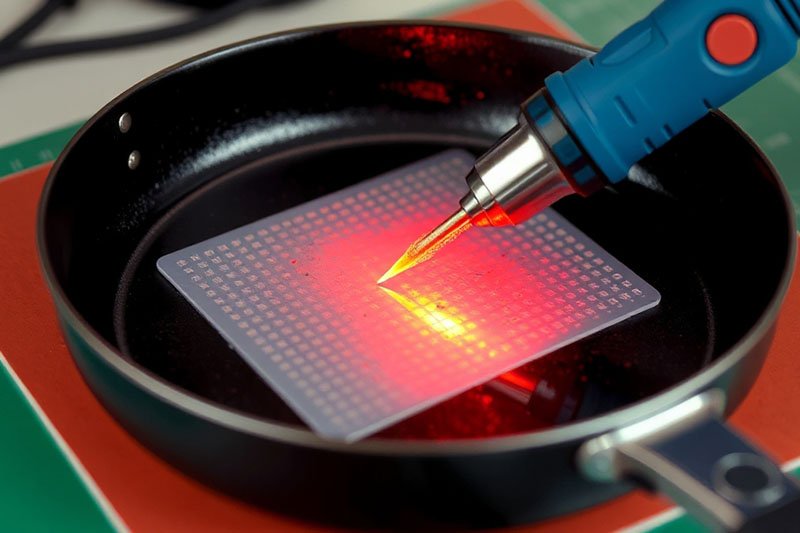
Heat-Related Challenges in Electronics Production
Electronics production involves processes like soldering, reflow ovens, and hot-air soldering stations, each generating considerable heat. High heat exposure can lead to:
- Component failure due to overheating
- Damage to production tables and benches
- Increased safety risks for operators, including burns
The following table summarizes common heat risks and how silicone mats can address them:
Risk | Impact | Silicone Mats’ Solution |
---|---|---|
Overheated components | Shortened product lifespan | Heat dissipation, thermal protection |
Surface burns/damage | Equipment deterioration, replacement | Durable protection, prevents damage |
Operator safety | Workplace injuries | Insulates heat, safer working area |
Why Silicone is Superior to Other Materials
Other materials like rubber or vinyl degrade under extreme heat conditions. Silicone, however, remains stable and resilient. Here’s why silicone stands out:
- Thermal Stability: Does not degrade or lose shape even at high temperatures.
- Non-reactive Material: Chemically inert, preventing contamination and chemical reactions.
- Long Lifespan: Durable and maintains integrity for extended periods, even in challenging industrial environments.
At RuiYang Silicone, we’ve helped several electronics manufacturers enhance their processes by implementing heat-resistant silicone mats. The feedback is always positive—improved safety, longer equipment life, and fewer production interruptions.
What Customizations Can Be Done on Silicone Mats for Electronics?
Every electronics manufacturer has unique needs, whether it’s precise dimensions, special textures, or specific conductivity requirements. Can silicone mats be tailored to fit these specialized demands?
Silicone mats offer extensive customization possibilities, including size, thickness, conductivity levels, surface textures, and even branding. This flexibility allows manufacturers to enhance their workspace efficiency, meet compliance standards, and boost their branding and identity.
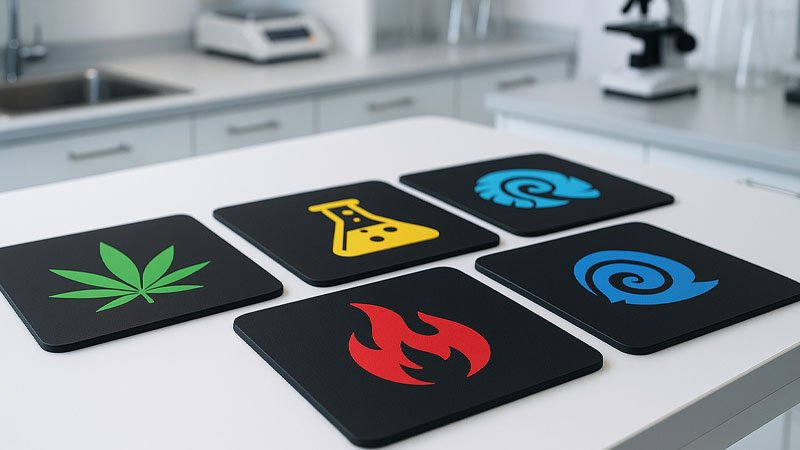
Popular Customization Options for Silicone Mats
Manufacturers often require silicone mats tailored to specific uses. Below are popular customizations we’ve frequently implemented:
Customization Option | Description | Application |
---|---|---|
Dimensions | Custom length, width, thickness | Workspace fitting, specific tool placement |
Conductivity Levels | Different levels of static dissipation | Specific ESD-sensitive electronics |
Surface Texture | Smooth, textured, ribbed | Enhancing grip, easy cleaning |
Branding & Colors | Custom logo, branding, specific color schemes | Company identity, organized workspace |
Benefits of Customizing Silicone Mats
Customized silicone mats not only enhance production but also positively impact branding, safety, and efficiency. Here’s how:
- Improved Workspace Organization: Mats can include specific markings to organize parts, tools, and work processes.
- Brand Visibility: Logos and customized colors reinforce brand identity internally and externally.
- Optimized Safety and Compliance: Tailored conductivity and heat resistance levels ensure adherence to strict safety regulations.
I’ve seen companies drastically improve efficiency by customizing silicone mats to match their workflow precisely. The initial investment in customization quickly pays off by reducing operational downtime and minimizing workplace errors.
Conclusion
Silicone mats significantly enhance electronics manufacturing through effective heat management, reliable ESD protection, and flexible customization, improving quality, safety, and productivity across the industry.