Silicone strips are highly prized across various sectors for their exceptional chemical resistance. Made from silicone rubber, these strips resist a wide range of chemicals, oils, and solvents, making them essential in many fields from industry to medicine. Their unique Si–O bond structure provides flexibility, durability, and stability in extreme conditions. Different silicone strips cater to specific needs: medical-grade strips for scar treatment and devices, industrial-grade for automotive and aerospace, and High Consistency Rubber (HCR) and Liquid Silicone Rubber (LSR) strips for high durability and precision.
Silicone strips resist many substances, including water, acids, bases, and solvents, although their resistance varies. They perform well in outdoor applications due to their water and weather resistance, though they struggle with hydrofluoric acid and high concentrations of strong acids. Despite being gas-permeable and costlier than natural rubber, advances in silicone recycling and material innovations enhance their sustainability and relevance.
Silicone Composition and Structure
Silicones have unique properties due to the Si–O bond, which is longer and has a wider bond angle than its carbon counterparts. This structure allows silicone chains to be highly flexible, maintaining their properties over a wide temperature range. Polysiloxane chains’ flexibility results from these longer bonds and wider angles. Polymers are often created without additives to avoid contamination, with methods like using THF and Li+ producing narrow polydispersities. The Si–C bond in organosilicon compounds is longer than the C–C bond, indicating less steric demand. Historical developments like the synthesis of tetraethylsilane laid the groundwork for important silicone polymers. Silica’s various forms and polymerization methods contribute to silicone’s superior chemical resistance.
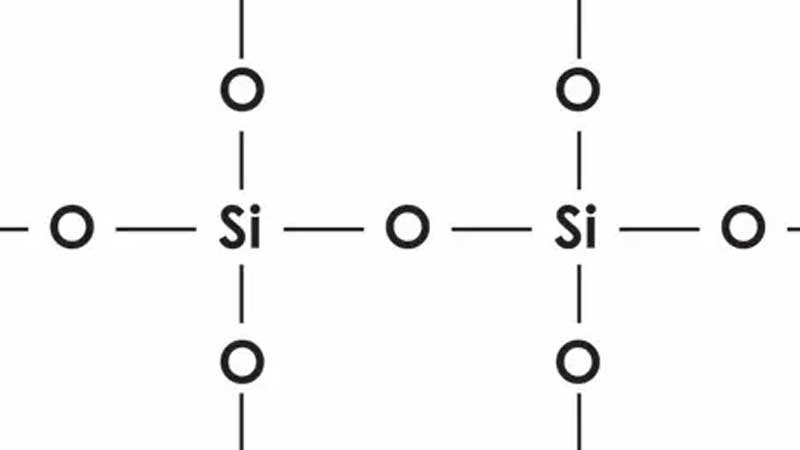
Silicone Strips Chemical Resistance Properties
Silicone rubber is renowned for its resistance to chemicals, oils, and solvents. Specific types like MF775 flame retardant silicone rubber, electrically conductive silicone rubber, and FDA-approved grades offer excellent resistance.
Water Resistance
Silicone sponge and HT800 rubber resist water well due to their closed-cell structure, making them suitable for outdoor and marine uses.
Resistance to Weathering
Silicone’s resistance to weathering, including oxygen, ozone, and UV light, is due to its strong silicon-oxygen bonds. Specialty silicones like fluorosilicone offer enhanced resistance for extreme conditions.
Acids and Bases
Silicone resists several acids and bases effectively, including acetic and citric acids. However, it has limited resistance to hydrofluoric, nitric, sulfuric, and hydrochloric acids. It performs well with phosphoric acid and is compatible with various salts, though its resistance to acetic anhydride and acetyl chloride is fair.
Solvents
Silicone’s compatibility with solvents varies. It works well with butyl alcohol and carbitol and shows conditional resistance to butanol and acetone. However, it is not compatible with chloroform.
Testing and Validation
Testing silicone’s chemical resistance involves checking its interaction with various chemicals. Silicone generally shows good compatibility with acetic acid, aluminum sulfate, and several alcohols but is less resistant to concentrated ammonium hydroxide, chloroform, aromatic hydrocarbons, hydrofluoric acid, and acetone.
Polar and Non-Polar Compounds
Silicone rubber does not significantly swell in polar compounds like alcohols but does swell in non-polar compounds like gasoline, due to molecular interactions.
Thermal and Environmental Properties
Silicone remains stable across temperatures from -50°C to 250°C, essential for consistent performance in extreme conditions.
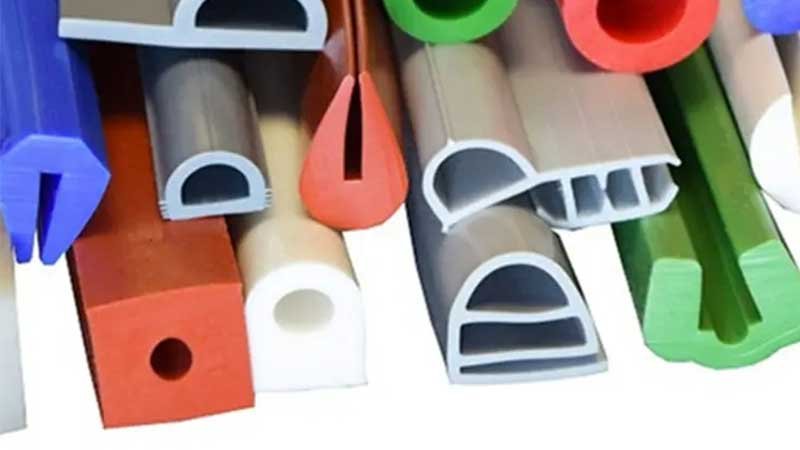
Factors Affecting Silicone Strips Chemical Resistance
The chemical resistance of silicone rubber depends on factors like the silicone type, with grades like MF775 and FDA-approved versions offering superior resistance. Specific chemical compatibility varies, with silicone showing strong resistance to various chemicals but weaker resistance to some acids and solvents. Physical properties like flexibility and tear resistance, combined with exposure conditions, also impact chemical resistance. Silicone’s environmental resistance is due to its silicon-oxygen bonds, making it suitable for outdoor and marine uses.
Silicone Strips Applications
Silicone strips are used widely for their chemical resistance and flexibility.
In industry, they handle oil exposure, though resistance varies by formulation.
In construction, they serve as gaskets and sealants, with a focus on recyclability.
In medicine, silicone strips help in scar treatment and skin care, and in high-voltage electrical insulation, they provide durability.
The choice of silicone product depends on application needs, with additives enhancing performance.
Silicone Strips Comparison with Other Materials
Natural Rubber
Advantages: Excellent elasticity, abrasion resistance, and biodegradability.
Limitations: Susceptible to chemical degradation, limiting use in harsh environments.
Fluorosilicone
Offers superior resistance to fuels, oils, and chemicals, and high-temperature stability. However, it is more expensive than standard silicone.
Mechanical Differences
Silicone rubber can be customized for scratch resistance and electrical properties, whereas natural rubber relies on inherent physical properties.
Silicone Rubber
Advantages: Excellent temperature resistance, chemical inertness, weatherability, sealing performance, and electrical properties.
Disadvantages: Higher gas permeability and cost compared to natural rubber.
Silicone Strips Testing and Standards
Testing silicone strips involves verifying chemical compatibility and evaluating material properties like tensile strength and hardness. Regulatory bodies like the FDA and EPA set safety standards for silicone products. Extract testing assesses materials in contact with fluids, with results influenced by various factors. Regulatory compliance is crucial for managing environmental impacts, particularly with hazardous waste.
Silicone Strips Maintenance and Care
Regular inspections for degradation signs, such as cracks and discoloration, are essential for extending silicone rubber components’ lifespan. Proactive replacement strategies can prevent unexpected failures. Proper cleaning with hot water and soap and avoiding oil-based soaps are crucial for maintaining silicone components. For sensitive applications, follow specific sterilization guidelines, avoiding ethylene oxide (ETO) due to incomplete outgassing data.
Future Developments
The future of silicone recycling looks promising, with planned state-of-the-art recycling plants and advancements in technology. Digital platforms and AI will enhance recycling efficiency, and regulatory changes will support these developments. Service-based business models and new silicone materials with properties like biodegradability will meet evolving environmental needs.