Silicone printing can be challenging. Many businesses face issues like ink smudging, uneven curing, and color fading. These problems can lead to unsatisfactory results and wasted materials. Identifying the root cause is essential for ensuring high-quality prints.
To effectively troubleshoot silicone printing issues, consider factors such as ink quality, curing conditions, and substrate preparation. Addressing these aspects can help improve the final product and reduce defects.
Let’s explore these common issues in more detail.
Why Does Ink Smudge During Silicone Printing
Ink smudging is a frequent problem in silicone printing. It occurs when the ink does not adhere properly to the silicone surface or when it is disturbed before it dries completely. This can result in blurred or smeared prints, which are not only unsightly but also compromise the durability of the print.
Causes of Ink Smudging
- Dirty Surface: Silicone surfaces must be clean and free of contaminants. Any dust, oil, or residue can prevent the ink from adhering properly.
- Incorrect Ink Formulation: Not all inks are suitable for silicone printing. Using the wrong type of ink can lead to poor adhesion and smudging.
- Insufficient Drying Time: Rushing the drying process can cause the ink to smudge. Proper curing time is essential for the ink to set.
How to Fix Ink Smudging
- Clean the Surface: Ensure the silicone surface is thoroughly cleaned using isopropyl alcohol or a similar cleaning agent. This removes any contaminants that might interfere with ink adhesion.
- Use Silicone-Compatible Inks: Select inks specifically formulated for silicone printing. These inks have better adhesion properties and are less likely to smudge.
- Allow Adequate Drying Time: Follow the manufacturer’s recommendations for drying and curing times. Using a drying rack or a controlled environment can help achieve consistent results.
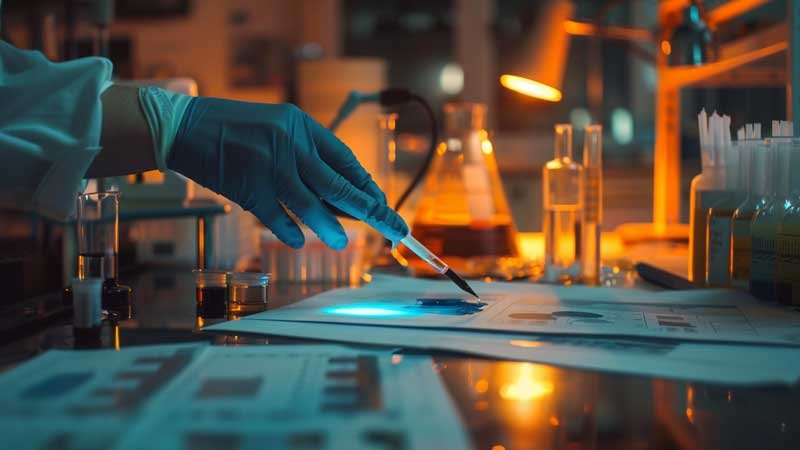
How Can You Achieve Even Curing in Silicone Printing
Uneven curing is another common issue that can affect the quality of silicone prints. It occurs when the ink does not cure uniformly, leading to areas that are either over-cured or under-cured. This can result in prints that are either too brittle or too soft.
Causes of Uneven Curing
- Inconsistent Heat Distribution: Uneven heat application during the curing process can lead to inconsistent results.
- Incorrect Curing Temperature: Using the wrong temperature can prevent the ink from curing properly.
- Variations in Ink Thickness: Applying ink unevenly can cause some areas to cure faster than others.
Solutions for Uneven Curing
- Ensure Even Heat Distribution: Use a convection oven or a heat press with even heat distribution. This ensures that the entire print area receives consistent heat.
- Set the Correct Temperature: Follow the ink manufacturer’s guidelines for the correct curing temperature. Using a temperature controller can help maintain the desired temperature throughout the process.
- Apply Ink Evenly: Use a consistent method for applying ink to the silicone surface. A screen printing technique can help achieve uniform ink thickness.
Why Does Color Fade in Silicone Prints
Color fading is a significant issue in silicone printing, especially for products exposed to sunlight or harsh environmental conditions. Fading can make the prints look dull and reduce their visual appeal.
Causes of Color Fading
- UV Exposure: Prolonged exposure to ultraviolet (UV) light can cause the colors to fade over time.
- Poor-Quality Inks: Using low-quality inks that are not UV-resistant can lead to faster fading.
- Inadequate Curing: Improperly cured inks are more susceptible to fading and wear.
How to Prevent Color Fading
- Use UV-Resistant Inks: Select inks that are specifically designed to resist UV light. These inks contain additives that protect the colors from fading.
- Apply a UV Coating: Adding a UV-protective coating over the print can provide an additional layer of protection against fading.
- Ensure Proper Curing: Follow the recommended curing process to ensure the ink is fully set. This enhances the durability and longevity of the print.
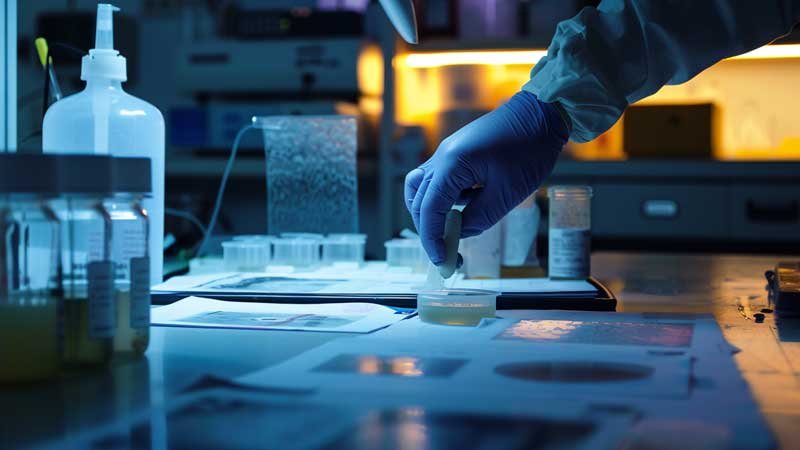
How to Maintain Consistent Quality in Silicone Printing
Maintaining consistent quality in silicone printing requires a combination of good practices and regular maintenance. Here are some tips to help you achieve reliable results:
Regular Equipment Maintenance
- Clean Printing Screens: Regularly clean the screens to remove any ink buildup or debris. This ensures a smooth and consistent ink flow.
- Check Heat Presses and Ovens: Ensure that your heat presses and ovens are functioning correctly and providing even heat distribution.
- Calibrate Equipment: Regularly calibrate your equipment to ensure accurate temperature and pressure settings.
Use High-Quality Materials
- Select the Right Inks: Choose inks that are compatible with silicone and designed for durability.
- Use High-Quality Silicone: Ensure that the silicone surfaces you are printing on are of high quality and free from defects.
Follow Best Practices
- Test Prints: Always perform test prints before starting a large batch. This helps identify any issues early and allows for adjustments.
- Monitor Environmental Conditions: Maintain a controlled environment with stable temperature and humidity levels. Extreme conditions can affect the curing process and print quality.
- Document Processes: Keep detailed records of your printing processes, including ink types, curing times, and temperatures. This helps in troubleshooting and maintaining consistency.
What Role Do Environmental Factors Play in Silicone Printing
Environmental conditions significantly influence the silicone printing process. Factors like humidity, temperature, and air quality can affect ink performance.
Managing Environmental Factors
- Control Humidity Levels: Keep humidity within the optimal range to prevent ink issues.
- Monitor Room Temperature: Ensure the printing area maintains a consistent temperature for better results.
- Ventilate Printing Space: Adequate ventilation can help prevent the buildup of harmful fumes from inks and solvents.
How Can You Improve Adhesion in Silicone Printing
Adhesion problems can lead to significant challenges in silicone printing. Understanding the factors that influence adhesion is critical.
Tips for Improving Adhesion
- Use Primer: Applying a primer can enhance adhesion on silicone surfaces.
- Adjust Printing Speed: Slower printing speeds may improve ink transfer and adhesion.
- Test Different Inks: Experiment with various inks to find the best match for your materials.
Conclusion
Silicone printing can be challenging, but with the right approach, you can overcome common issues like ink smudging, uneven curing, and color fading. By understanding the causes and implementing effective solutions, you can achieve high-quality and durable prints on silicone surfaces. Regular maintenance, using high-quality materials, and following best practices are key to maintaining consistent results in silicone printing.