Silicone, the wonder material that has revolutionized various industries, is not just limited to baking mats and phone cases. Its versatility and unique properties make it an ideal choice for manufacturing a wide range of parts used in countless applications. From automotive components to medical devices, silicone parts play a crucial role in modern technology and everyday life. In this article, we will explore the world of silicone parts, their manufacturing process, and their significance in different industries.
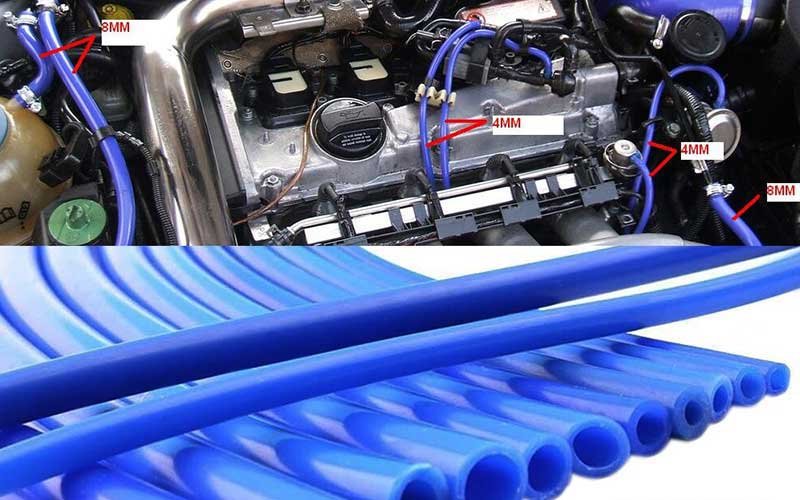
The Journey of Silicone Parts
Imagine you’re driving your car, appreciating its smooth ride and comfortable interior. Little do you realize that silicone parts are silently working behind the scenes, ensuring optimal performance and safety. From gaskets and seals to hoses and connectors, silicone components are an integral part of the automotive industry.
Silicone’s excellent temperature resistance, flexibility, and durability make it an ideal choice for withstanding the harsh conditions within an engine. It can handle extreme temperatures, resist oil and fuel, and maintain its integrity over a long period. This allows silicone gaskets and seals to provide a reliable barrier, preventing leaks and ensuring the engine operates smoothly.
Silicone hoses, another essential component in the automotive industry, are known for their resilience and ability to withstand high-pressure systems. They efficiently transfer fluids and gases in engines, providing a vital link in the complex network of automotive systems. These hoses not only endure extreme temperatures but also remain flexible, making installation and maintenance easier.
From Concept to Creation: The Silicone Parts Manufacturing Process
To fully appreciate the versatility of silicone parts, it’s important to understand the meticulous process involved in their creation.
Designing for Success
It all starts with the design phase. Skilled engineers work closely with clients to understand their specific requirements and design silicone parts tailored to their needs. This collaborative approach ensures that the final product not only meets the desired functionality but also fits seamlessly into the intended application.
Molding the Future
Once the design is finalized, the manufacturing process moves into the molding stage. Silicone parts can be produced through various molding methods, such as compression molding, transfer molding, and injection molding. Each technique offers its own advantages in terms of production speed, complexity of design, and cost-effectiveness.
For instance, injection molding is often preferred for large-scale production as it allows for high-volume manufacturing with consistent quality. On the other hand, compression molding is suitable for smaller production runs or parts with intricate designs.
Bringing It to Life
After the molding process, the silicone parts undergo a curing process to solidify the material and ensure its durability. This typically involves subjecting the molded parts to heat, pressure, and time, allowing the silicone to crosslink and achieve its final form. The curing process is critical to enhancing the mechanical properties of the silicone, making it robust and long-lasting.
Quality Is Paramount
Quality control is of utmost importance in silicone parts manufacturing. Reputable manufacturers, such as RY Silicone, implement rigorous quality management systems to ensure that every product meets or exceeds industry standards. Thorough inspections, testing, and certifications guarantee that the silicone parts possess the desired characteristics and are free from defects.
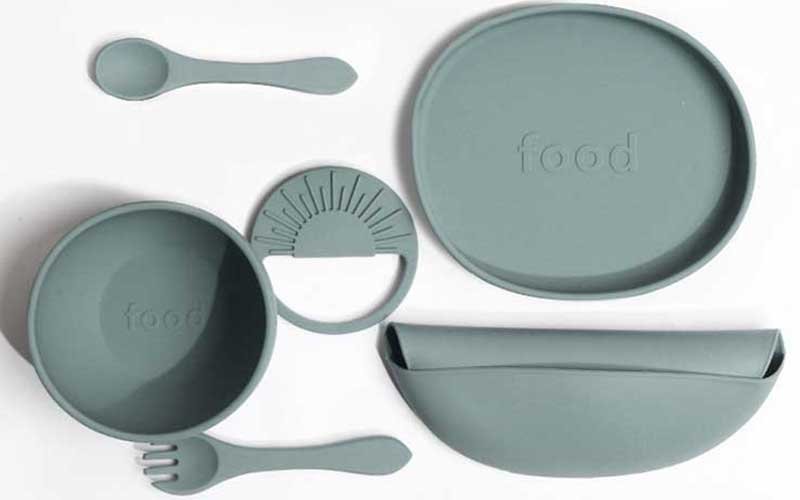
Everyday Applications: Silicone Parts in Action
Now that we understand the manufacturing process, let’s explore some real-life applications where silicone parts play a pivotal role.
In the Kitchen: Silicone Utensils and Bakeware
Have you ever used a silicone spatula or baking mat while cooking? These kitchen essentials owe their popularity to the numerous advantages of silicone. Silicone utensils are heat-resistant, ensuring that they won’t melt or warp even when exposed to high temperatures. Additionally, their non-stick properties make them a breeze to clean.
Medical Marvels: Silicone Components in Healthcare
Silicone’s biocompatibility and hypoallergenic properties make it invaluable in the medical field. From prosthetic devices to catheters and implants, silicone parts are extensively used to ensure patient comfort, durability, and compatibility with bodily tissues. Their flexibility allows for comfortable movement, while their non-reactive nature minimizes the risk of adverse reactions.
Automotive Advancements: Silicone Hoses and Seals
The automotive industry relies on silicone parts to enhance performance and reliability. Silicone hoses, seals, and gaskets provide excellent resistance to heat, chemicals, and pressure, making them indispensable in engines, cooling systems, and other critical automotive applications. Their ability to maintain their integrity under extreme conditions ensures the smooth operation of vehicles.
Technological Triumphs: Silicone Keypads and Electronic Components
Silicone parts also find their way into the world of technology. Silicone keypads are commonly used in consumer electronics and industrial equipment, providing tactile feedback and durability. Silicone’s electrical insulation properties make it ideal for manufacturing electronic components such as connectors, seals, and insulators, ensuring reliable performance even in demanding environments.

The Role of Silicone Parts Manufacturers
Now that we have explored the fascinating world of silicone parts, let’s shift our focus to the dedicated individuals and companies responsible for bringing these creations to life. Silicone parts manufacturers, like RY Silicone, are the driving force behind the innovation and production of silicone-based components.
Silicone parts manufacturers employ state-of-the-art facilities and cutting-edge technology to produce high-quality products. With a commitment to precision and quality, they ensure that each component meets stringent industry standards and customer requirements. From initial design and prototyping to final production and quality control, these manufacturers meticulously oversee every step of the process.
Moreover, reputable silicone parts manufacturers prioritize customer satisfaction and offer comprehensive services. They understand the importance of collaboration and work closely with clients to develop custom solutions tailored to their specific needs. Whether it’s an intricate silicone bead for jewelry or a complex silicone keypad for an industrial machine, these manufacturers rise to the challenge and deliver excellence.
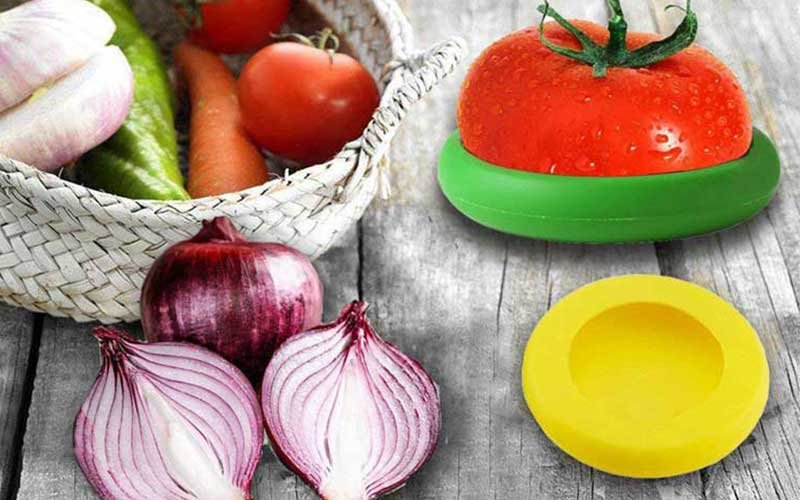
Quality Management and After-Sales Service
Quality is of paramount importance in the world of silicone parts, and reliable manufacturers prioritize it throughout the manufacturing process. After-sales service is another crucial aspect offered by reputable silicone parts manufacturers. They stand behind their products, providing support, addressing any concerns, and offering solutions in case of unexpected issues. This commitment to customer satisfaction sets them apart and fosters long-lasting partnerships with their clients.
The Future of Silicone Parts
As technology advances and new applications emerge, the future of silicone parts looks promising. With continuous innovation in materials and manufacturing techniques, we can expect even more versatile and efficient silicone components in the years to come.
Silicone parts will continue to push the boundaries of what’s possible in various industries. From automotive advancements to medical breakthroughs, consumer electronics to household essentials, the impact of silicone parts will be felt far and wide.
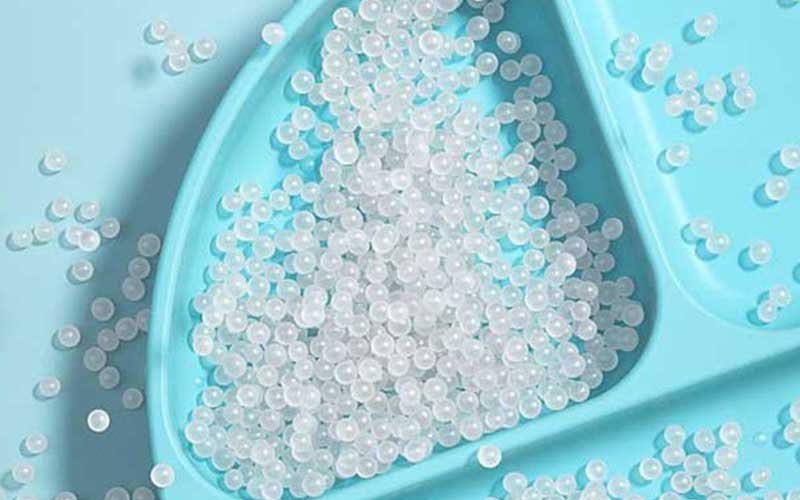
Conclusion
Silicone parts have revolutionized various industries, from automotive and healthcare to electronics and consumer goods. Their unique properties, such as temperature resistance, flexibility, and biocompatibility, make them indispensable components in modern technology and everyday products.
Whether it’s ensuring a leak-free engine, facilitating complex medical procedures, or enhancing user experience in electronic devices, silicone parts play a crucial role. The manufacturing process of silicone parts, through silicone injection molding, allows for the production of customized parts with precision and efficiency.
If you’re in need of high-quality silicone parts, it’s essential to partner with a reputable silicone parts manufacturer like RY Silicone (website: Silicone parts manufacturer). With their expertise in silicone manufacturing (website: Silicone Manufacturing), quality management, warehousing, logistics, and after-sales service, RY Silicone offers a comprehensive solution for your silicone part needs.
Silicone parts continue to shape our world, enabling innovation, safety, and convenience. Their journey from raw material to indispensable components showcases the incredible potential of silicone and its lasting impact on various industries.
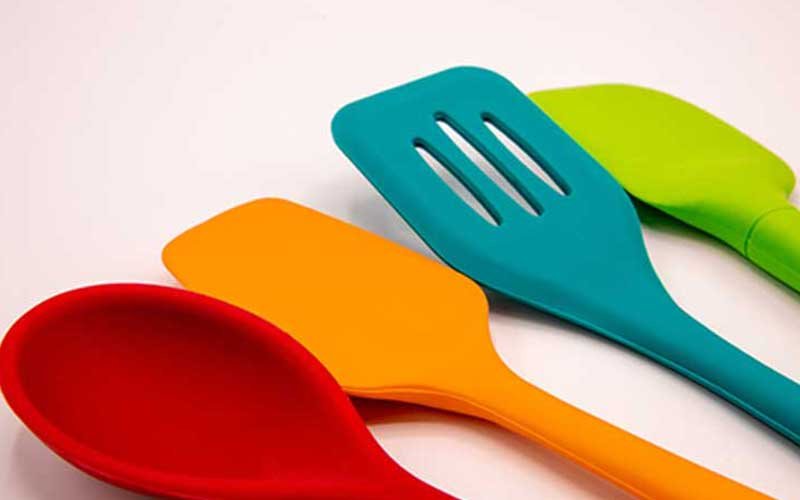
Frequently Asked Questions
Q: What are the 4 types of silicone?
A: Silicone materials can be classified into four main types: high-consistency rubber (HCR), liquid silicone rubber (LSR), room temperature vulcanizing (RTV) silicone, and fluorosilicone. Each type has its own unique properties and applications.
Q: What is silicone made out of?
A: Silicone is a synthetic material made from silicon, oxygen, carbon, and hydrogen. It is created through a chemical process that involves combining silicon dioxide (silica) with various other compounds to form silicone polymers.
Q: What is part A and B in silicone rubber?
A: In silicone rubber, part A and part B refer to the two components of a two-part silicone system. Part A typically contains the base polymer and some additives, while part B consists of a crosslinking agent or catalyst. When part A and part B are mixed together, a chemical reaction occurs, leading to the curing or solidification of the silicone rubber.
Q: Is silicone safer than Teflon?
A: Silicone is generally considered to be a safer option than Teflon (polytetrafluoroethylene) when it comes to cooking utensils and bakeware. Unlike Teflon, silicone does not release potentially harmful chemicals or gases when exposed to high temperatures. Silicone is also non-reactive and non-toxic, making it a popular choice for food-contact applications.
Q: Can bacteria live in silicone?
A: Silicone is a non-porous material, which means that it does not provide a suitable environment for bacteria to thrive. Its smooth and impermeable surface makes it resistant to microbial growth. However, it is still important to clean and maintain silicone products properly to prevent the buildup of dirt or residue.
Q: What happens if silicone gets wet before it cures?
A: If silicone gets wet before it fully cures, it may affect the curing process and the final properties of the silicone. Water or moisture can interfere with the crosslinking reaction, potentially leading to incomplete curing, reduced strength, or a tacky surface. It is best to ensure that the silicone remains dry during the curing period for optimal results.
Q: What does RTV mean in silicone?
A: RTV stands for “room temperature vulcanizing.” RTV silicone is a type of silicone rubber that cures at room temperature without the need for heat or pressure. It typically comes in a paste or liquid form and can be applied to various surfaces to create flexible and durable seals, gaskets, or coatings.
Q: Does silicone leach toxins?
A: Silicone is generally considered to be a safe and non-toxic material. It does not leach harmful chemicals or toxins under normal conditions. Silicone is widely used in medical and food-grade applications due to its inert nature and high biocompatibility.
Q: Does silicone break down in the body?
A: Silicone is considered biocompatible and is commonly used in medical implants and devices. While the body does not break down silicone, long-term implantation may result in a thin layer of scar tissue forming around the silicone implant, a natural response of the body’s immune system. It is essential to consult with a medical professional for specific information on silicone implants and their interactions with the body.