Silicone compression molding is a widely used manufacturing process across various industries. Despite its popularity, many are still unsure of its advantages and applications, which can prevent businesses from leveraging this effective production method.
This process involves placing silicone material into a heated mold, applying pressure to shape it. It’s efficient and produces durable products, making it ideal for high-volume production.
Let’s explore its mechanics and applications further.
What is Silicone Compression Molding?
Silicone compression molding is a common manufacturing method that transforms uncured silicone rubber into strong, high-quality products. This technique uses heat and pressure to mold silicone into different shapes and sizes, making it especially valuable in industries that require materials with excellent thermal stability, durability, and flexibility.
How Does Silicone Compression Molding Work?
The silicone compression molding process involves several critical stages to ensure efficient production of high-quality silicone parts. Here’s a step-by-step overview:
1. Material Selection and Preparation
The process begins with selecting the appropriate silicone rubber compound based on its properties and intended use. The uncured silicone is then weighed and pre-formed to fit into the mold cavity.
2. Mold Design and Heating
Molds, typically made of hardened steel or aluminum, are preheated to a specific temperature suited for the silicone compound, generally between 160°C and 185°C. This heating keeps the silicone pliable, allowing it to flow into the mold’s contours without curing prematurely.
3. Compression and Curing
Once the pre-formed silicone is placed in the mold, it is closed, and significant pressure—usually between 1,000 to 4,000 psi—is applied. This pressure ensures the rubber flows evenly into the mold. As the temperature rises, curing agents in the silicone activate, starting the vulcanization process, which gives the material its final strength and stability.
4. Cooling and Demolding
After curing, the mold cools, and the finished product is removed. This step ensures that the silicone part maintains its shape and properties.
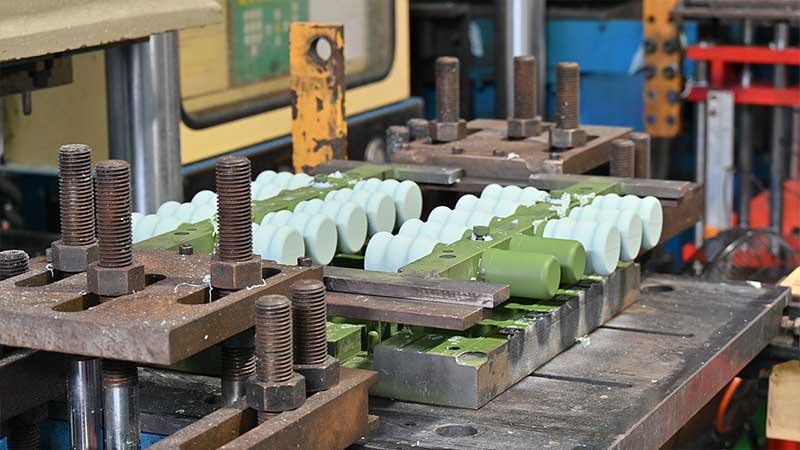
Benefits of Silicone Compression Molding
Silicone compression molding offers several key advantages:
Cost-Effective
This method is ideal for mass production, leading to lower operational costs compared to other molding techniques. It is particularly beneficial for small to medium-sized manufacturing operations.
Versatility
Silicone compression molding can produce a wide variety of shapes and sizes, making it suitable for numerous applications across different industries.
Durability
Silicone’s resistance to extreme temperatures ensures its effectiveness in demanding environments, making it a reliable choice for various products.
Eco-Friendly
The process often utilizes sustainable materials and generates less waste compared to traditional molding methods, making it an environmentally conscious option.
Applications of Silicone Compression Molding
Silicone compression molding is widely employed across various industries due to its versatility and the unique properties of silicone rubber. Common applications include:
Automotive Industry
Silicone compression molding is used to manufacture components such as hoses, gaskets, seals, and other parts that must endure harsh conditions and provide reliable performance.
Medical Devices
Valued for its biocompatibility and flexibility, silicone is commonly used in medical products like tubing, valves, and surgical tools, ensuring safety and effectiveness.
Consumer Goods
This method is prevalent in the production of kitchen utensils, appliance housings, and other everyday items, taking advantage of silicone’s durability and ease of use.
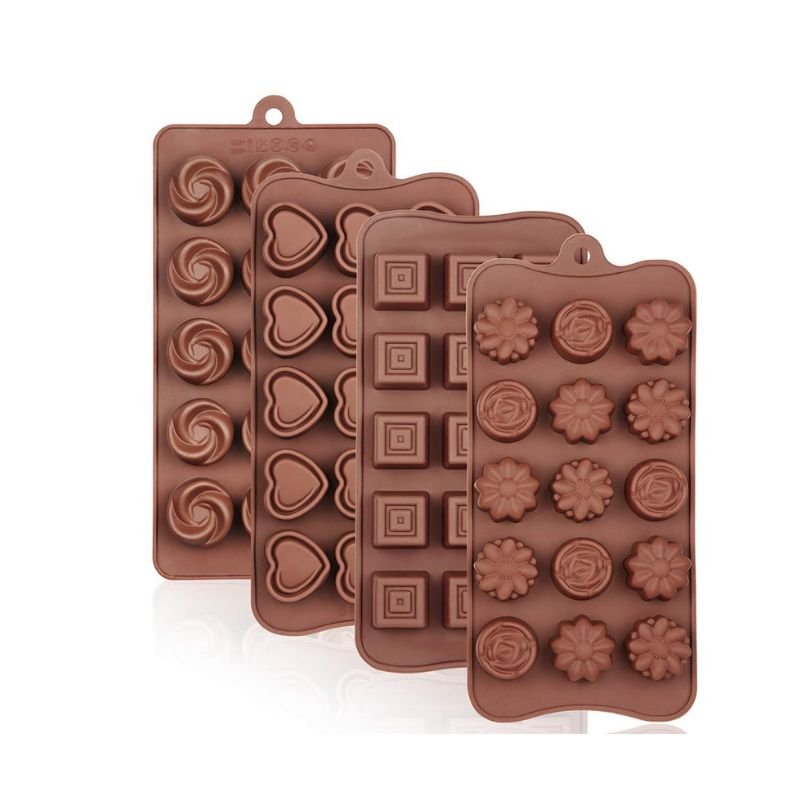
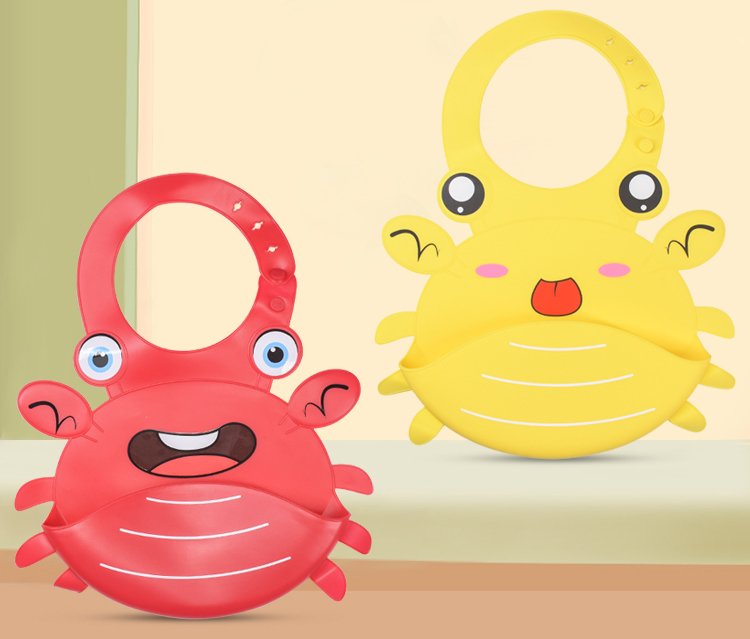
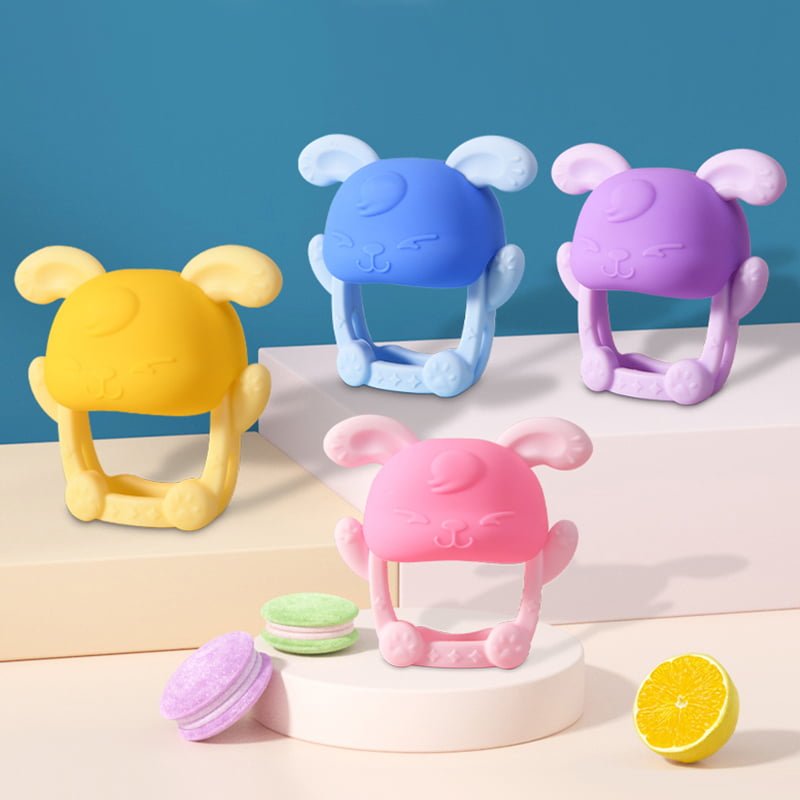
Aerospace Industry
Silicone compression molding is utilized to create lightweight, high-strength components such as interior panels and structural parts, crucial for aircraft performance.
Electrical and Electronics Industry
It is also used for producing insulators, switchgear, and other components that require precision and reliability, ensuring optimal functionality in electronic devices.
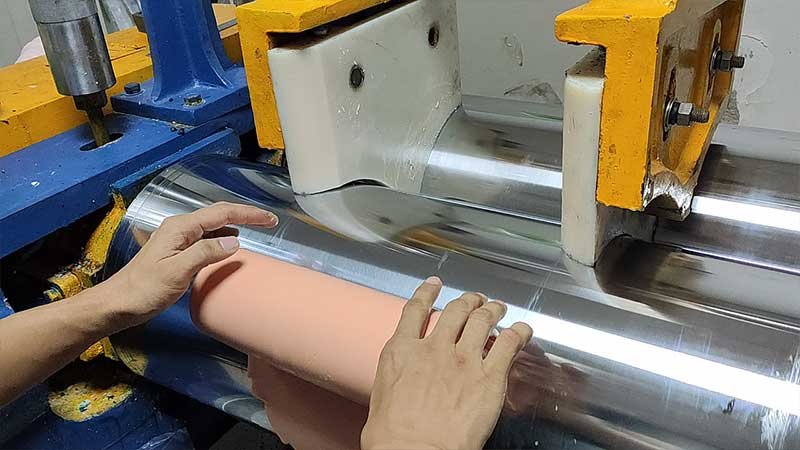
Comparison with Other Molding Processes
Silicone compression molding stands out when compared to other manufacturing methods. Here’s a comparison:
Feature | Silicone Compression Molding | Injection Molding | Blow Molding |
---|---|---|---|
Setup Complexity | Simple | Complex | Moderate |
Cost | Less expensive | Higher initial costs | Moderate |
Waste Generation | Low | Moderate | Low |
Production Speed | Slower for some applications | Faster | Fast |
Material Versatility | High | Moderate | Limited |
Choosing a Silicone Compression Molding Supplier
When selecting a supplier for silicone compression molding, consider the following key qualities:
1. Experience
Choose a supplier with a solid track record in silicone compression molding. Their experience can significantly impact the quality of your products.
2. Quality Control
Ensure the supplier has strict quality control measures in place. This guarantees that the products meet industry standards and specifications.
3. Customization Options
Look for suppliers that offer tailored solutions to meet your specific needs. Customization can enhance the functionality of the final products.
4. Customer Support
Good communication is vital. A supplier that provides strong customer support can help resolve issues quickly and ensure a smooth production process.
Contact rysilicone for your customized silicone products now.
Limitations of Silicone Compression Molding
While silicone compression molding offers numerous advantages, it also has some limitations:
Production Speed
This method may be slower than other molding techniques for certain applications, which can impact overall efficiency, especially in high-demand scenarios.
Initial Setup Cost
The creation of molds can involve significant initial costs. This investment may be a consideration for smaller projects or companies with limited budgets.
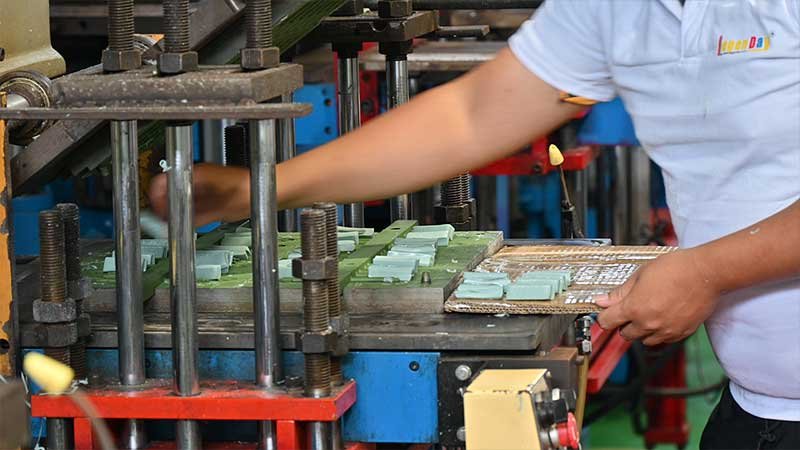
Optimizing Silicone Compression Molding Production
To enhance efficiency in silicone compression molding production, consider the following tips:
1. Mold Design
Design molds with easy demolding in mind. This can reduce production time and improve the overall quality of the finished products.
2. Material Quality
Using high-quality silicone is crucial for achieving better results. Quality materials lead to stronger and more reliable products.
3. Temperature Control
Maintain a consistent temperature throughout the molding process. This helps ensure uniform curing and optimal performance of the silicone parts.
4. Training
Ensure that operators are well-trained in the silicone compression molding process. Proper training can significantly enhance production efficiency and product quality.
Innovations in Silicone Compression Molding
The silicone compression molding industry is evolving with new technologies and innovations, including:
3D Printing
This technology allows for faster mold production, reducing lead times and enabling rapid prototyping of new designs.
Smart Sensors
Smart sensors can monitor the molding process in real-time, providing valuable data that helps optimize production and ensure consistent quality.
Sustainable Materials
There is ongoing development of more eco-friendly silicone options, which enhances the environmental benefits of the molding process and meets growing consumer demand for sustainable products.
Conclusion
Silicone compression molding is an efficient and versatile manufacturing process with numerous applications across various industries. Understanding its workings and benefits is essential for industries looking to optimize production and leverage the unique properties of silicone rubber.