Choosing the wrong silicone mat thickness or hardness can ruin your entire project. I’ve seen countless manufacturers waste thousands of dollars on unsuitable materials.
The ideal silicone mat thickness ranges from 0.5mm to 25mm, while durometer typically falls between 10A to 80A Shore hardness. Your specific application requirements determine the perfect combination of these two critical properties.
After 12 years in the silicone manufacturing industry, I’ve helped hundreds of clients select the perfect specifications for their applications. Let me share the insights that will save you time and money.
What Thickness Range Works Best for Different Applications?
Most people think thicker always means better. This assumption costs them performance and money in many applications.
Silicone mat thickness should match your application’s compression, insulation, and durability needs. Thin mats (0.5-2mm) excel in gaskets, while thick mats (10-25mm) provide superior cushioning and insulation.
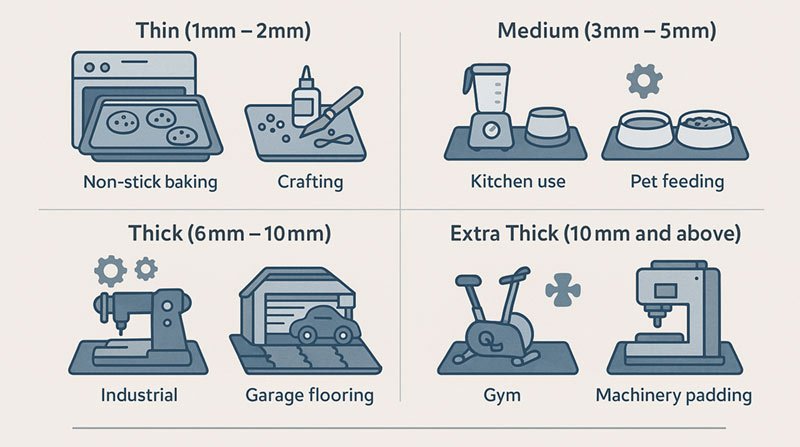
I remember working with a client who insisted on 10mm thick mats for their electronic gasket application. The thick material created poor sealing and increased costs by 300%. We switched to 1.5mm thickness and achieved perfect results.
The thickness selection depends on several key factors. For sealing applications, you need just enough material to fill gaps without over-compression. Electronic applications typically require 0.5mm to 3mm thickness for optimal performance.
Application Type | Recommended Thickness | Key Benefits |
---|---|---|
Gaskets & Seals | 0.5mm – 3mm | Precise fit, cost-effective |
Thermal Pads | 1mm – 5mm | Heat transfer, conformability |
Vibration Dampening | 5mm – 15mm | Shock absorption, noise reduction |
Insulation Mats | 10mm – 25mm | Thermal barrier, cushioning |
Food Grade Mats | 2mm – 8mm | Easy cleaning, durability |
Compression requirements also drive thickness selection. If your application compresses the mat by 25%, you need enough initial thickness to maintain sealing after compression. I always recommend calculating the final compressed thickness to ensure it meets your minimum requirements.
Manufacturing considerations affect thickness choice too. Thinner mats cure faster and cost less to produce. Thicker mats require longer cure times and more material. For high-volume production, thin mats often provide better economics without sacrificing performance.
How Does Durometer Affect Your Mat Performance?
Many engineers confuse durometer with quality. Higher durometer doesn’t always mean better performance for your specific needs.
Durometer measures silicone hardness on the Shore A scale from 10A (very soft) to 80A (firm rubber-like). Soft durometers (10A-30A) provide excellent sealing, while hard durometers (50A-80A) offer better wear resistance.
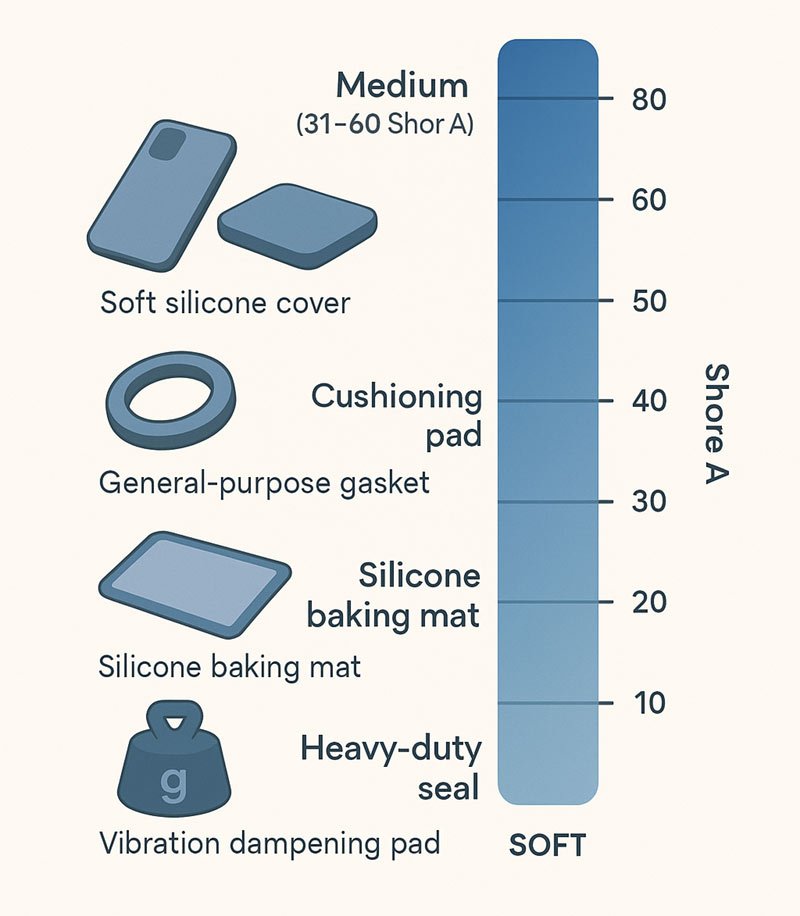
I learned this lesson early in my career when a food processing client needed mats for their conveyor system. They requested 70A durometer for “maximum durability.” The hard mats couldn’t conform to surface irregularities and failed within weeks. We switched to 40A durometer and achieved two years of reliable service.
Soft durometers excel in sealing applications because they conform to surface imperfections. The material flows into tiny gaps and creates effective barriers against liquids and gases. However, soft materials wear faster under abrasive conditions.
Durometer Selection Guidelines
Sealing Applications (10A-40A): Soft durometers work best when you need the material to flow and conform. Door seals, window gaskets, and pipe connections benefit from this flexibility. The material compresses easily and maintains contact pressure over time.
General Purpose Applications (30A-50A): This range provides the best balance of flexibility and durability for most applications. Food service mats, laboratory surfaces, and general industrial uses perform well in this durometer range.
High-Wear Applications (50A-80A): Hard durometers resist abrasion and maintain their shape under stress. Cutting mats, high-traffic walkways, and industrial equipment pads need this level of firmness.
The temperature affects durometer performance significantly. Silicone becomes softer at high temperatures and harder at low temperatures. I always consider the operating temperature range when selecting durometer specifications.
Chemical exposure also influences durometer choice. Some chemicals cause silicone to swell and soften over time. Others may harden the material. Your chemical compatibility requirements may override other durometer considerations.
What Factors Should Guide Your Selection Process?
Most specification decisions happen too quickly without considering all relevant factors. This rushed approach leads to expensive mistakes and project delays.
Your selection process should evaluate load requirements, environmental conditions, expected lifespan, manufacturing constraints, and cost targets. Each factor influences both thickness and durometer specifications.
I developed a systematic approach after seeing too many projects fail due to incomplete specification analysis. Start with your primary function requirement, then layer in the secondary considerations.
Load analysis comes first in my process. Calculate the static and dynamic loads your mat will experience. Static loads determine minimum thickness to prevent bottoming out. Dynamic loads affect fatigue resistance and require durometer considerations.
Environmental Factor Analysis
Temperature Cycling: Repeated heating and cooling stress the material differently than constant temperature exposure. Thicker mats handle thermal stress better due to lower thermal gradients. Softer durometers accommodate thermal expansion more effectively.
Chemical Exposure: Aggressive chemicals may require specific silicone formulations that limit your thickness and durometer options. I always request chemical compatibility data before finalizing specifications.
UV and Ozone Exposure: Outdoor applications need UV-stable formulations. These materials typically have slightly different mechanical properties than standard grades. The durometer may be limited to specific ranges for optimal weather resistance.
Cleaning Requirements: Food grade and medical applications need materials that withstand aggressive cleaning chemicals and high-temperature sanitizing. These requirements often dictate both minimum durometer for durability and maximum thickness for complete cleaning.
Manufacturing and Cost Considerations
Tooling costs increase significantly for very thin or very thick mats. Standard thickness ranges (1mm-10mm) use existing tooling and reduce setup costs. Custom thicknesses require new tooling and minimum order quantities.
Lead times vary by specification complexity. Standard combinations of thickness and durometer ship quickly from stock. Custom specifications need 2-4 weeks for production scheduling and quality testing.
Quality control becomes more challenging with extreme specifications. Very thin mats may have thickness variations that affect performance. Very soft durometers require special handling to prevent damage during shipping and installation.
Conclusion
Selecting the right thickness and durometer combination requires careful analysis of your specific application requirements, environmental conditions, and manufacturing constraints.