Are you struggling to find the right silicone printing ink for your business? Do you need a high-quality formulation that stands the test of time and offers customization flexibility? Many businesses face this challenge. The wrong choice could lead to fading designs, poor adhesion, or environmental issues. But with constant advancements in silicone technology, innovative solutions are emerging that can transform how you think about printing on silicone surfaces.
Now, let’s dive into the innovations and key aspects you need to know to stay competitive in the industry.
History of Silicone Printing Ink
The history of printing ink spans thousands of years, beginning in ancient civilizations like Egypt and China. Early inks were made from natural substances such as soot, charcoal, and plant extracts. The Egyptians used a blend of soot and gum to write on papyrus, while the Chinese developed ink from lampblack, glue, and water.
With the invention of the printing press in the 15th century, ink formulations changed dramatically. Oil-based inks were developed to adhere to metal and produce clear, readable prints, revolutionizing the industry. Johannes Gutenberg, who introduced the movable type printing press, initially used a mixture of lampblack and varnish for his inks.
During the Middle Ages, iron gall ink, made from tannins, iron salts, and gum arabic, became popular for its durability and resistance to fading, and it remained in use until the 20th century. As printing technology advanced, ink formulations continued to evolve. Modern inks are now complex chemical blends designed for specific uses on materials like paper, plastics, textiles, and metals, reflecting ongoing innovation in the industry.
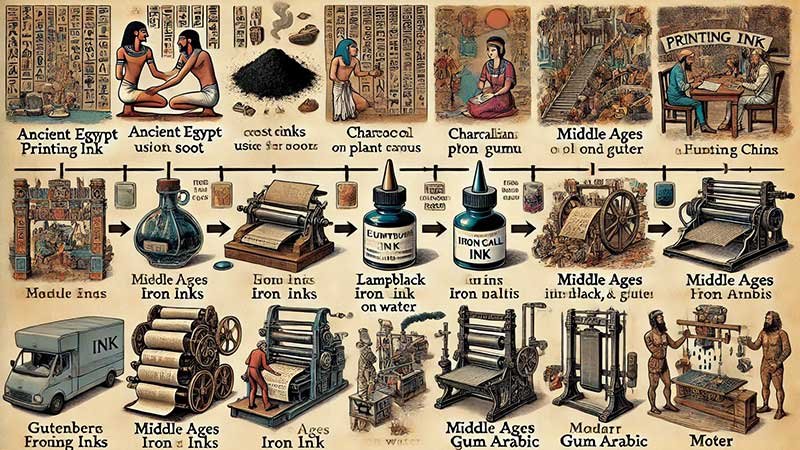
Why is silicone printing ink so essential?
Silicone is a notoriously difficult material to print on. Its non-stick surface and high thermal resistance make it challenging for traditional inks to adhere properly. This is why special silicone printing inks are formulated to work in these unique conditions.
These inks bond well with the silicone substrate, ensuring long-lasting prints that won’t crack, peel, or fade even under extreme conditions. Whether U’re working with silicone baby products, medical equipment, or kitchenware, having the right ink can make or break the quality of your final product.
Types of Silicone Printing Inks
Printing inks are categorized based on their composition, drying methods, and applications, each offering unique qualities suited to different printing techniques and surfaces.
Solvent-Based Inks
Solvent-based inks are known for their versatility and ability to adhere to various materials like metal, plastic, and paper. Their durability makes them ideal for industrial uses that require strong, long-lasting markings.
Water-Based Inks
Water-based inks, which use water as their main solvent, are a more environmentally friendly option, emitting fewer volatile organic compounds (VOCs). They are primarily used for printing on materials like corrugated and kraft boards, offering good adhesion and print quality.
Traditional Inks
Often called oil-based inks, traditional inks consist of pigments suspended in petroleum-based solvents or drying oils like linseed oil. These inks are widely used in offset lithography, letterpress, and flexographic printing, offering excellent color reproduction and adhesion to surfaces such as paper, cardboard, and plastics.
UV Inks
UV-curable inks are popular due to their low VOC emissions and fast curing process. When exposed to ultraviolet light, these inks harden almost instantly, eliminating the need for solvents and lengthy drying times, making them ideal for high-speed printing.
Digital Inks
Digital inks include energy-curable varieties like ultraviolet (UV) and electron beam (EB) inks, which cure rapidly when exposed to specific light sources. UV LED inks are particularly eco-friendly since they do not rely on mercury-based lamps, making them more sustainable for digital printing.
Specialty Inks
Specialty inks, such as metallic and fluorescent inks, are used to create eye-catching effects. Metallic inks contain reflective particles, while fluorescent inks produce vibrant colors under UV light, making them popular in packaging and promotional materials.
Screen Printing Inks
Screen printing inks have a thick, paint-like texture, allowing for bold designs and vivid colors. They work well on various surfaces like textiles, ceramics, and glass, and are often used for printing designs that require a thicker ink application.
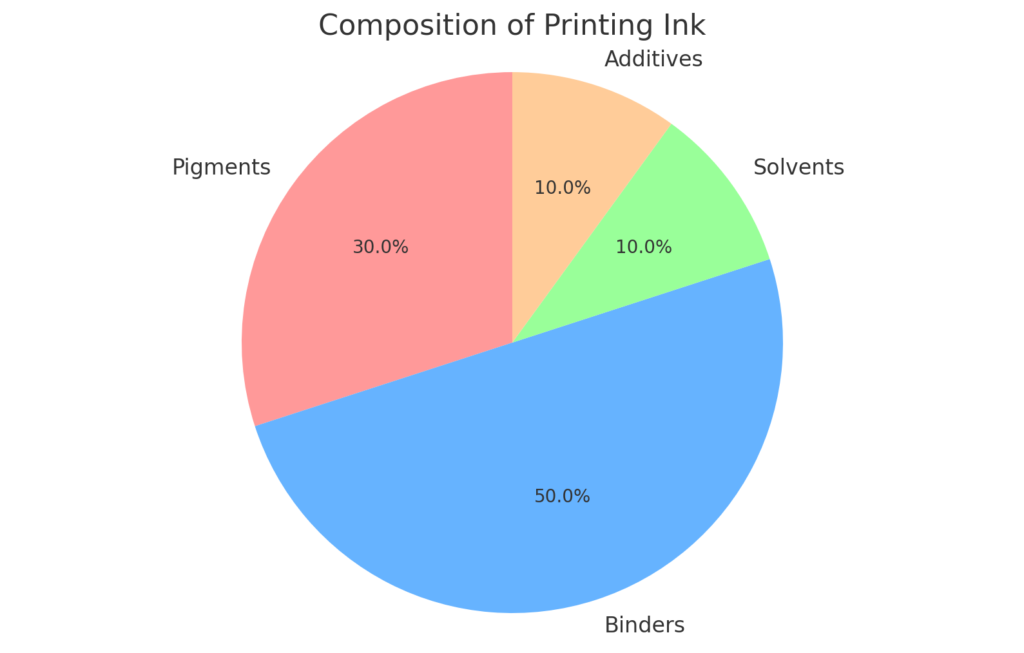
How are silicone printing inks formulated?
The formulation of silicone inks is a complex process that balances several factors, including adhesion, durability, and flexibility. Typically, these inks are made using a combination of silicone resins, curing agents, and pigments. Here’s a quick breakdown:
- Silicone Resins: These form the primary base and are responsible for adhesion to the silicone surface.
- Curing Agents: These help the ink bond with the silicone and harden once it’s printed.
- Pigments: These provide color and must be able to withstand the heat required for silicone curing.
But recent innovations have improved the quality of these components. For example, nanotechnology is now being used to enhance ink adhesion and reduce curing times, leading to more efficient production processes. Newer formulations are also designed to be more eco-friendly, using water-based solvents instead of harmful chemicals.
What innovations are driving change?
1. High-Performance Silicone Inks
One of the biggest innovations is the development of high-performance inks. These inks offer superior adhesion and resistance to wear. Unlike older formulations, they can now bond to silicone with minimal pre-treatment, reducing the production time and cost for manufacturers. This innovation benefits industries like fashion and automotive, where printed silicone is exposed to tough conditions.
2. Eco-Friendly Formulations
More companies are pushing for sustainable options. The introduction of water-based silicone inks reduces VOC emissions, making them safer for both workers and the environment. These inks are perfect for baby products and medical-grade silicone where safety standards are extremely strict. With this, U can maintain high quality without compromising on environmental regulations.
3. UV-Curable Inks
Another exciting innovation is UV-curable silicone inks. These inks use UV light to cure instead of traditional heat processes. This not only speeds up production but also improves durability and print clarity. Industries that need precision and detail, such as electronics or wearable technologies, greatly benefit from this advancement.
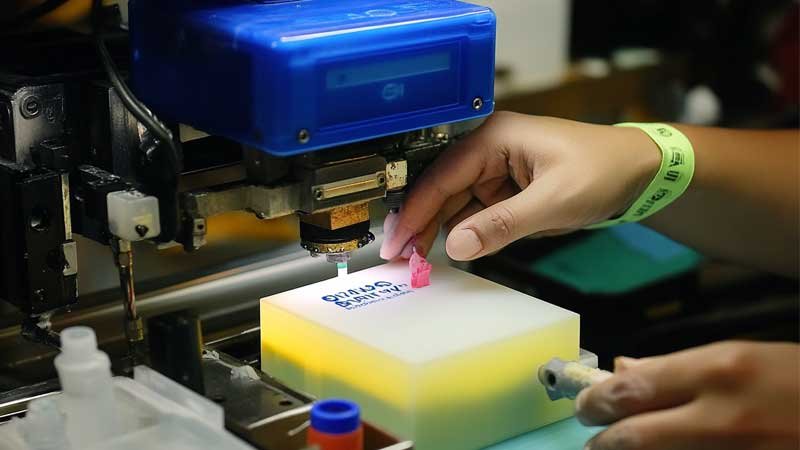
What industries benefit the most from silicone ink innovations?
Industries that rely on high-performance silicone products are the primary beneficiaries of these ink innovations. Here are a few examples:
Medical Devices
Silicone is widely used in medical devices because of its biocompatibility and flexibility. The ability to print directly onto silicone parts, like tubing or implants, using medical-grade silicone inks, opens up new possibilities in device labeling and customization. Improved formulations mean that prints are clearer and more durable, even after multiple sterilizations.
Consumer Goods
In consumer markets, customized silicone products are in high demand. Think of silicone kitchenware, toys, or even wearable technology. The durability and customization flexibility of new silicone inks allow manufacturers to offer vibrant, long-lasting designs that match their brand identity. The eco-friendly options also appeal to consumers who prefer sustainable products.
Automotive Industry
Silicone is used extensively in the automotive industry for parts like gaskets and seals. The high temperatures and wear in these environments mean the ink must be extremely durable. Heat-resistant formulations ensure that branding, instructions, or other information printed on these parts remain intact for the vehicle’s lifespan.
What are the challenges?
Despite these innovations, some challenges remain in silicone printing ink formulation.
One of the main issues is the curing process. While UV-curable inks offer an alternative, they may not be suitable for all applications, especially those involving thicker materials.
Additionally, achieving consistent adhesion on certain silicone surfaces can still be difficult. Manufacturers need to carefully balance curing agents and silicone resins to optimize performance across different applications.
Another challenge is ensuring that the ink formulations meet various regulatory requirements, especially in industries like medical devices or food-grade products. The need for non-toxic, FDA-approved materials can limit some of the more advanced formulations, but ongoing research aims to address these constraints.
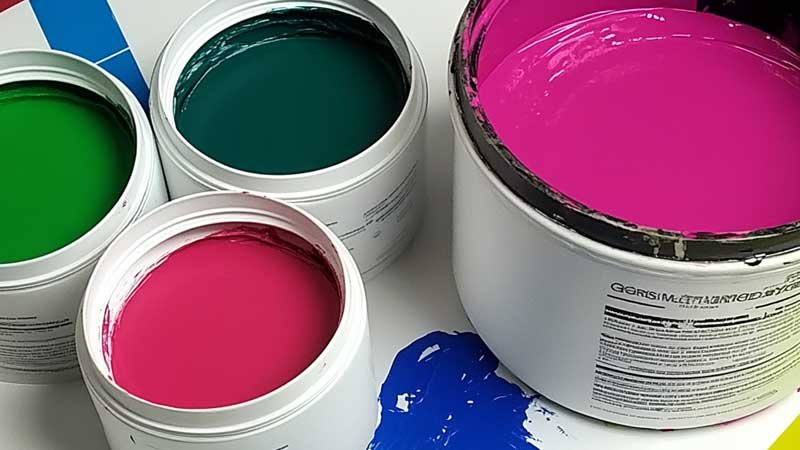
What should you consider when choosing a silicone ink supplier?
When looking for a supplier of silicone printing ink, it’s important to ask the following questions:
- Are the inks customizable?: Can the supplier tweak the formulation to meet your specific needs, whether it’s better adhesion, flexibility, or eco-friendly options?
- Do they offer a range of curing methods?: A good supplier should provide both heat-curable and UV-curable inks, depending on the application.
- Do they comply with industry regulations?: Make sure the ink formulations are compliant with FDA, REACH, or other relevant standards for your industry.
Choosing the right ink supplier can be a game-changer for your business. It’s crucial to work with a company that understands your unique requirements and has the flexibility to offer customized solutions.
How to implement silicone ink innovations into your process?
Adopting these new silicone ink formulations requires a few adjustments to your current production processes. For example, if you are switching to UV-curable inks, you will need to invest in UV light equipment, but the long-term gains in speed and quality will outweigh the initial costs. Similarly, if you’re opting for water-based inks, you may need to update your drying process.
Before making a switch, it’s wise to conduct tests on small batches to see how the ink performs under your specific conditions. This will help identify any issues with adhesion, curing times, or color vibrancy before scaling up to full production.
What does the future hold for silicone printing ink?
The future of silicone printing ink is bright, with even more innovations on the horizon. Researchers are currently exploring bio-based materials to further improve the eco-friendliness of silicone inks. At the same time, developments in 3D printing are paving the way for more complex silicone designs, requiring inks that can keep up with the intricate details.
In the next few years, you can expect to see more specialized formulations designed for niche industries, along with continued improvements in adhesion technologies. These innovations will help companies like yours deliver superior products and remain competitive in an ever-changing market.
Conclusion
Silicone printing ink formulations are evolving rapidly, with innovations that offer better performance, sustainability, and flexibility. Whether U’re in the medical device industry, consumer goods, or automotive market, these new inks provide the tools U need to enhance your product offerings and streamline your production process. Staying informed about these trends will ensure U remain ahead in the competitive silicone market.