Laser cutting has become an indispensable tool for makers and professionals alike, offering unparalleled precision and versatility in material manipulation. But what about that tricky material – silicone? Can you achieve clean, accurate cuts with a laser on this flexible friend?
Absolutely! Laser cutting silicone is a viable option, opening doors to exciting creative projects and functional applications. However, it requires specific knowledge and techniques to achieve optimal results.
Buckle up, as we delve into the world of laser cutting silicone!
Understanding the Nuances: Silicone Compatibility and Challenges
Not all silicone is created equal. The specific type of silicone, its thickness, and any additives will influence its laser cutting behavior. Generally, thinner silicone sheets (up to 0.25 inches) made from polydimethylsiloxane (PDMS) respond well to laser cutting.
Here are some challenges to consider:
- Fumes and Residue: The laser cutting process can generate fumes containing harmful byproducts. Proper ventilation is crucial to ensure a safe working environment. Additionally, a residue might form on the cut edges. While it can often be washed off with soap and water, testing on scrap material is recommended to determine the cleaning method best suited for your specific silicone.
- Material Distortion: Silicone’s flexibility can lead to warping or curling during the cutting process. Using a honeycomb cutting bed or strategically placed masking tape can help minimize this effect.
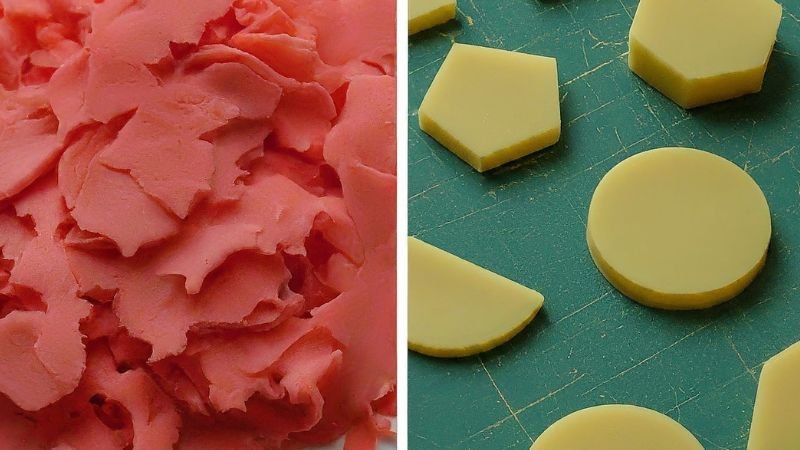
Gearing Up for Success: Essential Tips for Laser Cutting Silicone
Now that we’ve addressed the potential roadblocks, let’s explore some practical tips to ensure a smooth laser cutting experience with silicone:
- Consult your Laser Cutter Manual: Different laser cutters have varying capabilities and safety protocols. Refer to your machine’s manual for specific recommendations on laser settings and material handling for silicone.
- Test, Test, Test!: Silicone can react differently depending on its composition and thickness. Always perform test cuts on scrap material before tackling your final project. This allows you to fine-tune the laser power, speed, and cutting path to achieve clean cuts with minimal residue.
- Prioritize Ventilation: As mentioned earlier, proper ventilation is paramount. Ensure your laser cutter has an effective exhaust system to remove fumes and particulates generated during the cutting process.
- Embrace the Power of Air Assist: Most laser cutters come equipped with an air assist function. This blasts a stream of compressed air onto the cutting area, helping to remove debris and cool the material. Utilizing air assist can significantly reduce charring and improve cut quality.
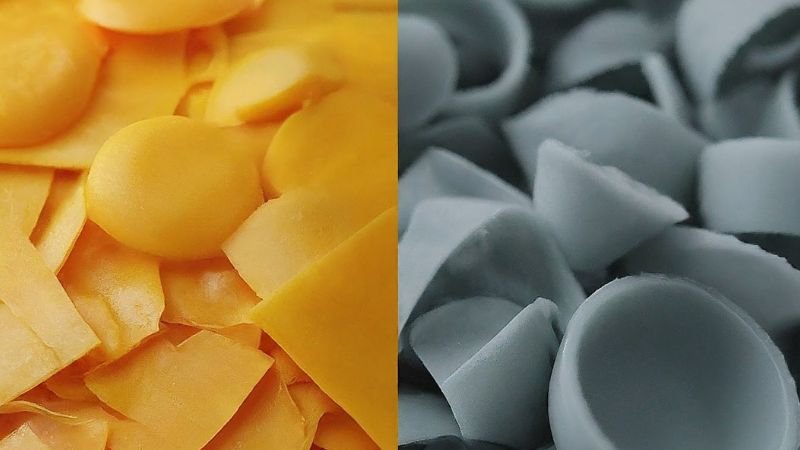
Laser Cutting Silicone: Unveiling a World of Possibilities
With the right knowledge and techniques, laser cutting silicone unlocks a treasure trove of creative and functional applications. Here are a few inspiring examples:
- Gaskets and Seals: Precisely cut silicone gaskets can provide excellent sealing properties for various applications.
- Wearable Tech Components: The flexibility and biocompatibility of silicone make it ideal for creating comfortable and customized components for wearable tech devices.
- Prototyping and Product Design: Laser-cut silicone prototypes offer a quick and cost-effective way to test form and function during the design process.
- Crafting and Art: From intricate jewelry designs to decorative appliques, laser-cut silicone can add a unique touch to various craft projects.
Embrace the Challenge, Unleash the Potential!
Laser cutting silicone might present a steeper learning curve compared to some materials. However, with the right approach and a touch of experimentation, you can unlock its potential and create innovative projects. So, fire up your laser cutter, embrace the challenge, and witness the wonders of laser-cut silicone!