Introduction
Imagine a world without silicone hoses. It’s a difficult feat because these unassuming, yet essential components play a crucial role in a wide range of industries, from automotive and aerospace to food processing and medical devices. Silicone hoses are the unsung heroes that quietly ensure the smooth operation of machinery, transport vital fluids, and withstand extreme temperatures. In this article, we will delve into the fascinating world of silicone hoses, exploring their manufacturing process, unique properties, and diverse applications.
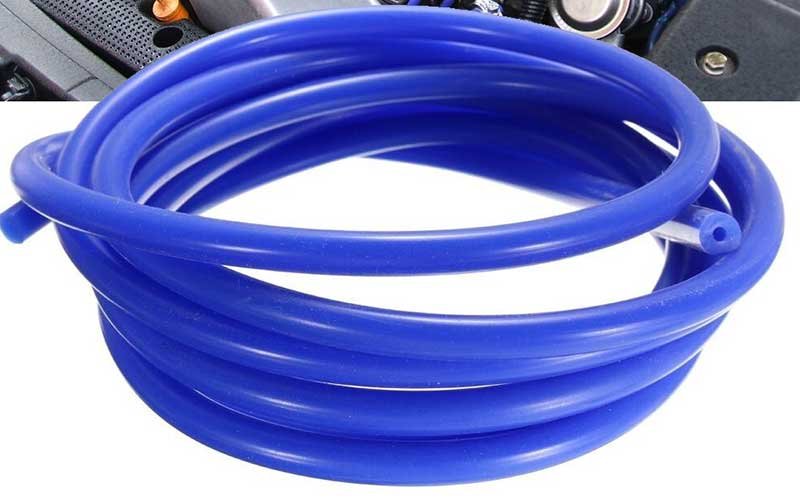
The Marvels of Silicone Manufacturing
Silicone hoses owe their exceptional qualities to the cutting-edge manufacturing process that goes into their creation. Leading silicone manufacturers, such as RY Silicone, employ advanced techniques to produce these versatile components. The process typically involves the following steps:
- Raw Material Selection: The manufacturing process begins with the careful selection of premium-grade silicone rubber, which forms the foundation of high-quality silicone hoses. Silicone rubber offers impressive resistance to extreme temperatures, chemicals, and UV radiation, making it an ideal material for various applications.
- Mixing and Preparation: The selected silicone rubber is mixed with curing agents, pigments, and other additives to achieve the desired properties and colors. This mixture undergoes meticulous processing, including milling and extrusion, to create a uniform and homogenous compound.
- Extrusion and Vulcanization: The compound is then extruded into the desired hose shape using precision molds and extrusion machinery. During the extrusion process, the silicone material is vulcanized, a chemical reaction that crosslinks the polymer chains, enhancing the hose’s strength and durability.
- Post-Curing and Quality Control: To ensure optimal performance, the silicone hoses undergo post-curing, where they are exposed to specific temperatures for a defined period. This step further improves the hose’s mechanical properties and stability. Rigorous quality control measures, including visual inspections, pressure testing, and dimensional checks, guarantee that each hose meets the highest standards.

The Unrivaled Qualities of Silicone Hoses
Silicone hoses possess a remarkable set of qualities that make them stand out among other hose materials. Let’s take a closer look at what sets silicone hoses apart:
- Temperature Resistance: Whether exposed to scorching heat or freezing cold, silicone hoses remain resilient. Withstand extreme temperatures ranging from -60°C to 200°C (-76°F to 392°F), they excel in demanding environments where other materials falter.
- Flexibility and Durability: Silicone hoses exhibit excellent flexibility, enabling easy installation and maneuverability. Their inherent elasticity ensures they can withstand repetitive bending and stretching without cracking or losing their shape, making them ideal for dynamic applications.
- Chemical Resistance: Silicone’s inert nature grants the hoses exceptional resistance to a wide range of chemicals, including acids, bases, solvents, and fuels. This quality ensures their longevity and reliability, even when exposed to aggressive substances.
- High-Purity Standards: Silicone hoses are widely used in critical applications such as pharmaceutical manufacturing and food processing. They are known for their exceptional purity, as they are free from additives and impurities that could contaminate the substances they transport.
- UV and Ozone Resistance: The unique molecular structure of silicone hoses renders them highly resistant to UV radiation and ozone exposure. This property makes them ideal for outdoor applications, such as automotive cooling systems or solar panel installations.
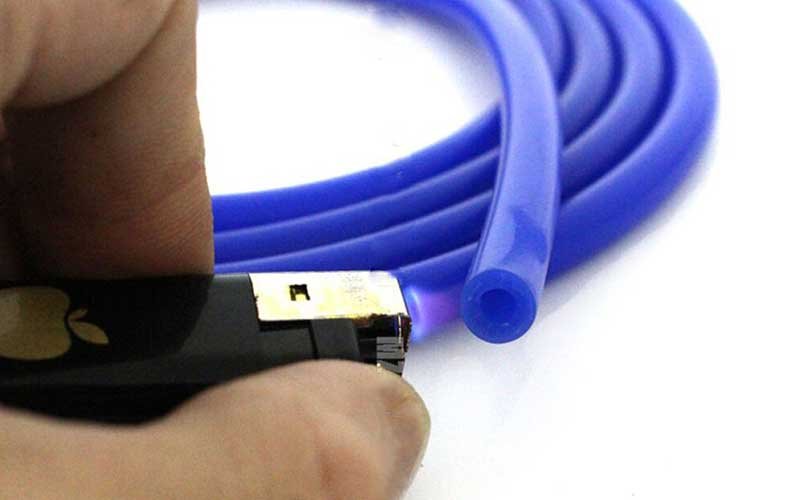
The Versatility of Silicone Hoses in Various Industries
Silicone hoses find their way into countless industrial sectors, showcasing their adaptability and reliability. Let’s explore a few examples of their diverse applications:
- Automotive and Aerospace: In the automotive and aerospace industries, silicone hoses play a critical role in engine cooling, turbocharger boost systems, and intercooler connections. Their temperature resistance and durability ensure efficient heat transfer and reliable performance, even in high-performance vehicles and aircraft.
- Food and Beverage: Silicone hoses are widely used in food and beverage processing, thanks to their high-purity standards and excellent resistance to extreme temperatures and chemicals. They are commonly employed in dairy processing, brewing, and wine production, ensuring the safe and hygienic transfer of liquids and ingredients.
- Medical and Pharmaceutical: Silicone hoses play a crucial role in medical and pharmaceutical applications, where cleanliness and biocompatibility are paramount. They are used in medical equipment, such as oxygen delivery systems, catheters, and drug delivery systems. Silicone hoses provide a safe and reliable conduit for gases and fluids, without the risk of leaching harmful substances.
- Industrial Manufacturing: In industrial manufacturing processes, silicone hoses find application in various fields. They are used in machinery and equipment for the transport of abrasive materials, chemicals, and gases. The hoses’ flexibility, durability, and resistance to wear and tear make them an ideal choice for heavy-duty applications.
- HVAC and Ventilation Systems: Silicone hoses are widely used in heating, ventilation, and air conditioning (HVAC) systems. Their temperature resistance and flexibility make them suitable for handling hot or cold air and fluids, ensuring efficient HVAC operation and energy conservation.
- Renewable Energy: With the rise of renewable energy sources, silicone hoses have become integral components in solar power systems and wind turbines. They facilitate the transfer of coolant in solar thermal systems and provide reliable connections in wind turbine installations, withstanding the challenging outdoor conditions.
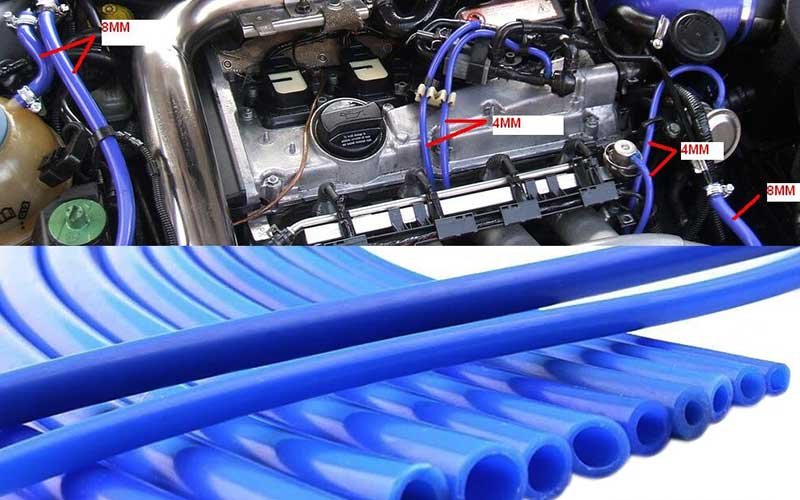
Ensuring Quality and After-Sales Service
When choosing silicone hoses for industrial applications, it’s crucial to partner with reputable manufacturers who prioritize quality and customer satisfaction. RY Silicone stands out as a leading silicone manufacturer, offering a wide range of silicone hoses engineered to meet the highest industry standards.
RY Silicone’s commitment to quality is evident in their rigorous quality management system. Every step of the manufacturing process adheres to strict quality control measures, ensuring that their silicone hoses are reliable, durable, and perform optimally in various applications. To learn more about their quality management practices, visit their Quality Management page.
Additionally, RY Silicone provides excellent after-sales service, offering technical support and guidance to their customers. Their knowledgeable team is readily available to address any concerns or questions regarding the installation, use, or maintenance of silicone hoses. This commitment to customer satisfaction sets them apart as a trusted partner in the industry. Explore their After-Sales Service offerings for more information.
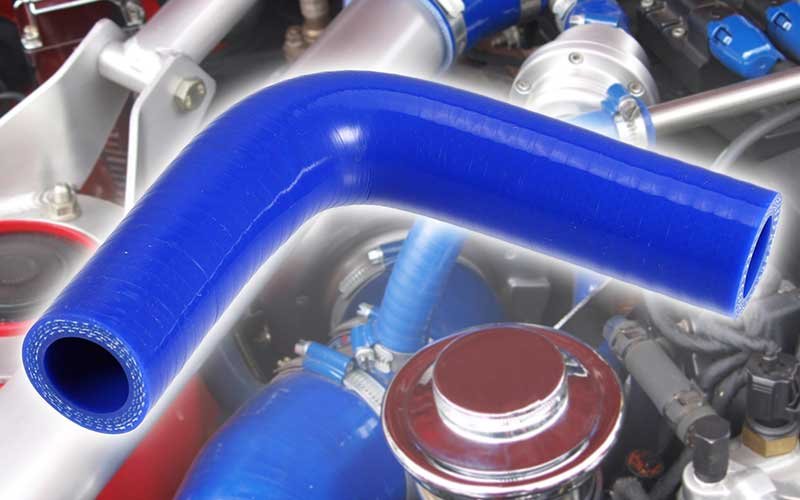
Conclusion
Silicone hoses may not often take the spotlight, but their impact on various industries cannot be overlooked. These versatile components possess remarkable properties, including temperature resistance, flexibility, and chemical resistance, making them indispensable in demanding applications. Whether in automotive engines, food processing plants, or medical devices, silicone hoses ensure the smooth and reliable operation of vital systems.
Choosing a reliable silicone manufacturer is paramount to ensuring the quality and performance of silicone hoses. RY Silicone, with its advanced manufacturing process and commitment to excellence, stands out as a trusted provider of high-quality silicone hoses. Their dedication to quality management and after-sales service sets them apart in the industry.
Next time you encounter a well-functioning engine, enjoy safe food and beverages, or benefit from efficient HVAC systems, take a moment to appreciate the unsung heroes—silicone hoses—working tirelessly behind the scenes.
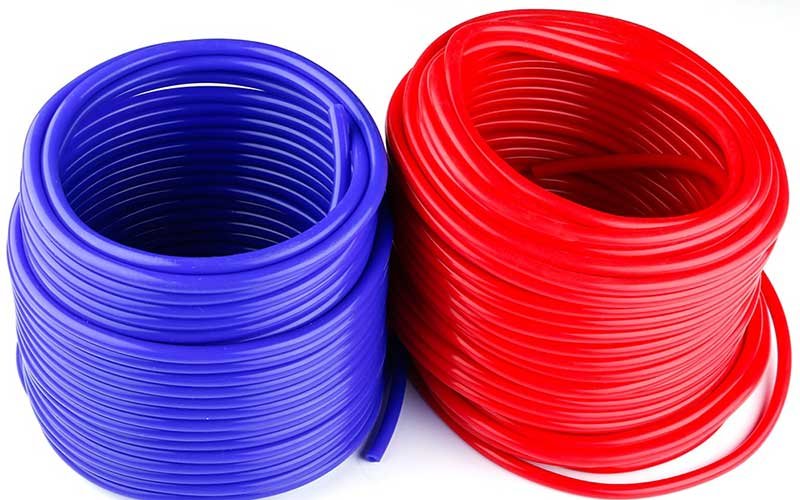
FAQs
Q: Are silicone hoses better than OEM?
A: Silicone hoses offer several advantages over Original Equipment Manufacturer (OEM) hoses. They are known for their exceptional durability, flexibility, and resistance to extreme temperatures. Unlike some OEM hoses, silicone hoses are less prone to cracking, swelling, or deteriorating over time. Additionally, silicone hoses provide superior resistance to oil, coolant, and other automotive fluids, making them a reliable choice for various applications.
Q: What are the disadvantages of silicone hoses?
A: While silicone hoses have numerous advantages, they also have a few drawbacks. One of the main disadvantages is their higher cost compared to traditional rubber hoses. Silicone hoses can be more expensive due to the manufacturing process and the quality of materials used. Additionally, silicone hoses may not be suitable for certain applications that involve exposure to abrasive materials or extreme mechanical stress, as they may be more prone to physical damage.
Q: How long do silicone hoses last?
A: The lifespan of silicone hoses can vary depending on several factors, including the quality of the hose, the application, and the operating conditions. In general, well-maintained silicone hoses can last significantly longer than traditional rubber hoses. With proper installation and regular inspection for any signs of wear or deterioration, silicone hoses can typically last between 5 to 10 years or even longer.
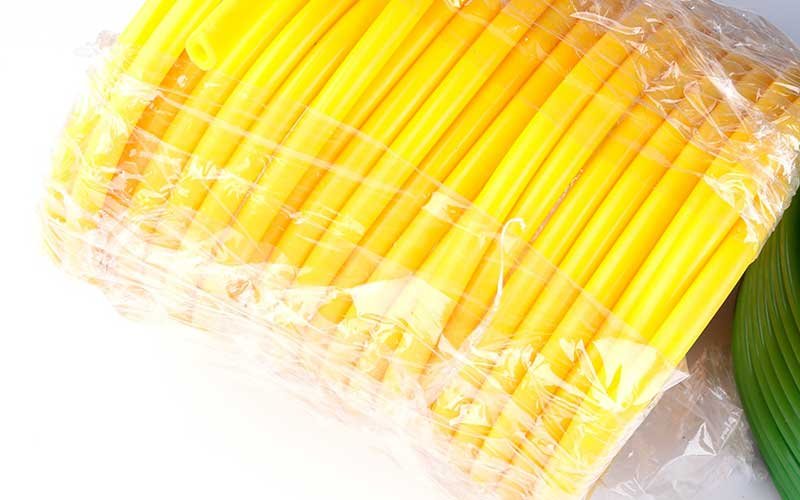
Q: What are the weaknesses of silicone?
A: While silicone is a versatile material with numerous benefits, it does have some weaknesses. One of the main weaknesses is its relatively low resistance to certain solvents and fuels, such as petroleum-based products. Exposure to these substances can cause degradation or swelling of silicone over time. Additionally, silicone can be more prone to damage from sharp objects or excessive twisting and bending, making it important to use it in appropriate applications.
Q: Are braided hoses better than rubber?
A: Braided hoses and rubber hoses serve different purposes and have their own advantages and disadvantages. Rubber hoses are often more affordable and suitable for many general-purpose applications. On the other hand, braided hoses, typically made with a combination of synthetic rubber and reinforced with wire or textile braids, offer higher burst pressure resistance and increased durability. Braided hoses are commonly used in high-pressure applications, such as hydraulic systems, where the additional strength is necessary.
Q: Are silicone hoses worth it?
A: Silicone hoses can be a worthwhile investment depending on the specific application and requirements. They offer superior temperature resistance, flexibility, and durability compared to many other materials. If you need a hose that can withstand extreme temperatures, harsh chemicals, or demanding operating conditions, silicone hoses are often the preferred choice. However, it is essential to consider the cost and suitability for your specific needs before making a decision.
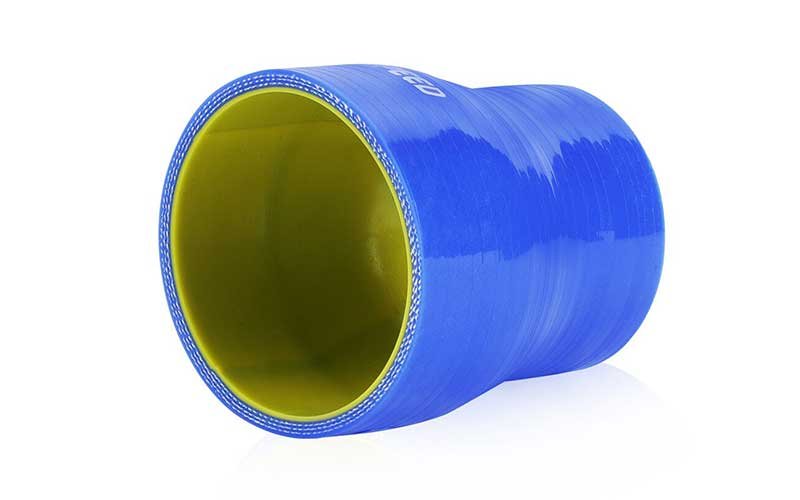
Q: Why are rubber hoses not recommended?
A: Rubber hoses are widely used in various applications and can be suitable for many purposes. However, they may not be recommended in certain situations due to their limitations. Rubber hoses are generally less resistant to extreme temperatures, chemicals, and environmental factors compared to silicone hoses. They can degrade or deteriorate over time when exposed to harsh conditions, leading to leaks, cracks, or failure. In applications where higher temperature resistance, durability, and chemical resistance are required, silicone hoses are often preferred over rubber hoses.
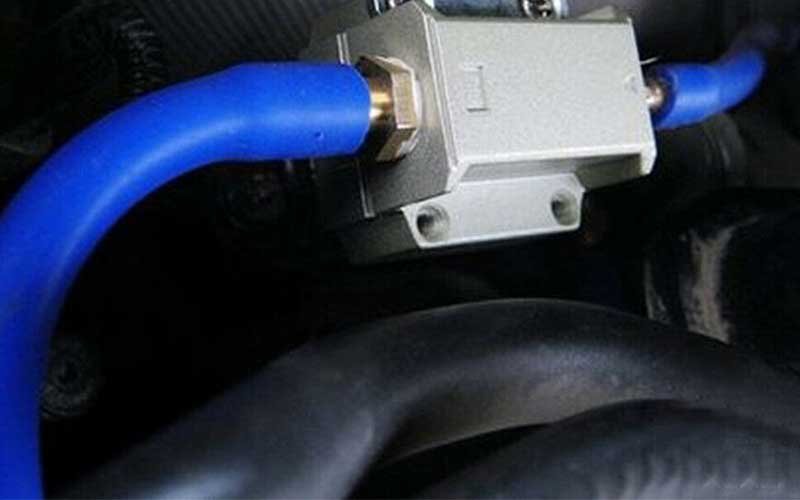
Q: Why is silicone bad in manufacturing?
A: Silicone itself is not inherently bad in manufacturing; in fact, it has numerous beneficial properties that make it desirable for many applications. However, there are certain considerations to keep in mind when using silicone in manufacturing. Silicone can have a higher initial cost compared to other materials, which may impact overall manufacturing expenses. Additionally, silicone can be more challenging to bond or adhere to other materials, requiring specific techniques or adhesives. It’s important for manufacturers to understand the unique characteristics of silicone and its compatibility with the manufacturing processes and materials involved.
Q: What is the problem with silicone?
A: While silicone is a versatile material, it does have some limitations and considerations. One common issue is its lower resistance to certain solvents, fuels, and oils compared to other materials like fluoropolymers. Prolonged exposure to these substances can cause swelling or degradation of silicone. Additionally, silicone may not be as abrasion-resistant as some other materials, making it less suitable for applications that involve high levels of wear or mechanical stress. Manufacturers and users should assess the specific requirements and potential challenges of their application to determine if silicone is the most suitable choice.
To learn the difference between silicone hose and silicone tubing.