To improve the application of silicone rubber, it is essential to have a good understanding of its sources, classification, and properties. Rubber can be classified into natural and synthetic types.
The Difference Between Rubber and Silicone Rubber
Natural rubber, also known as latex, is derived directly from the rubber tree, while synthetic rubber is created by mixing different materials to obtain various properties, including elasticity, and is referred to as an elastomer.
When compared to natural rubber, silicone rubber has several advantages. It can withstand high temperatures of up to 230°C, while natural rubber can only handle temperatures of up to around 80°C before melting and degrading.
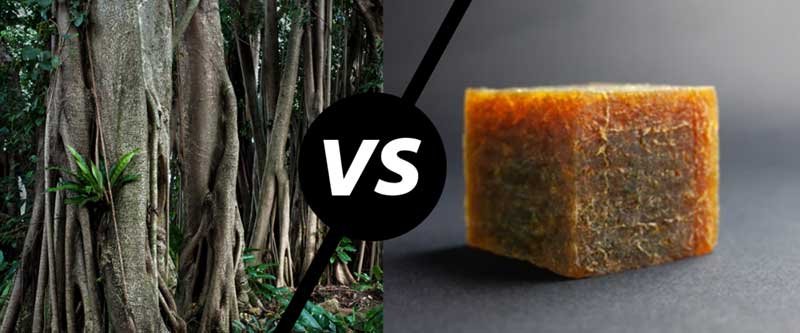
Additionally, silicone offers superior flame resistance and is more chemically, weather, and UV resistant.
As a result, it is the preferred choice for high-temperature applications and outdoor use. Finally, the four main types of silicone rubber will be reviewed.
1. Room Temperature Vulcanized (RTV)
Silicones that do not require heat to cure and take their final shape are known as “room-temperature vulcanizing” (RTV) silicones, which can be of two types: one-component (RTV-1) and two-component (RTV-2) formulations.
RTV-1 is a ready-to-use product, where a stabilizing agent in the silicone reacts with the air’s moisture, causing the outer layer to cure quickly. These silicones are appreciated for their ease of use, good adhesion, and high-temperature stability, making them suitable for various applications such as sealants, bonding glues, and coatings.
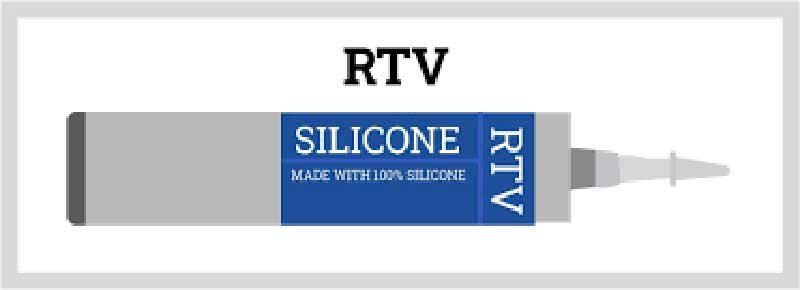
RTV-2 is a two-part formulation that requires mixing before use, and it cures faster than RTV-1. It is available in a wider range of products and has excellent mechanical properties across a broad temperature range. Platinum-cured RTV-2 silicones are preferred for applications that require no byproducts. Some typical applications of RTV-2 include 3D printing, coatings, and molds.
2. Liquid Silicone Rubber (LSR)
“Liquid silicone” generally denotes the initial form of the raw material used for creating silicone products. In the past, silicone grades were supplied in a semi-solid, gum-like state that required compression molding.
Liquid silicone rubber (LSR), however, is a two-part, platinum-cured raw material with high fluidity, which enables the precise capturing of details in injection-molded components or the coating of any surface shape.

LSR’s platinum-curing cross-linking system doesn’t produce any byproducts during curing, making it a safe material for applications that require food and medical-grade standards.
What Is Food-Grade LSR?
Food-grade liquid silicone rubber is a highly versatile material that is ideal for manufacturing consumer products. Its ability to withstand extreme temperatures makes it an excellent choice for kitchen products, including plastic grips for tableware and cooking tools, ice cube trays, and baking molds. In addition, food-grade LSR is well-suited for use with any industrial equipment that comes into contact with or is exposed to food, thanks to its ease of sterilization and compression settings.
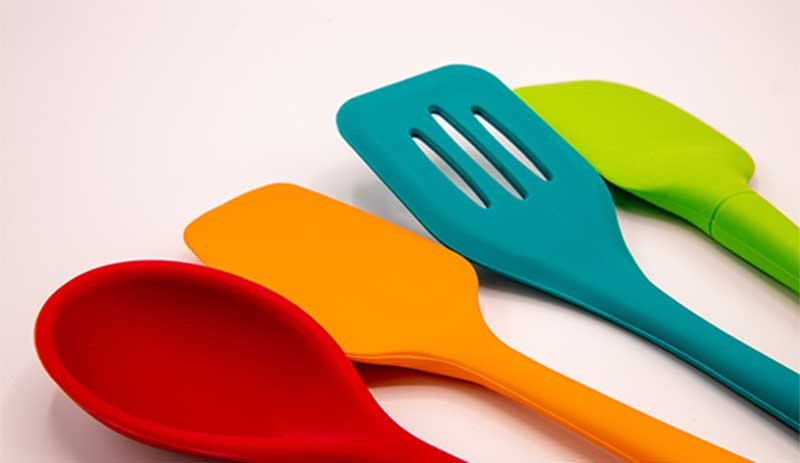
What Is Medical-Grade LSR?
Manufacturing companies in the medical device industry prefer to use medical-grade LSRs. These LSRs allow manufacturers to meet the challenges associated with producing complex, technologically advanced devices, while also improving quality, reducing costs, and enhancing the durability of the final product.
3. Fluorosilicone
Fluorosilicone is a type of polysiloxane molecule that provides enhanced resistance to challenging environments, such as fuels, oils, mineral oils, and organic solvents. Despite having nearly the same mechanical properties as regular silicones, fluorosiloxane offers better chemical resistance.
However, it is less effective in hot air and more expensive. It is commonly used in aerospace and automotive applications where exposure to chemicals is a concern.

4. High-Consistency Rubber (HCR)
“Solid silicone” or “gum stock” are other names for High Consistency Silicone Rubber (HCR), which is made up of high molecular weight polysiloxane chains. HCR can be augmented with a range of fillers to improve specific properties like heat resistance and hardness. It can be cured using peroxide curing or platinum catalyst formulations. The platinum catalyst option does not produce chemical by-products while curing.
HCR is supplied in bulk forms like rods, cylinders and tubes for further processing. This material is ideal for long-term implantable medical devices, automotive engine components, and various household consumer products.

Summary
Silicones are non-organic elastomeric polymers with a wide range of properties, making them adaptable to various forms and applications. While silicone is a type of rubber with alternating silicon and oxygen atoms, it offers better performance at temperature extremes and a broader range of properties than natural rubber. Liquid rubber sealants may be silicone-based or based on other materials, while liquid silicone rubber (LSR) is always silicone and used for injection molding, bonding, and sealing applications.
The process of manufacturing products is different for different silicone, you can click here to learn more. Silicone Manufacturing Process.