Silicone products are vital across various industries, renowned for their flexibility and longevity. Two key processes in their manufacturing are curing and vulcanization. Though both play pivotal roles in converting silicone from its raw form to a functional state, they utilize different methods and produce distinct outcomes. This article breaks down the nuances of each process, emphasizing their unique importance in silicone production.
What is Curing?
Curing is the foundational process in the manufacturing of silicone products. It is the transformation of raw silicone into a solid, usable material via a reaction facilitated by heat or UV light in the presence of a catalyst. This process forges a stable network of silicone polymers, which equips the material to withstand environmental stressors. This step is crucial for creating dependable products, ranging from pliable kitchenware to robust sealants in construction.
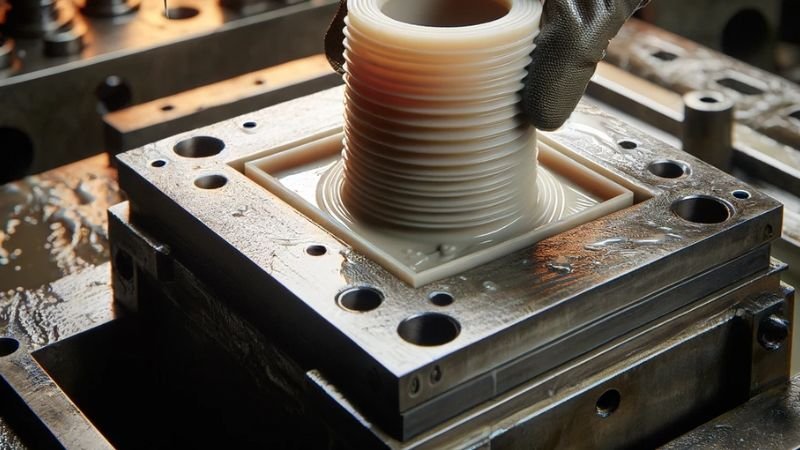
What is Vulcanization?
Vulcanization is an advanced stage of curing. It employs sulfur or similar cross-linking agents to form extra bonds between the silicone polymers under heat. This process not only hardens the silicone but also enhances its properties, increasing its resistance to thermal and mechanical stress. Vulcanized silicone is, therefore, better suited for more demanding applications.
Key Differences
While both curing and vulcanization transform silicone into its final form, they differ in methodology and the characteristics of the end product.
Aspect | Curing | Vulcanization |
---|---|---|
Process | General hardening of silicone. | Specialized curing with cross-linking agents. |
Chemicals Used | Catalysts. | Sulfur or other cross-linking agents. |
Heat Requirement | Necessary to activate catalysts. | Higher temperatures for cross-linking. |
Resulting Properties | Stable, resistant to environmental factors. | Enhanced strength, thermal resistance. |
Typical Use | General-purpose products (kitchen tools, sealants). | High-performance applications (automotive, aerospace). |
The table above succinctly illustrates the distinctions, providing a clear, at-a-glance comparison between the two processes.
The Process in Action: A Closer Look
Manufacturers must tailor these processes to the specifications of the final product. Standard curing may be accomplished with heat alone, but vulcanization demands precise control over cross-linking agents and temperature to achieve the desired material properties.
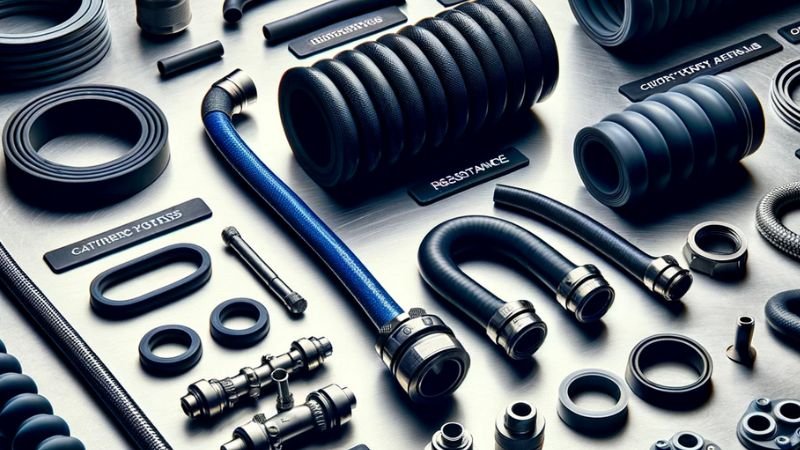
Applications and Examples
The application of cured and vulcanized silicone spans a vast range of products. The following chart outlines the typical uses in various industries, demonstrating the versatility of silicone products.
Silicone Application Chart
Industry | Cured Silicone Applications | Vulcanized Silicone Applications |
---|---|---|
Automotive | Interior buttons, trims | Engine gaskets, hoses |
Aerospace | Window seals, interior mounts | Fuel hoses, door seals |
Consumer Goods | Cooking utensils, bakeware | Heat-resistant cookware handles |
Construction | Sealants, gaskets | Structural glazing seals |
Electronics | Keyboards, flexible circuits | Insulation for wires, connectors |
The chart clarifies the breadth of silicone’s use, indicating how curing and vulcanization cater to different product demands.
Conclusion
Curing and vulcanization are not just chemical reactions but are crucial steps that define the performance and durability of silicone products. Curing sets the stage for the product’s shape and texture, while vulcanization enhances its ability to withstand extreme conditions. For companies like PMS, mastery over these processes ensures that their injection-molded products meet the high expectations of a diverse, international market. This deep dive into the two methods reveals their indispensable role in creating high-quality silicone goods tailored for a global audience.