The silicone mold industry is rapidly evolving, driven by demand for high-quality, customizable, and eco-friendly manufacturing. Industries across sectors are embracing silicone molds for their versatility and efficiency. This progress is fueled by continuous innovation in mold manufacturing.
This article will explore how cutting-edge technologies and material advancements are transforming industries worldwide. We will examine how these innovations contribute to enhanced precision, faster production cycles, and increased sustainability and versatility in silicone mold manufacturing.
Businesses are constantly seeking faster production times, improved material quality, and eco-friendly solutions. The rise of automation, digitalization, and innovative techniques has enabled the production of highly intricate molds with precision and reduced costs. This article will explore some of the most significant advancements driving the growth of silicone mold manufacturing.
What is Silicone Mold Manufacturing?
Before diving into the innovations, let’s take a step back and define silicone mold manufacturing. Silicone molds are used to create products in various industries, including automotive, healthcare, food, consumer goods, and more. Made from silicone rubber, which is flexible, durable, and heat-resistant, these molds are popular due to their ability to capture intricate details, resist wear and tear, and perform well under high-temperature conditions.
Silicone molds have been used for decades, but recent developments in both the material and manufacturing processes have opened up a world of possibilities. These improvements help manufacturers create more accurate, durable, and cost-effective products, increasing their demand in numerous industries.
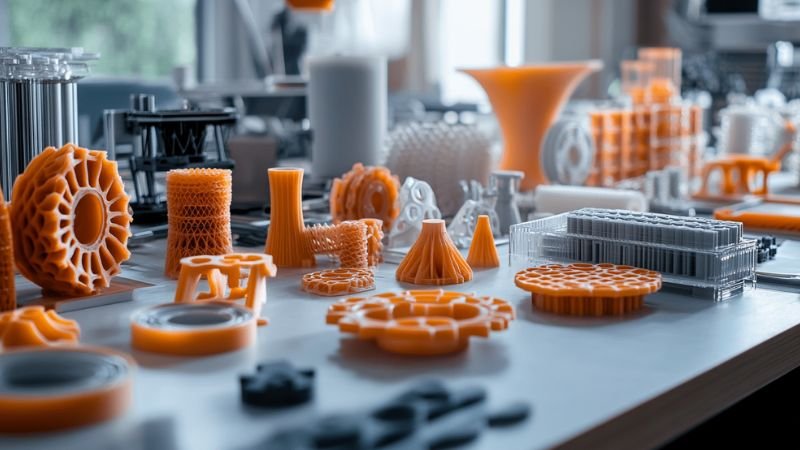
1. 3D Printing and Rapid Prototyping in Silicone Mold Manufacturing
One of the most exciting innovations in silicone mold manufacturing is the integration of 3D printing. 3D printing allows manufacturers to create complex and highly detailed molds with greater precision and reduced lead time. Traditionally, mold manufacturing required lengthy processes, including CNC machining and casting. But now, 3D printing is revolutionizing the industry by allowing manufacturers to rapidly prototype molds without the need for expensive tooling or molds.
How it works
- Manufacturers design molds using CAD (computer-aided design) software, then use 3D printers to build molds layer by layer.
- The 3D printed molds can be made from a variety of materials, including silicone-based resins, and they offer intricate detail that is hard to achieve through traditional methods.
- These molds can be used in the production of silicone products, offering flexibility in terms of design and faster turnaround times.
By cutting down on design time, reducing costs, and offering an unprecedented level of precision, 3D printing is playing a key role in making silicone mold manufacturing faster, cheaper, and more accurate than ever before.
2. Improved Silicone Materials and Formulations
Another significant innovation in silicone mold manufacturing is the development of improved silicone materials. While traditional silicone rubbers are known for their durability and flexibility, newer formulations are taking these qualities to the next level. These new materials offer superior heat resistance, greater tear strength, and enhanced ability to withstand extreme conditions.
Some of the new materials include
- High-temperature-resistant silicone: Ideal for molds used in industries like automotive and aerospace, these silicone materials can withstand temperatures up to 300°C or higher.
- Food-grade silicone: With growing demand for safe and sustainable products, food-grade silicone is now widely used in baking molds, baby products, and kitchenware. The material is non-toxic, flexible, and meets stringent safety standards.
- Bio-based silicones: As sustainability becomes a key concern for manufacturers and consumers alike, bio-based silicones are being introduced. These silicones are made from renewable resources like plant-based oils, reducing the environmental impact of production.
The development of these advanced materials has opened up new possibilities for silicone mold applications, making them not only more reliable but also more eco-friendly.
3. Automation and Robotics in Mold Production
Automation has made its way into nearly every part of manufacturing, and silicone mold production is no exception. The use of robotics and automated systems in mold manufacturing has led to improved efficiency, accuracy, and scalability in production processes. These systems enable manufacturers to produce large quantities of molds quickly and with minimal human intervention, reducing errors and lowering labor costs.
Key advantages of automation in silicone mold manufacturing
- Precision and consistency: Robots can perform repetitive tasks, such as pouring silicone, cutting molds, and assembling parts, with perfect consistency. This leads to highly accurate and uniform molds, which are crucial for high-quality end products.
- Increased speed: Automated systems allow for faster production cycles, making it possible to meet high demand with shorter lead times.
- Reduced human error: With automated systems handling the most time-consuming aspects of mold manufacturing, there’s less chance for human error, which ultimately leads to fewer defects and higher-quality products.
Incorporating automation into silicone mold manufacturing not only increases efficiency but also allows for greater customization and a more streamlined production process.
4. Precision Molding with Advanced Injection Molding Technology
Injection molding has long been a popular method for producing silicone parts, and recent advances in injection molding technology have made the process even more precise and efficient. With innovations like multi-shot injection molding, manufacturers can produce more complex parts with multiple materials or colors in a single mold.
What’s new in precision molding
- Multi-material molding: Advanced injection molding allows manufacturers to inject different types of silicone or other materials into the same mold, creating products with multiple textures, colors, and properties.
- Micro-injection molding: This technique allows for the production of smaller, intricate parts with extreme precision, making it ideal for industries like electronics, medical devices, and automotive manufacturing.
- Gas-assisted injection molding: This method uses gas to create hollow sections in silicone molds, which can reduce material usage and improve product lightness without sacrificing strength.
These advanced injection molding techniques enable manufacturers to create high-quality silicone molds and products with less waste, more accuracy, and greater design flexibility.
5. Sustainable Practices in Silicone Mold Manufacturing
As environmental concerns continue to rise, sustainability has become a key factor in innovation within silicone mold manufacturing. Manufacturers are looking for ways to minimize their environmental impact while still meeting the growing demand for silicone products. From using bio-based silicone to improving waste management processes, the industry is embracing greener practices.
Sustainability innovations include
- Recyclable silicone: While traditional silicone is durable and long-lasting, it can be difficult to recycle. However, new formulations of recyclable silicone are being introduced, allowing molds to be reused or repurposed instead of being discarded.
- Energy-efficient manufacturing processes: Manufacturers are implementing energy-efficient machines and practices to reduce the carbon footprint of their operations. This includes using renewable energy sources, optimizing production processes, and reducing waste during mold creation.
- Zero-waste molding: Advances in silicone mold design have allowed for zero-waste manufacturing, where every bit of material is used efficiently to create molds and parts, minimizing scrap and reducing waste.
These sustainable practices are helping to create a more eco-friendly future for silicone mold manufacturing while still maintaining high-quality production standards.
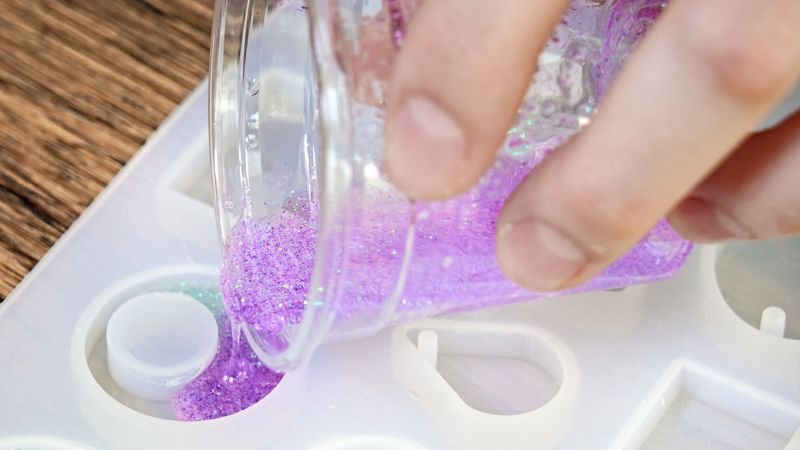
6. Digitalization and Smart Mold Production
Another significant trend in silicone mold manufacturing is the integration of digital technologies. From CAD software and simulations to real-time data analytics, digital tools are transforming how manufacturers design, produce, and optimize silicone molds.
Digital tools are enhancing mold production in several ways
- Virtual design and simulation: Using CAD software and digital simulations, manufacturers can test the mold’s performance before even creating it. This reduces the chances of design flaws and minimizes material waste.
- Real-time production monitoring: IoT sensors and data analytics tools are helping manufacturers monitor production processes in real-time, enabling them to adjust machine settings and improve quality control.
- Predictive maintenance: With digital technologies, manufacturers can predict when equipment is likely to fail, allowing them to perform maintenance before problems arise. This reduces downtime and improves overall production efficiency.
The digital transformation of silicone mold manufacturing is not just about improving the production process—it’s about creating smarter, more responsive systems that enhance efficiency and ensure the highest quality.
7. Customization and On-Demand Production
As markets demand more personalized products, manufacturers are turning to advanced molding technologies to offer greater customization. Consumers are no longer satisfied with one-size-fits-all solutions—they want products that meet their specific needs. Silicone molds are no exception, and new innovations in custom mold production are making it easier than ever to create unique designs.
Customization trends include
- Low-volume production: With the rise of on-demand manufacturing, silicone mold manufacturers are now able to produce small batches of highly customized molds. This is perfect for industries that require low-volume but highly intricate products, such as the medical or luxury goods industries.
- Flexible design options: Advancements in mold-making techniques allow manufacturers to offer more flexible design options. From intricate details to complex shapes, silicone molds can be adapted to meet the unique specifications of clients.
These innovations are helping businesses create highly tailored products that appeal to a wide range of consumers, without sacrificing efficiency or cost-effectiveness.
Conclusion
Innovations in silicone mold manufacturing have transformed the industry in recent years, paving the way for faster, more accurate, and sustainable production methods. Whether through advancements in 3D printing, automation, material science, or digitalization, manufacturers are continually pushing the boundaries of what’s possible in mold production.