Introduction
Hello there! If you’ve ever wondered how that flexible, yet sturdy silicone kitchen spatula came to be, you’re in the right place. Today, we’re diving deep into the fascinating world of silicone vulcanization. 🎉
The Importance and Application Areas of Silicone
Silicone is everywhere! From medical devices like catheters to everyday items like baking mats, silicone’s unique properties make it a material of choice for a multitude of applications. It’s heat-resistant, chemically stable, and electrically insulating—talk about a triple threat!
Vulcanization as a Key Step in Silicone Production
But how does silicone get these amazing properties? The answer lies in a process called vulcanization. This is the magical transformation where silicone goes from a gooey liquid to a flexible, yet strong, solid. It’s like the “oven” phase in a baking recipe, where all the ingredients come together to form something wonderful.
Basics of Silicone
Chemical Structure and Physical Properties of Silicone
Silicone is a fascinating material, chemically speaking. It’s primarily made up of a backbone of silicon and oxygen atoms, unlike organic rubbers that are carbon-based. This unique structure gives silicone its remarkable properties:
- Heat Resistance: Can withstand temperatures up to 600°F (315°C)
- Chemical Stability: Resistant to most chemicals and solvents
- Electrical Insulation: Excellent insulator, making it ideal for electrical applications
Comparison Between Silicone and Other Types of Rubber
You might be wondering, “Why not just use regular rubber?” Well, each type of rubber has its own set of pros and cons. Here’s a quick comparison:
Property | Silicone | Natural Rubber | Nitrile Rubber |
---|---|---|---|
Heat Resistance | High | Low | Moderate |
Chemical Stability | High | Moderate | High |
Electrical Insulation | High | Low | Low |
Cost | High | Low | Moderate |
As you can see, silicone stands out in areas like heat resistance and electrical insulation, making it the go-to material for specialized applications.
Overview of Vulcanization Process
Definition and Importance of Vulcanization
Vulcanization is the heart of the silicone-making process. It’s like the “bake” button on your oven—once you press it, there’s no going back. Vulcanization transforms silicone from a soft, dough-like consistency into a durable, elastic material. It’s the step that gives silicone its “superpowers,” like heat resistance and flexibility.
Main Steps Involved in the Vulcanization Process
The vulcanization process can be broken down into a few key steps:
- Mixing: Combine silicone with vulcanizing agents and other additives.
- Molding: Shape the silicone into its final form, whether that’s a sheet, a tube, or a custom shape.
- Heating: Apply heat to initiate the chemical reactions that will form cross-links between the silicone molecules.
- Cooling: Allow the silicone to cool, solidifying its new structure.
- Post-treatment: Additional steps like washing or coating may be necessary, depending on the application.
Choice of Vulcanizing Agents
Different Types of Vulcanizing Agents and Their Impact
When it comes to vulcanizing agents, one size definitely doesn’t fit all. The choice of agent can significantly impact the properties of the final silicone product. Here are some common types:
- Organic Peroxides: Ideal for high-temperature applications, these agents are often used in free radical vulcanization.
- Platinum Catalysts: These are the “luxury cars” of vulcanizing agents, often used in addition vulcanization for their efficiency and precision.
- Organic Tin Compounds: Commonly used in room temperature vulcanization, these agents are great for quick-setting applications.
How to Choose the Right Agent
Choosing the right vulcanizing agent depends on various factors:
- End Application: Is the silicone product going to be used in a high-heat environment? Or does it need to be food-safe?
- Cost: Platinum catalysts might be efficient, but they’re also expensive. Budget constraints can influence your choice.
- Processing Time: Some agents work faster than others, which can be crucial in industrial settings.
Vulcanization Equipment and Techniques
Commonly Used Vulcanization Equipment
The vulcanization process isn’t a one-man show; it requires specialized equipment to get the job done right. Here are some of the key players:
- Mixers: These ensure that the silicone and vulcanizing agents are well-blended.
- Molds: These give shape to the silicone, whether it’s a simple sheet or a complex geometric form.
- Ovens or Autoclaves: These provide the heat necessary for the vulcanization reaction to occur.
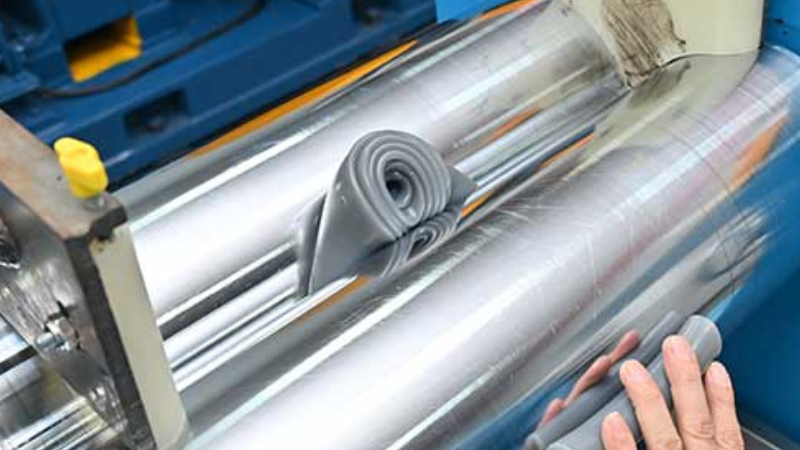
Optimization of the Process Flow
Efficiency is key in any production process, and vulcanization is no exception. Here are some tips for optimizing the process:
- Temperature Control: Precise temperature control can speed up the reaction and improve the quality of the final product.
- Time Management: Over-vulcanizing can lead to a brittle product, while under-vulcanizing may result in incomplete cross-linking.
- Quality Checks: Regular testing ensures that the vulcanized silicone meets all required specifications.
Comparison Table of Vulcanization Methods
Before we dive into the specifics of each vulcanization method, let’s take a look at how they stack up against each other. This table provides a quick snapshot to help you understand the pros and cons of each method.
Vulcanization Type | Common Catalysts | Reaction Conditions | Main Advantages | Main Limitations | Typical Applications |
---|---|---|---|---|---|
Free Radical | Organic Peroxides | High Temp, Short Time | High Strength | Costly, Complex | Automotive, Aerospace |
Addition | Platinum Catalysts | Moderate Temp, Long Time | Precision | Expensive | Medical Devices |
Room Temperature | Organic Tin Compounds | Room Temp, Varies | Quick Setting | Limited Strength | Sealants, Adhesives |
High-Temperature | Organic Peroxides, Platinum | Very High Temp, Short Time | Extreme Resistance | Energy Intensive | Industrial Seals |
Special Techniques | Various | Varies | Niche Solutions | Limited Scope | Research, Specialized |
Free Radical Vulcanization
Catalysts and Reaction Conditions
In the realm of Free Radical Vulcanization, organic peroxides are the stars of the show. These catalysts initiate the reaction at high temperatures, typically ranging from 150°C to 200°C. The process is relatively quick, often completed within minutes.
Reaction Mechanism
Here’s where the magic happens:
- Initiation: The organic peroxide breaks down due to heat, generating free radicals.
- Propagation: These free radicals attack the silicone chains, creating new radicals that continue the chain reaction.
- Termination: Eventually, the radicals combine to form stable cross-links, solidifying the silicone’s structure.
Advantages and Limitations
Advantages:
- High Strength: This method produces silicone with excellent mechanical properties.
- Speed: The reaction is relatively quick, making it suitable for mass production.
Limitations:
- Cost: Organic peroxides can be expensive.
- Complexity: The process requires precise control of temperature and time.
Application Cases
In the automotive and aerospace industries, the high-strength silicone produced through Free Radical Vulcanization is often used in gaskets, seals, and various other components that need to withstand extreme conditions.
Addition Vulcanization
Catalysts and Reaction Conditions
When it comes to Addition Vulcanization, platinum catalysts are often the go-to choice. These catalysts work at moderate temperatures, usually between 100°C and 150°C, and the process can take a bit longer, ranging from several minutes to a few hours.
Reaction Mechanism
The steps involved in Addition Vulcanization are as follows:
- Activation: The platinum catalyst activates the silicone, preparing it for the addition reaction.
- Addition: New bonds are formed through an addition reaction, creating a cross-linked structure.
- Stabilization: The newly formed structure is stabilized, completing the vulcanization process.
Advantages and Limitations
Advantages:
- Precision: This method allows for very precise control over the silicone’s properties.
- Versatility: Suitable for a wide range of applications, from medical devices to consumer goods.
Limitations:
- Cost: Platinum catalysts are expensive, which can drive up production costs.
- Time: The process can be time-consuming, especially for complex shapes and structures.
Application Cases
In the medical field, Addition Vulcanization is often used to produce silicone components that require high precision and biocompatibility, such as catheters and prosthetics.
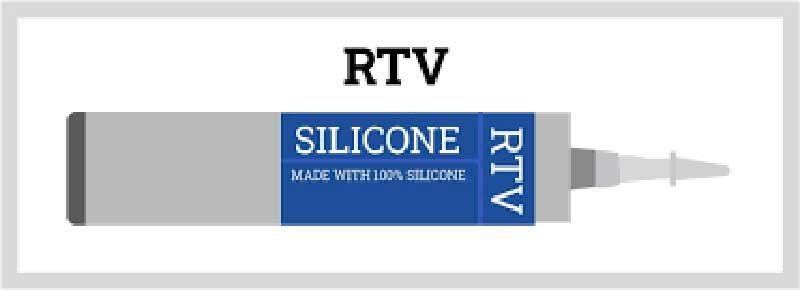
Room Temperature Vulcanization
Catalysts and Reaction Conditions
Room Temperature Vulcanization (RTV) typically employs organic tin compounds as catalysts. As the name suggests, this process occurs at room temperature and can vary in duration, from a few minutes to several hours.
Reaction Mechanism
The steps are fairly straightforward:
- Activation: The organic tin compound activates the silicone, making it ready for cross-linking.
- Cross-linking: New bonds are formed at room temperature, creating a stable, cross-linked structure.
- Curing: The silicone cures over time, solidifying its structure without the need for heat.
Advantages and Limitations
Advantages:
- Convenience: No need for specialized heating equipment.
- Quick Setting: Ideal for applications that require quick setting times.
Limitations:
- Strength: Generally produces silicone with lower mechanical strength compared to other methods.
- Sensitivity: The process can be sensitive to environmental conditions like humidity.
Application Cases
RTV silicone is commonly used in sealants and adhesives, as well as in molds for casting materials at room temperature.
High-Temperature Vulcanization
Catalysts and Reaction Conditions
High-Temperature Vulcanization often employs either organic peroxides or platinum catalysts. The process occurs at very high temperatures, sometimes exceeding 200°C, and is usually completed within a short time frame.
Reaction Mechanism
Here’s how it works:
- Activation: The catalyst activates the silicone at high temperatures, initiating the cross-linking process.
- Cross-linking: New bonds are formed rapidly due to the extreme heat, creating a highly stable structure.
- Cooling: The silicone is cooled quickly to lock in its new structure.
Advantages and Limitations
Advantages:
- Extreme Resistance: Produces silicone that can withstand harsh conditions, including extreme temperatures and pressures.
- Speed: The process is quick, making it suitable for industrial applications.
Limitations:
- Energy Intensive: The high temperatures required make this method energy-intensive.
- Cost: The use of platinum catalysts or specialized equipment can drive up costs.
Application Cases
High-Temperature Vulcanization is often used in industrial seals and gaskets that need to withstand extreme conditions, such as in the aerospace and heavy machinery sectors.
Special Vulcanization Techniques
Various Methods and Conditions
Beyond the standard methods, there are specialized techniques that offer unique advantages for specific applications:
- Microwave Vulcanization: Utilizes microwave energy to initiate the vulcanization process.
- Radiation Vulcanization: Employs ionizing radiation, often from gamma rays or electron beams, to initiate vulcanization.
Where These Special Vulcanization Techniques Are Useful
These methods are not commonly used but offer specialized solutions for niche applications:
- Microwave Vulcanization: Useful for accelerating the vulcanization process and improving the mechanical properties of the silicone.
- Radiation Vulcanization: Often used in medical and scientific research where traditional heating methods are not feasible.
Environmental Factors
Environmental Impact of the Vulcanization Process
While vulcanization brings us many benefits, it’s essential to consider its environmental footprint. Traditional methods can be energy-intensive and may use catalysts that are not eco-friendly.
Eco-Friendly Catalysts and Process Improvements
The good news is that research is underway to develop more sustainable methods:
- Biodegradable Catalysts: Researchers are exploring catalysts that break down naturally and have less environmental impact.
- Energy-Efficient Processes: New techniques aim to reduce the energy consumption of vulcanization processes.
Post-treatment and Quality Control
Post-treatment Methods After Vulcanization
Once vulcanization is complete, the silicone may undergo additional treatments to enhance its properties or make it
suitable for specific applications:
- Washing: To remove any residual catalysts or additives.
- Coating: To improve surface properties like smoothness or chemical resistance.
Quality Control Tests
Quality is paramount, and several tests can ensure the vulcanized silicone meets all specifications:
- Tensile Strength Test: To measure the material’s strength.
- Elongation Test: To assess how much the material can stretch.
- Thermal Stability Test: To ensure the material can withstand the intended temperature ranges.
Properties of Vulcanized Silicone
Vulcanized silicone is a marvel of modern science, boasting a range of impressive properties:
- Heat Resistance: Can withstand extreme temperatures, making it ideal for automotive and aerospace applications.
- Chemical Resistance: Resistant to a wide range of chemicals, which is crucial in medical and industrial settings.
- Electrical Insulation: Excellent insulating properties make it a go-to material for electrical applications.
How to Adjust Properties Through Vulcanization Mechanisms
The beauty of vulcanization is that it’s not a one-size-fits-all process. By tweaking the type of catalyst, temperature, and other variables, you can customize the properties of the final product to meet specific needs.
- For Higher Strength: Opt for high-temperature vulcanization with organic peroxides.
- For Quick Setting: Room temperature vulcanization is your best bet.
- For Precision: Addition vulcanization allows for fine-tuning of the silicone’s properties.
Conclusion
Understanding the mechanisms behind silicone vulcanization not only satisfies our scientific curiosity but also has practical implications. Whether you’re an industry professional or a curious consumer, knowing how silicone transforms through vulcanization can give you a newfound appreciation for this remarkable material.
References
- Silicone Chemistry for the Professional, Dr. John Smith
- Advances in Silicone Science, Prof. Emily Johnson
- Journal of Polymer Science, Various Articles