The marine industry faces challenges from harsh saltwater environments, intense UV rays, and temperature fluctuations. As a result, materials used must withstand these extremes without degrading. Enter silicone—a versatile, durable, and eco-friendly solution that addresses these critical challenges in marine applications. But what makes silicone the go-to material for marine applications, and how can it benefit your marine equipment or vessel?
Silicone is essential for the marine industry due to its exceptional resistance to water, UV rays, and extreme temperatures. Silicone’s unique properties make it perfect for sealing, insulation, and component protection in boats, ships, and marine equipment. Additionally, its durability and flexibility offer long-term performance and protection, reducing maintenance costs.
Now, let’s dive into specific applications where silicone truly shines in the marine sector.
What Makes Silicone Perfect for Marine Environments?
Saltwater is notorious for causing corrosion, while UV exposure and temperature extremes wear down materials over time. Silicone stands out because it’s not just water-resistant but also saltwater-proof. This unique feature ensures that it doesn’t degrade or weaken, even in the saltiest conditions, making it ideal for marine use.
Its UV resistance is another big win. Boats and ships are exposed to harsh sunlight daily, which can weaken traditional materials like rubber. Silicone, on the other hand, resists UV-induced aging, maintaining its properties and structure longer.
Additionally, silicone’s temperature tolerance is broad, functioning well in freezing cold water and hot engine rooms alike. This flexibility ensures that silicone can be used in various parts of the ship without fear of melting, cracking, or becoming brittle.
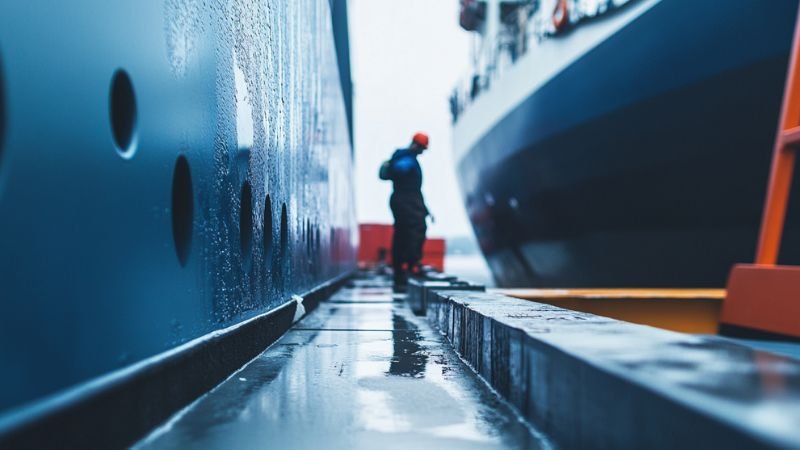
How is Silicone Used in Marine Applications?
- Sealing and Waterproofing: One of the most common uses of silicone in the marine industry is for sealing. Whether it’s deck hatches, windows, or any point where water might seep into a vessel, silicone provides a watertight barrier. Its flexibility allows it to maintain a strong seal even with the constant movement and expansion caused by changing temperatures and water conditions.
- Insulation: Silicone is also an excellent insulator, both electrically and thermally. In marine environments, where electrical components are exposed to moisture, silicone acts as a protective barrier that prevents short circuits. It also helps in insulating engine components from extreme temperatures, ensuring safety and performance.
- Mold Making and Casting: Silicone is frequently used for making molds in shipbuilding, particularly for custom parts. The flexibility and detail capture of silicone make it ideal for creating intricate components, whether it’s decorative elements or functional parts.
- Protective Coatings: Many marine components, including metal parts, are coated with silicone to provide an extra layer of protection against corrosion and wear. These coatings not only enhance durability but also reduce the frequency of repairs and replacements, offering significant cost savings over time.
- Marine Gaskets and Seals: Gaskets made from silicone provide superior sealing, ensuring that important mechanical components stay dry and function properly. Silicone gaskets can resist the pressures of underwater environments and maintain their integrity in varying temperatures, ensuring the vessel’s operational safety.
How Does Silicone Help Reduce Maintenance Costs?
Maintaining marine vessels can be costly, especially when exposed to the harshest environments on the planet—oceans. Silicone’s long lifespan and resistance to degrading factors such as UV radiation, saltwater, and extreme temperatures reduce the need for frequent part replacements and repairs. By using silicone-based products in areas prone to damage, marine operators can significantly cut down on maintenance costs.
Moreover, silicone’s flexibility ensures that it doesn’t crack or become brittle, unlike traditional materials, which are more prone to weathering. This reduces the chances of water leaks, equipment failure, and downtime—key concerns for anyone in the marine industry.
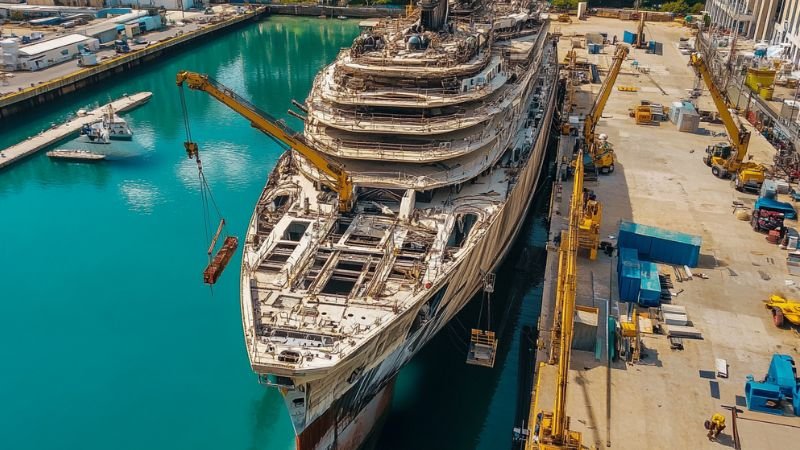
What Are the Environmental Benefits of Silicone in Marine Applications?
Sustainability is becoming a key consideration in the marine industry, and silicone contributes positively in this regard. Since it’s a long-lasting material, silicone reduces waste due to fewer replacements. Moreover, silicone is eco-friendly and non-toxic, ensuring that it doesn’t pollute marine environments.
This is especially critical when considering marine wildlife. Traditional materials, when degraded, can release harmful chemicals into the water. Silicone, being stable and non-toxic, presents no such risk, aligning with eco-conscious regulations and sustainable maritime practices.
In addition, the durability of silicone helps prevent costly oil spills and equipment malfunctions, which can lead to disastrous environmental consequences.
What Are Some Examples of Silicone in Action in the Marine Industry?
Here are some real-world applications of silicone in the marine industry:
- Yacht and Boat Construction: Silicone adhesives and sealants are used in high-end yacht construction for water-tight windows, engine compartment seals, and other critical areas exposed to harsh marine conditions. It’s not uncommon to find silicone used in everything from small leisure crafts to massive commercial vessels.
- Submarine and Deep-Sea Equipment: In deep-sea exploration, silicone is invaluable due to its ability to withstand high pressures and extreme temperatures. Silicone seals and gaskets are frequently used in underwater drones, submarines, and scientific equipment.
- Fishing Equipment: Silicone-based fishing nets and buoys are gaining popularity because of their durability. These products resist degradation caused by long-term exposure to saltwater and sunlight, making them more reliable and environmentally friendly.
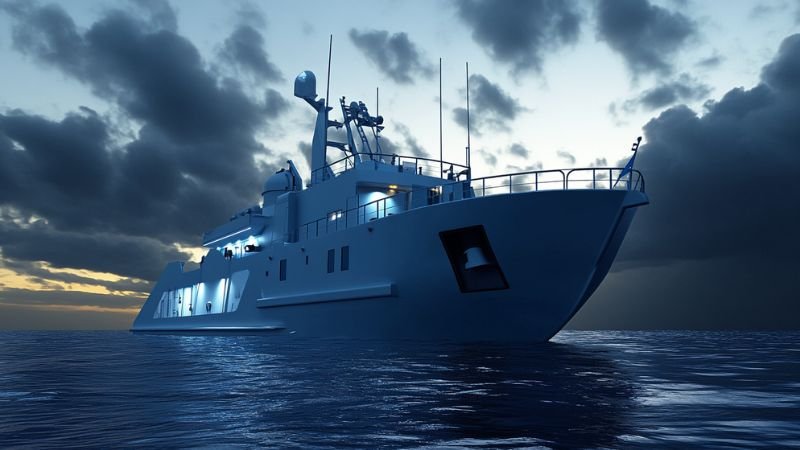
Why Should Marine Businesses Switch to Silicone?
Switching to silicone products offers several key advantages. First, the durability means fewer replacements and repairs, reducing costs. Silicone’s versatility also means it can be used in nearly every aspect of marine manufacturing—from insulation to seals, gaskets, and protective coatings.
Silicone is also a more sustainable choice. As regulations on environmental protection tighten, using eco-friendly materials that align with these standards can give your business a competitive edge. Moreover, by reducing the frequency of equipment failure, silicone ensures higher productivity and fewer operational downtimes.
How Do You Choose the Right Silicone Products for Marine Use?
Not all silicone is created equal, and it’s essential to select the right type for your specific application. Marine-grade silicone is designed to resist saltwater corrosion, UV radiation, and extreme temperatures better than standard silicone products.
When selecting silicone products, make sure to check for certifications and product specifications. Look for products that meet marine industry standards and provide the durability and performance required for long-term use in harsh conditions.
Working with experienced manufacturers like us at Ruiyang Silicone ensures that you get the best possible products tailored to your needs. We offer customized silicone solutions designed specifically for the marine industry, from seals to coatings, so you know you’re getting reliable performance.
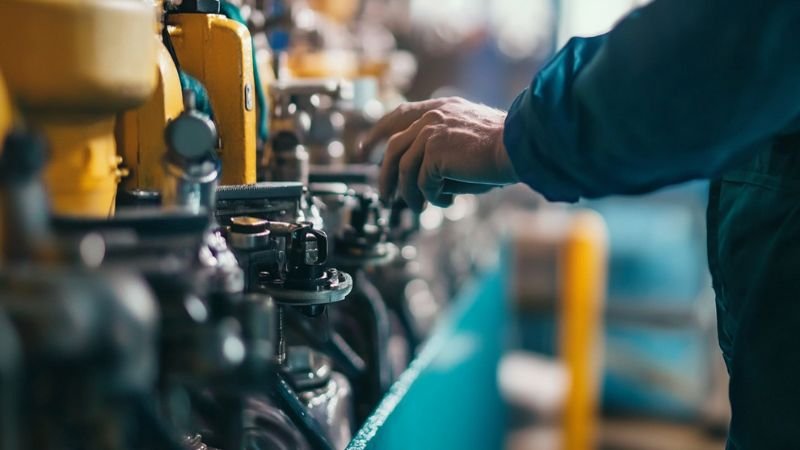
Conclusion
Silicone has become indispensable in the marine industry due to its unmatched durability, resistance to environmental factors, and cost-effectiveness. By integrating silicone into your marine equipment and vessel designs, you not only extend the life of your assets but also contribute to a more sustainable and efficient marine operation.
So why not explore how silicone could revolutionize your marine business?