Silicone’s ability to conduct heat varies depending on its composition and form. Generally, silicone has lower thermal conductivity compared to metals like copper and aluminum. This makes it particularly suitable for applications where thermal insulation is critical, such as in electronics, automotive components, and kitchenware.
What is Thermal Conductivity?
Thermal conductivity measures how effectively a material transfers heat. Silicone’s capacity to dissipate heat effectively is influenced by factors such as its polymer type (such as PDMS), crosslinking density, and the presence of fillers. These factors affect how well silicone manages heat in different environments.
Factors Affecting Thermal Conductivity
Several factors impact silicone’s thermal conductivity, each playing a crucial role in its ability to transfer heat:
Composition and Structure
- Silicone Polymers: The type of silicone polymer used, such as polydimethylsiloxane (PDMS) or phenyl-based silicones, affects its thermal conductivity. Generally, silicones with higher molecular weights tend to have lower thermal conductivities.
- Crosslinking Density: Highly crosslinked silicone structures typically have lower thermal conductivity due to reduced molecular mobility.
- Fillers and Additives: The addition of fillers like ceramics, metals, or carbon-based materials can either enhance or diminish thermal conductivity, depending on their composition and how well they are dispersed within the silicone matrix.
Temperature and Environmental Conditions
Silicone’s thermal conductivity can vary significantly with changes in temperature. Understanding the operating temperature range and environmental factors such as humidity and pressure is crucial for optimizing its performance.
Thickness and Geometry
The thickness and shape of silicone components also affect thermal conductivity. Thinner materials generally conduct heat more efficiently, while complex shapes can alter heat flow patterns.
Surface Finish and Contact Resistance
Surface finish and the resistance between mating surfaces influence thermal conductivity, especially in applications requiring efficient heat transfer interfaces like thermal pads or heat sinks.
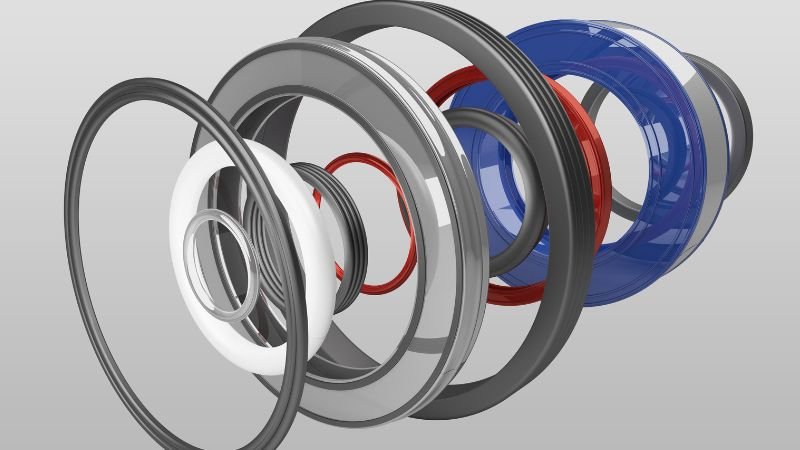
Thermal Properties of Silicone
Silicone exhibits a range of thermal properties that make it versatile for various industrial applications:
General Thermal Conductivity Range
Silicone typically has a thermal conductivity ranging from 0.1 to 0.4 W/m·K. This is lower than metals but higher than most organic materials. It remains stable across temperatures from -50°C to 200°C, making it suitable for diverse applications from electronic enclosures to medical devices.
While metals like copper or aluminum have much higher thermal conductivities (ranging from 100 to 400 W/m·K), silicone compensates with properties such as flexibility, durability, and electrical insulation, which are advantageous in many applications.
Comparison with Other Materials
Silicone’s thermal conductivity exceeds that of most organic materials like plastics, rubbers, and polymers, making it suitable for applications requiring moderate heat dissipation. However, it falls short compared to metals, limiting its use in applications requiring very high heat transfer rates.
Thermal Stability and Reliability
Silicone maintains stable thermal properties over a wide temperature range, typically from -50°C to 200°C or higher, depending on its formulation and application conditions. This stability makes silicone well-suited for both low-temperature and high-temperature applications, including automotive engine seals, electronic enclosures, and medical devices.
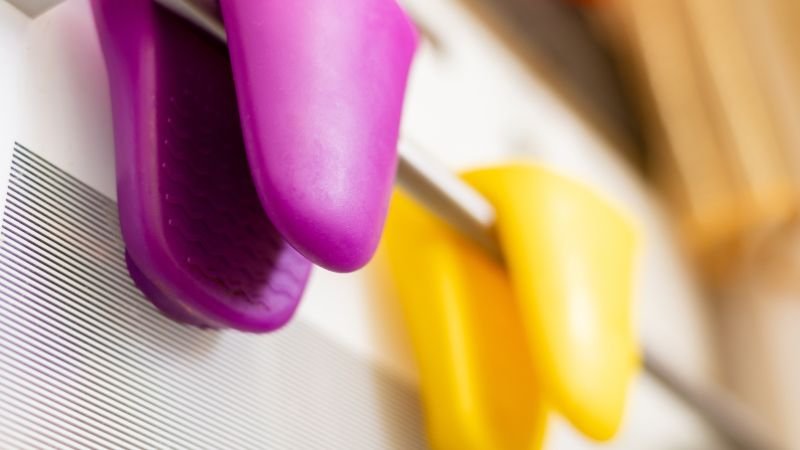
Applications of Silicone with High Thermal Conductivity
Silicone’s thermal properties make it indispensable in several key industries where efficient heat management is critical. Here are some notable applications:
Electronics Industry
- Thermal Management in Electronics: Silicone is widely used in electronic devices for thermal management purposes. It is employed in thermal pads, thermal interface materials (TIMs), and heat sinks to dissipate heat generated by components such as CPUs, GPUs, and power electronics.
- Encapsulation and Insulation: Silicone’s electrical insulation properties combined with moderate thermal conductivity make it ideal for encapsulating and insulating electronic components.
Automotive Sector
- Engine Components: Silicone gaskets, seals, and hoses withstand high temperatures in automotive engines, preventing fluid leaks and maintaining engine efficiency.
- Thermal Interface Materials: Silicone-based thermal pastes and adhesives bond heat sinks to electronic components and manage heat in automotive electronics.
Medical and Healthcare
- Medical Devices: Silicone is used in medical devices requiring efficient heat dissipation, such as patient monitoring equipment and diagnostic devices.
- Prosthetics and Implants: Silicone prosthetics benefit from biocompatibility, durability, and thermal stability, ensuring patient comfort and reliability.
Industrial Applications
- Sealing and Insulation: Silicone seals and gaskets in industrial equipment withstand extreme temperatures and ensure effective sealing.
- Heat Transfer Solutions: Silicone-based materials in industrial heat exchangers, HVAC systems, and renewable energy applications enhance heat transfer and thermal management.
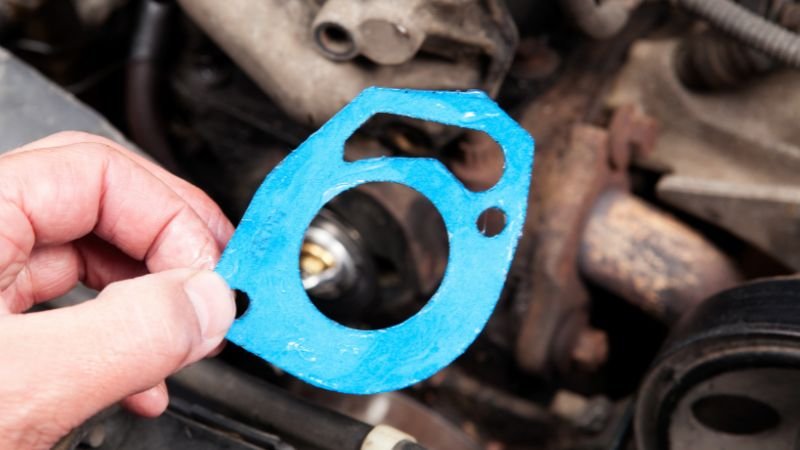
Advantages of Silicone’s Thermal Conductivity
Silicone offers several advantages in thermal conductivity and heat management:
Flexibility and Durability
Silicone’s flexibility allows it to conform to irregular surfaces, making it suitable for components that expand or contract due to temperature changes. It maintains mechanical properties over a wide temperature range, ensuring long-term performance.
Electrical Insulation
Silicone exhibits excellent electrical insulation alongside thermal conductivity, ideal for applications requiring both thermal management and electrical isolation.
Biocompatibility and Safety
In medical applications, silicone’s biocompatibility ensures compatibility with biological tissues, minimizing risks of allergic reactions. It meets regulatory requirements for medical devices, offering a safe and reliable choice.
Resistance to Environmental Factors
Silicone remains stable in harsh conditions such as UV radiation, ozone exposure, and chemical environments, enhancing its durability in outdoor and industrial applications. It resists moisture degradation and maintains thermal properties over time.
Customization and Versatility
Silicone formulations can be tailored with additives and fillers to meet specific thermal conductivity requirements while maintaining mechanical strength and elasticity.
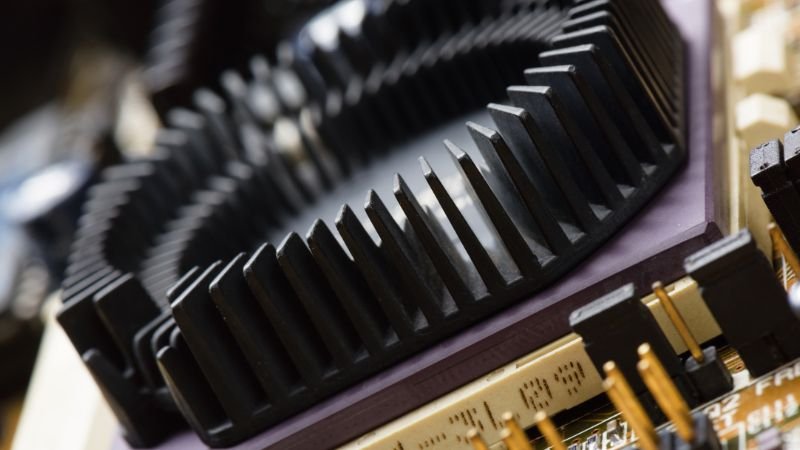
Challenges and Limitations
Despite its advantages, silicone faces challenges in thermal conductivity:
Lower Thermal Conductivity Compared to Metals
Silicone’s thermal conductivity is significantly lower than metals like copper or aluminum, limiting its use in applications requiring very high heat transfer rates.
Dependency on Formulation and Processing
Silicone’s thermal conductivity varies with formulation, additives, and processing conditions like curing temperature, requiring careful control during manufacturing.
Interface Resistance and Contact Issues
Efficient heat transfer demands minimizing interface resistance between silicone and other materials. Proper surface preparation and use of thermal interface materials (TIMs) are essential for optimizing performance.
Application-Specific Challenges
In high-power electronics or demanding industrial environments, silicone’s thermal conductivity may not meet stringent heat dissipation requirements. Engineers balance conductivity with other material properties for overall performance.
Cost Considerations
Enhanced thermal conductivity silicone formulations may incur higher production costs. Cost-effectiveness analysis is crucial when selecting silicone materials for specific applications.
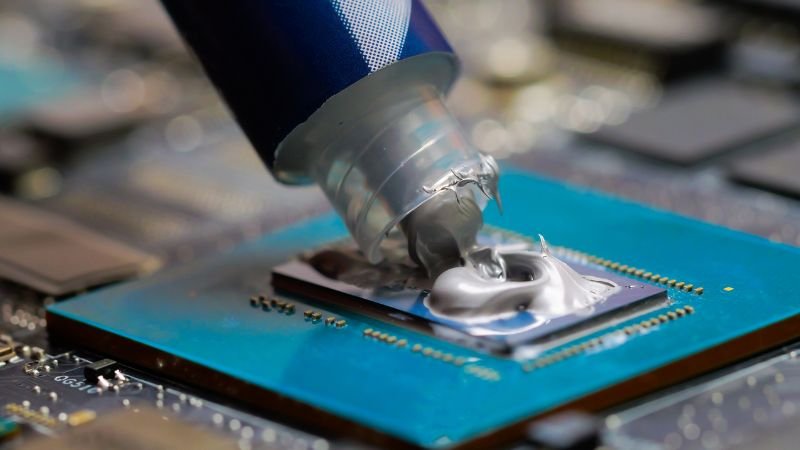
Future Trends and Innovations
Research continues to enhance silicone’s thermal properties and expand its applications:
Advanced Additives and Fillers
Ongoing research explores novel additives like graphene and carbon nanotubes to improve silicone’s thermal conductivity while maintaining other properties.
Nanostructuring and Composite Materials
Nanostructuring techniques promise precise thermal property control through nanocomposites and coatings, potentially achieving higher thermal conductivities.
3D Printing and Customization
Additive manufacturing enables complex silicone structures with optimized thermal conductivity for specific applications, advancing thermal management solutions.
Integration in Emerging Technologies
Silicone’s thermal properties are crucial in emerging sectors like electric vehicles and renewable energy systems, driving demand for high-performance materials.
Environmental Sustainability
Focus on eco-friendly silicone formulations aims to minimize environmental impact through sustainable material sourcing and recycling practices.
These advancements position silicone as a versatile material in thermal management, ensuring enhanced performance, reliability, and sustainability across diverse applications.
Sources: