Silicone Transfer Molding (STM) is a reliable and efficient method for producing high-precision silicone parts.
This article explores the STM process, including its working principles, key steps, and applications. We also discuss its advantages, limitations, and how it compares to other molding techniques. Moreover, we answer common questions to help you better understand this manufacturing method.
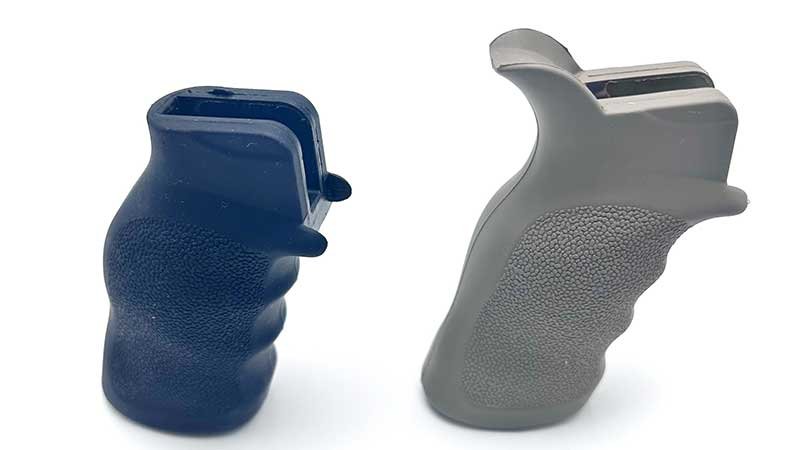
What Is Silicone Transfer Molding?
Silicone Transfer Molding (STM) is a manufacturing process used to create high-precision silicone parts, such as handles for medical devices or encapsulations for electronic components. It is particularly well-suited for products that require complex shapes and tight tolerances. The STM process injects uncured silicone into a heated mold under pressure, and it then cures to form the final product. This method is favored for its flexibility and durability, making it especially ideal for applications that require biocompatibility, such as in the medical field.
How Does Silicone Transfer Molding Work?
Silicone transfer molding is a highly efficient and precise manufacturing process. By combining heat and pressure, this method ensures excellent material flow and detailed mold replication. From mold preparation to final post-processing, each step plays a crucial role in achieving superior product performance. Here are key stages of silicone transfer molding.
Mold Preparation: The Foundation of Quality
Mold preparation is the first step.
The mold is usually made of high-strength steel or aluminum, and mold determines the product’s shape and quality. Steel molds are often chosen for their durability, while aluminum molds allow shorter cycle times. The mold must be manufactured with high precision, so the part comes out just right.
Before production starts, the mold is cleaned and coated with a release agent like silicone-based sprays or PTFE coatings. This coating prevents sticking, easing product removal and extending mold life.
Material Preparation: Getting Silicone Ready
Silicone transfer molding uses a mixture of base silicone and a curing agent. These components must be blended in precise proportions to ensure uniform chemical properties in the final product. Common mixing ratios range from 10:1 to 20:1 (base silicone to curing agent), depending on the specific formulation and desired properties.
Silicone material can come in various forms, such as powder, granules, or sheets. High-consistency rubber (HCR) is commonly used in transfer molding due to its better mechanical properties compared to liquid silicone rubber (LSR).
After mixing, the pre-measured silicone is placed into the transfer molding machine’s reservoir (transfer pot), which is typically designed with a pre-heating function to improve flowability before transfer.
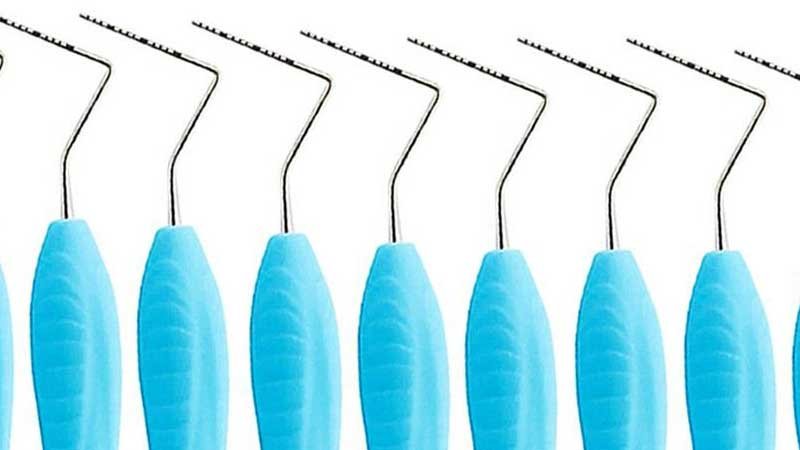
Transfer Stage: Shaping the Silicone
With the mold prepared and the silicone loaded, the mold is closed. The machine’s plunger then applies pressure to the heated silicone in the transfer pot. Typical transfer pressures range from 500 to 2,000 psi (pounds per square inch), depending on the viscosity of the silicone and the complexity of the mold design.
Heat reduces the silicone’s viscosity, making it flow like a liquid. Under pressure, the material moves through the gate and runner system, filling every cavity of the mold. To optimize flow and prevent air entrapment, venting channels are often designed into the mold to allow trapped gases to escape.
This combination of heat and pressure ensures that even the finest details of the mold are accurately replicated.
Curing: Giving the Part Its Strength
Once the mold is filled, the next step is curing, also known as vulcanization.
The heat from the transfer process activates the curing agent, triggering a cross-linking reaction between silicone molecules. Curing temperatures typically range from 150°C to 200°C (302°F to 392°F), with curing times varying from 30 seconds to several minutes depending on the thickness of the part.
This chemical process transforms soft silicone into a firm, permanent shape, giving the molded part strength, elasticity, and durability. For parts requiring higher mechanical strength, post-curing in an oven at 200°C for several hours may be necessary.
Demolding and Ejection: Releasing the Final Product
After curing, the mold opens.
To remove the finished silicone part, ejector pins are placed within the mold. The placement and pressure of these pins must be carefully controlled to prevent deforming the part.
These pins gently push the molded piece out without causing damage. In some cases, a vacuum-assisted demolding system is used to reduce stress on the part during removal.
Careful handling during this step is essential to maintain the integrity of the part.
Post-Processing: The Final Touch
Freshly molded silicone parts may have excess material along the mold’s parting line, known as flash. This needs to be trimmed during post-processing. Flash thickness typically ranges from 0.05 mm to 0.2 mm, depending on mold precision and clamping force during molding.
Besides, additional surface treatments or quality inspections may be required. Common post-processing methods include plasma treatment to enhance surface adhesion for bonding applications and cryogenic deflashing, where parts are frozen and tumbled to remove excess material.
These final steps ensure that the silicone parts meet all necessary dimensional and aesthetic standards.
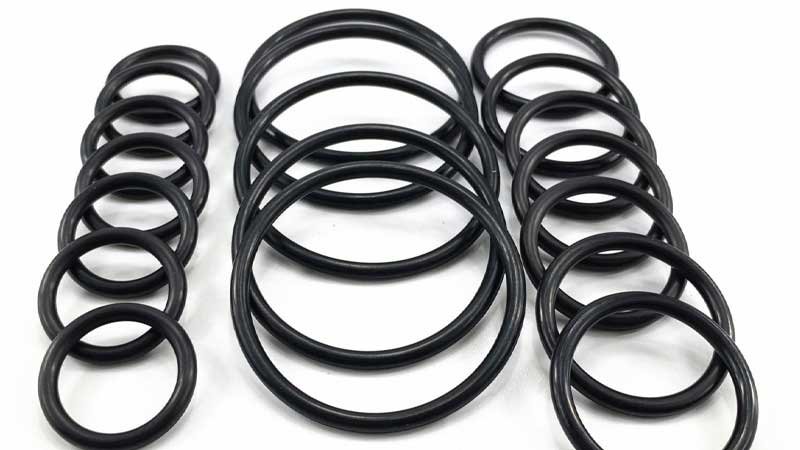
Advantages and Limitations: Weighing the Pros and Cons
Silicone transfer molding offers flexibility and high-quality results, making it ideal for many industries. However, like any manufacturing process, it has both advantages and limitations that must be considered.
Advantages of Silicone Transfer Molding
- Flexibility and Durability: Silicone transfer molding is ideal for producing parts with complex shapes. The molding process allows for intricate designs and detailed features that would be difficult to achieve with other methods.
- Ease of Insert Integration: It is easy to integrate inserts or metal components directly into the silicone parts during molding. This reduces the need for additional assembly steps, saving time and labor costs.
- Simple Design and Controllable Costs: The overall design of silicone transfer molding molds is relatively simple, and the process can be cost-effective, especially for medium to small batch production. It offers a good balance between cost and performance for specific applications.
Limitations of Silicone Transfer Molding
- Longer Curing Time: The curing time for silicone transfer molding can range from 1 to 15 minutes, and it is longer than injection molding. This can slow down production, especially for high-volume runs.
- Material Waste: The material preparation and transfer stages can result in some waste. This can impact efficiency and increase material costs.
- Air Trapping: The air may be trapped during the transfer process. This can lead to defects like bubbles in the final product, affecting its quality. Proper venting and careful control of the process are needed to prevent this issue.
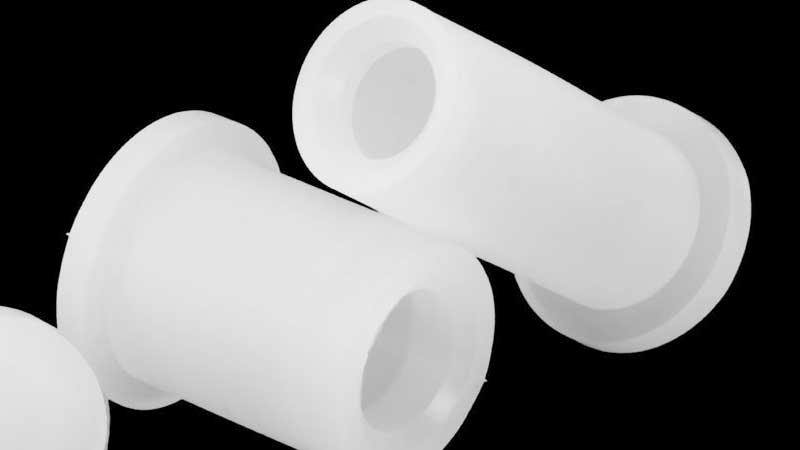
Applications of Silicone Transfer Molding
Silicone Transfer Molding is widely used across various industries due to its flexibility and ability to integrate metal inserts. Here are some of the key applications:
Industry | Applications |
Medical | Surgical instrument handles and implant components, due to biocompatibility and temperature resistance. |
Electronics | Electronic components, to protect circuits from environmental factors. |
Automotive | Hydraulic seals and face seals, suitable for sharp edges and complex shapes. |
STM’s ability to create detailed, high-performance parts makes it ideal for these industries, providing durable and reliable components.
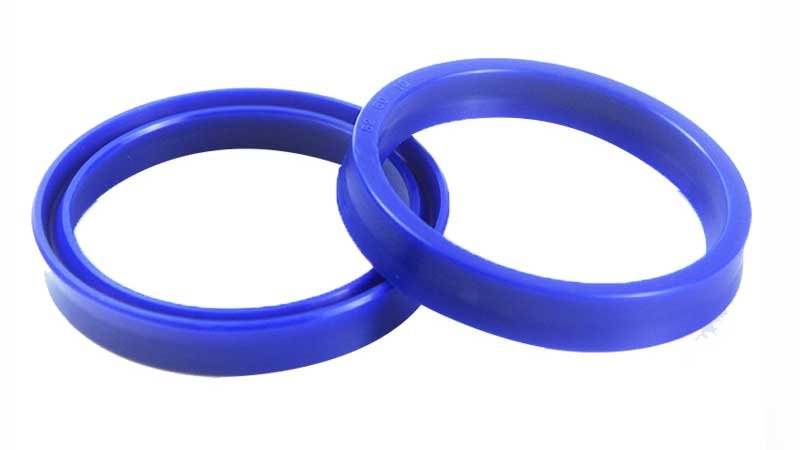
Frequently Asked Questions
Here are some common questions to help readers better understand Silicone Transfer Molding(STM):
What is the cost of STM?
The cost of STM depends on the batch size and complexity of the part. It is generally higher than compression molding due to the cost of equipment and materials.
How long does STM take?
Each cycle typically takes around 30-45 seconds, with curing times ranging from 1 to 15 minutes, depending on the size of the part.
Is STM suitable for medical devices?
Yes, STM is widely used in the medical industry due to its biocompatibility and temperature resistance, making it ideal for producing surgical handles, implants, and other medical components.
How is STM different from injection molding?
STM uses lower pressure (1500-2000 psi), making it more suitable for medium to small batch production and complex shapes. In contrast, injection molding uses higher pressure and is more efficient for large-scale production.
Conclusion
Silicone Transfer Molding is a versatile technique that offers precision, durability, and flexibility. While it has some limitations, such as longer curing times and potential material waste, its ability to create complex shapes and integrate inserts makes it a valuable solution for many industries. Understanding the STM process and its benefits can help manufacturers choose the best molding method for their needs.