Whether it’s a simple logo or a complex design, the surface patterns on silicone products are not just for aesthetics. They serve functional purposes, such as providing grip, enhancing visual appeal, and even adding an extra layer of safety.
The process of creating surface patterns on silicone products involves various advanced techniques that ensure durability and precision. From traditional methods like engraving and embossing to modern techniques like laser etching and chemical treatments, each method has its own set of benefits and applications.
Let’s explore some of the most common and effective surface pattern processing techniques used in the silicone industry.
What Are The Different Techniques For Silicone Surface Pattern Processing?
Creating surface patterns on silicone involves several techniques, each suited for different types of designs and applications. Here are some of the most popular methods:
1. Engraving
Engraving is one of the oldest techniques used for creating patterns on silicone products. This method involves removing material from the surface to create a design. It’s often done using a CNC (Computer Numerical Control) machine, which ensures precision and consistency. Engraving is ideal for creating deep, permanent patterns that won’t wear off easily. It’s commonly used for logos, serial numbers, and intricate designs.
Benefits of Engraving
- Precision: Provides highly accurate patterns.
- Durability: Patterns are permanent and resistant to wear.
- Versatility: Suitable for a wide range of products and designs.
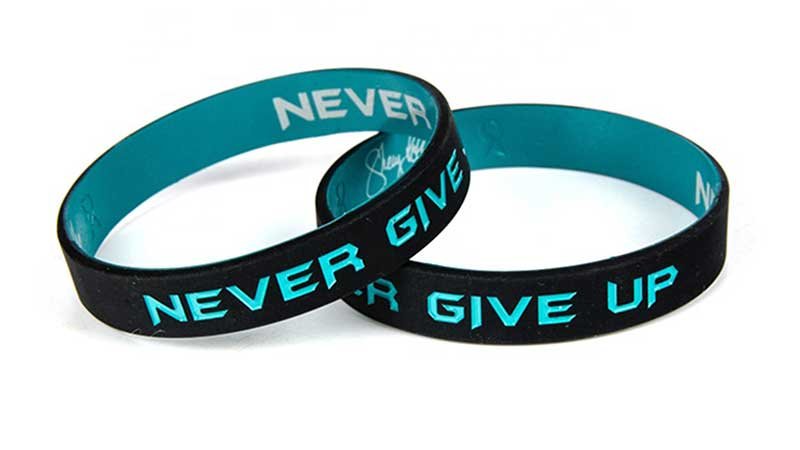
2. Embossing
Embossing involves pressing a pattern into the silicone surface, creating a raised design. This technique is particularly useful for adding texture to products, which can improve grip and aesthetic appeal. Embossing is often used in kitchenware and baby products, where a non-slip surface is beneficial. The process can be done using heat and pressure, ensuring the pattern is durable and long-lasting.
Benefits of Embossing
- Texture: Adds a tactile element to the product.
- Grip: Improves the functionality of products like kitchenware and baby items.
- Aesthetic Appeal: Creates visually appealing designs.
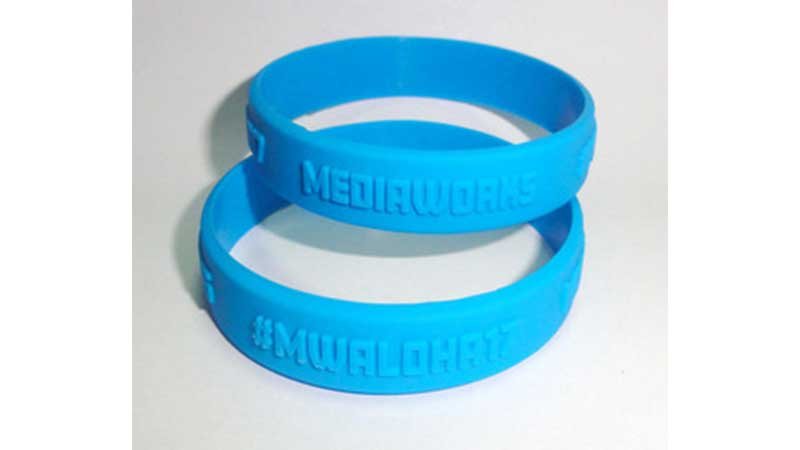
3. Laser Etching
Laser etching is a modern technique that uses a laser to burn a pattern into the silicone surface. This method offers high precision and can create very detailed designs. Laser etching is also faster than traditional methods like engraving and embossing, making it ideal for large-scale production. This technique is widely used in the electronics industry for labeling and branding purposes.
Benefits of Laser Etching
- Speed: Fast and efficient for large-scale production.
- Detail: Capable of creating intricate and detailed patterns.
- Non-Contact: No physical contact with the product, reducing the risk of damage.
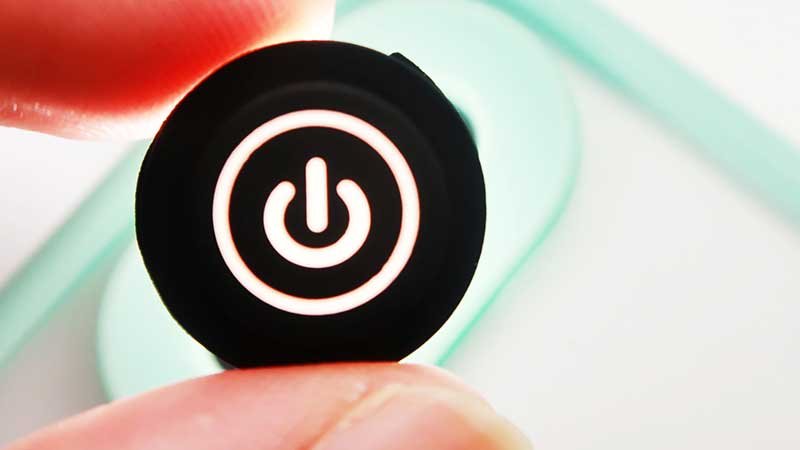
4. Screen Printing
Screen printing involves applying ink through a mesh screen to create a pattern on the silicone surface. This technique is highly versatile and can be used to create both simple and complex designs. Screen printing is commonly used for adding colorful patterns and logos to products. It’s particularly popular in the fashion and promotional products industries due to its cost-effectiveness and ability to produce vibrant colors.
Benefits of Screen Printing
- Color Variety: Allows for vibrant, multi-color designs.
- Cost-Effective: Ideal for large runs with complex designs.
- Flexibility: Can be used on various types of silicone products.
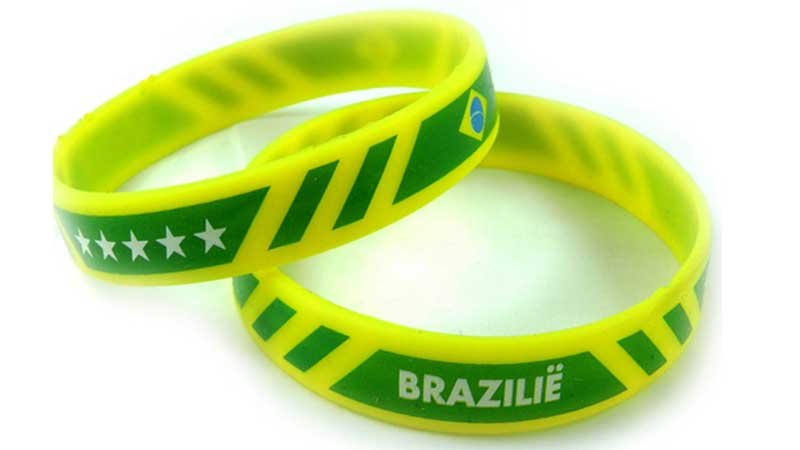
5. Pad Printing
Pad printing is another popular technique for adding patterns to silicone products. It involves transferring ink from a silicone pad onto the product’s surface. This method is highly accurate and can be used to print on irregularly shaped surfaces. Pad printing is often used in the automotive and medical industries, where precision is crucial.
Benefits of Pad Printing
- Accuracy: Highly precise, even on irregular surfaces.
- Adaptability: Suitable for small and large products.
- Consistency: Ensures uniform patterns across multiple items.
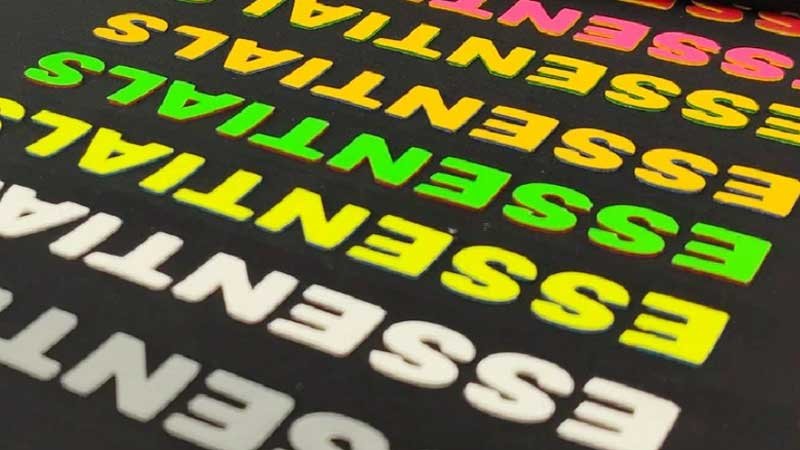
6. Chemical Treatments
Chemical treatments can be used to alter the surface of silicone products, creating patterns or textures. These treatments involve applying a chemical solution to the surface, which reacts with the silicone to create the desired effect. Chemical treatments are often used to improve the adhesion of inks or coatings, making them more durable and long-lasting.
Benefits of Chemical Treatments
- Adhesion: Improves the durability of inks and coatings.
- Texture: Can create unique surface textures.
- Customization: Offers a range of effects depending on the chemical used.
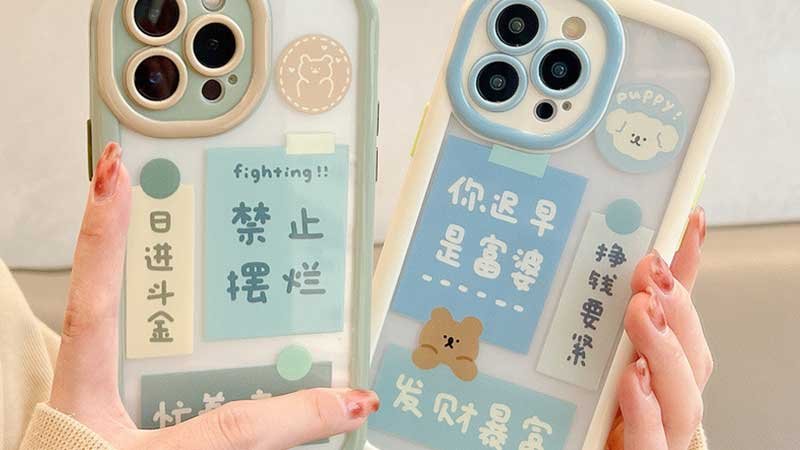
Comparison of Silicone Surface Pattern Processing Techniques
Here’s a quick comparison of the different silicone product surface pattern processing techniques:
Technique | Precision | Durability | Speed | Design Complexity | Application |
---|---|---|---|---|---|
Engraving | High | Very High | Medium | High | Logos, serial numbers, intricate designs |
Embossing | Medium | High | Medium | Medium | Kitchenware, baby products, textured surfaces |
Laser Etching | Very High | High | Very High | Very High | Electronics, branding, detailed designs |
Screen Printing | High | Medium | High | Very High | Fashion items, promotional products, colorful patterns |
Pad Printing | Very High | Medium | High | High | Automotive, medical devices, irregular surfaces |
Chemical Treatments | Medium | High | Medium | Medium | Improving ink adhesion, creating unique textures |
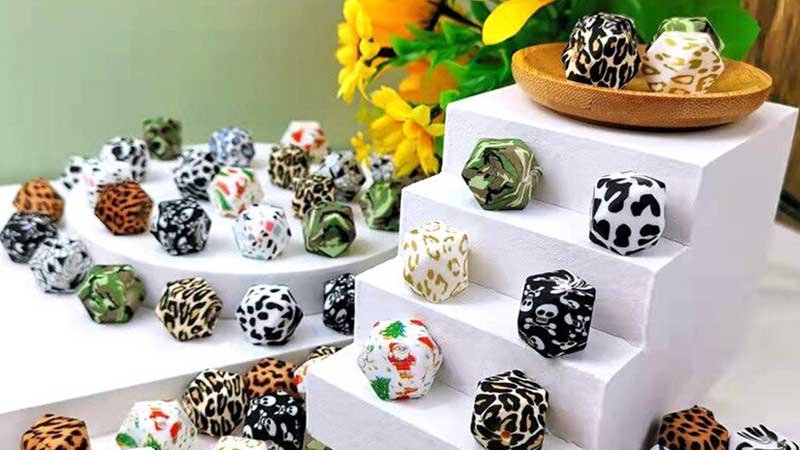
How To Choose The Right Technique?
Choosing the right surface pattern processing technique depends on several factors, including the type of product, the desired pattern, and the intended use. Here are some tips to help you make an informed decision:
1. Consider The Product’s Function
Think about how the product will be used. For example, if you need a non-slip surface for kitchenware or baby products, embossing might be the best option. If you’re looking for detailed branding or logos, laser etching or engraving could be more suitable.
2. Evaluate The Design Complexity
The complexity of the design can also influence your choice of technique. Laser etching and screen printing are ideal for intricate patterns, while embossing and pad printing work well for simpler designs.
3. Assess Durability Requirements
Consider how durable the pattern needs to be. Engraving and embossing create patterns that are resistant to wear and tear, making them suitable for products that will be used frequently. Screen printing and pad printing, on the other hand, may not be as durable but offer greater flexibility in terms of color and design.
4. Think About Production Volume
The volume of production can also impact your decision. Laser etching and screen printing are fast and efficient, making them ideal for large-scale production. Engraving and embossing, while slower, are better suited for smaller batches or custom orders.
Conclusion
Understanding the various silicone product surface pattern processing techniques can help you make informed decisions for your business. Whether you’re looking to add aesthetic value, improve functionality, or enhance branding, there’s a technique that suits your needs. By choosing the right method, you can ensure that your silicone products stand out in the market and meet the high standards your customers expect.
For more detailed information on these techniques, check out these resources:
- Engraving Techniques in Silicone Manufacturing
- The Benefits of Embossing for Silicone Products
- How Laser Etching Enhances Silicone Product Design
- Screen Printing on Silicone: A Comprehensive Guide
- Pad Printing for Precision Patterns
- Chemical Treatments for Silicone Surface Enhancement